
Sign In
Don’t wait to automate
15-03-2021
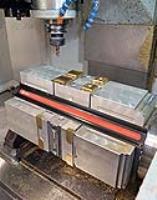
One of the repercussions of Covid-19 has been a widespread discussion about bringing more manufacturing back to the UK, and rightly so in the view of workholding and automation specialist 1st Machine Tool Accessories (www.1mta.com). But is reshoring large amounts of production realistic in the short term, or is industry unprepared to cope with the higher demand and respond to the need to make parts more cost-effectively?
It is generally accepted that the manufacturing sector in the UK is behind its competitors in Europe, the US and especially the Far East when it comes to the adoption of automation in its factories. There is no lack of knowledge, just equipment on the shop floor, although there has been significant effort in recent years to redress the situation and raise competitiveness.
1st MTA is a keen advocate of automating machine tools to achieve savings and regards some level of unattended operation to be crucial for cost-efficient production and generating a healthy profit. However, the company stresses that big investment in expensive robotics is not a prerequisite for success or justifiable in smaller factories. Correct equipment for an application could be as simple as employing hydraulic rather than manual clamping to actuate jaw closure; using a rotary table to add a fourth and perhaps a fifth CNC axis to a 3-axis machining centre so that parts can be made in fewer operations or maybe in one hit; or choosing a full-length bar magazine rather than a short barfeed to automate a lathe.
Whether producing prismatic or rotational components, return on investment (ROI) in such relatively inexpensive automation equipment can be surprisingly rapid, although the operative word is relatively. It is important for a manufacturer to research the market carefully, quiz potential suppliers and avoid rushing into choosing a lower initial investment for a shorter ROI. If it falls short in achieving what is expected, it can actually result in a longer payback period. Then the user is stuck with the worst of both worlds – a less effective automation solution and inferior cash flow.
Once the decision to invest has been made, is it best to opt for the latest top-level technology or upgrade existing production plant? The former would be the ideal, as it offers not only the most productive and accurate machine tool technology but also invaluable support from the manufacturer and accessories suppliers. Although it requires higher initial investment, it can often lead to a quicker ROI.
For a lower investment, upgrading existing machines can be achieved to suit particular applications and industry sectors, using equipment and accessories readily available on the market. Among the most useful items are those that provide automated and improved workholding, additional CNC axes for deploying the cutting tool more efficiently, and additional production capacity through extended periods of autonomous running.
For more information on Don’t wait to automate talk to 1st Machine Tool Accessories
Enquire Now
List your company on FindTheNeedle.