
Sign In
Chick Qwik-Loks & One-Loks at James Brown Industries Cut Manufacturing Costs By Three-Quarters
20-05-2014
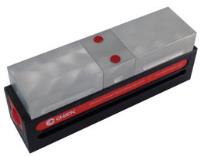
Cwmbran-based subcontractor, James Brown Industries, receives two-thirds of its business from companies in the oil and gas sector. Earlier this year, one customer significantly increased the volume of stainless steel and nickel alloy components it was ordering for daily Kanban delivery in boxes containing anything from 8- to more than 600-off. In addition, new component variants were being added.
These dedicated, twin-pallet, 3-axis vertical machining centres (VMCs) on the shop floor were struggling to keep up, even working around the clock. The problem was solved by adopting new, more advanced component fixturing methods supplied by 1st Machine Tool Accessories (1st MTA).
A family of 28 parts was originally involved, which increased to 32, each part having to be machined on four, five or six faces. Not only were those numbers of set-ups needed per component, but the variety and quantities of parts meant that four or five changeovers were needed daily on each machine, taking three to four hours every time.
Moreover, the parts are cost-sensitive and the customer was looking for a price reduction.
Clearly something had to be done. An engineer from 1st MTA was called in to advise on how to fixture the components more efficiently on the Doosan VC510 VMCs with a view to reducing spindle idle time. The aim was not only to ensure that parts flow smoothly out of the factory to the customer, but also to reduce production cost per part.
A suite of Chick Workholding Qwik-Lok System 5 twin-station workholding systems provided the answer. Three are mounted side by side on each machine pallet, replacing the same number of conventional wind-up vices, each of which held one component.
The Qwik-Lok has two clamping stations that are tightened with a single handle against a fixed central jaw, doubling the number of components that can be held. However, by superimposing a CHICK faceplate with 24 clamping stations, up to 72 smaller parts can be secured on each machine pallet.
Normally, to stand a chance of setting up so many components at once on a VMC, a rotary table and tailstock supporting a trunnion offering four clamping surfaces would be needed. This would add extra cost and might compromise rigidity and accuracy, especially when cutting tough metals.
The faceplates were machined in-house by the subcontractor to convert each twin-station workholding system into three similar but smaller twin stations, each of the six positions capable of holding up to four parts. Thus 24 parts are held per Qwik-Lok, 72 per pallet. Clamping is achieved by tightening Allen bolts on three central pillars which push pads into components on either side to force them against the fixed jaws. This element of the solution was also introduced by 1st MTA.
Eight different cutters on average are needed per cycle and with more components under the spindle, fewer tool changes are needed overall, so cycle time per part is lower. Fixturing more components also means that set-up time is a smaller proportion of the floor-to-floor time per component. In practice, 28 parts come off a machine per hour now, compared with 7 parts per hour previously - a four-fold increase in productivity.
Managing director Martin Brown, who has owned the firm since 2004, sad, "A fixed overhead turning out four times as many components translate into a reduction of 75 per cent in the value-added manufacturing cost of a part.
"Materials like Duplex and Hastelloy are quite expensive, so account for around one-third of a component by value, but cutting the other two-thirds by 75 per cent still halves the overall cost of the part.
"This is a massive saving. It allows us to hold or reduce the prices we charge customers and at the same time invest more in up to date plant to generate even greater efficiencies.
"It also means we can quote more competitively for new work and we are already winning additional contracts as a result."
An extra benefit of being able to fixture so many components is that the longer cycle time per pallet normally allows the next batch of components to be set up on the second pallet while the previous batch is being machined.
The worst-case at Cwmbran is a 15-minute delay between cycle end and pallet change. Comparing this with the previous three-to four-hour changeovers, there is a 12- to 16-fold saving, increasing production time by several hours per day across all the machines.
Another factor that speeds set-up time is the ability of the CHICK jaws to provide a reliable datum face when loading parts.
With the old vice jaws, it was neccesary to clock into position some tightly toleranced parts, such as stainless steel manifold blocks on which the seal faces have to be machined to within ±0.05 mm. Skilled operators formerly had to attend the machines to position components accurately, but now less experienced staff can load the machines, leading to further savings.
A fourth Doosan twin-pallet, 3-axis VMC at Cwmbran has been similarly set up with three CHICK Qwik-Loks per pallet to streamline machining of castings for off-road braking systems, which is another main area of the subcontractor's business.
There are 13 Doosan VMCs in use throughout the factory. Another CHICK workholding product is to be found on many of them, namely a One-Lok quick-acting vice. The benefit of this workholding device is that the moveable jaw can be slid over a ratchet to within a few handle turns of the component, allowing it to be secured much faster than when a conventional wind-up vice was used.
One-Loks increase productivity when machining one-offs and small batches and share the Qwik-Lok's virtue of accurate component location. One, two or three One-Loks are used per machine pallet at James Brown Industries and 1st MTA has to date supplied 25 of these clamping units to the subcontractor.
The Chick One-Lok and Chick System 5 range are available from 1st MTA.
For more information on Chick Qwik-Loks & One-Loks at James Brown Industries Cut Manufacturing Costs By Three-Quarters talk to 1st Machine Tool Accessories
Enquire Now
List your company on FindTheNeedle.