
Sign In
Iemca Bar Feeders
12-09-2013
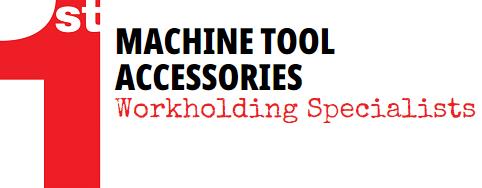
When people think of automation in manufacturing, high-end solutions like 6-axis robotic workpiece loading or multi-pallet flexible manufacturing systems often spring to mind first. Yet the most prevalent items of automation equipment, in the metalcutting sector at least, are bar magazines that feed turning machines.
A leading producer of such stock feeders is the Italian firm, Iemca, represented in the UK by sole agent, 1st Machine Tool Accessories. It has supplied magazines fitted to two dozen of the CNC lathes operated by South Coast turned parts subcontractor, Precision Products (Brighton) Ltd.
Fifteen of these turning centres are Citizen sliding-headstock models, while five of the remainder are fixed-head Miyano lathes, now also supplied through Citizen Machinery UK. Seven types of Iemca feeder in various bar diameter variants are used, including the manufacturer's Boss, KID, Genius, Elite and Smart models, plus an older CH112.
From a user's point of view, there are few people with more practical knowledge of these bar feeders than Brian Owen, managing director of Precision Products. It is noteworthy that his company only produces mill-turned components from bar stock, to the exclusion of chucking and prismatic machining. In this article, he advises on the importance of carefully matching each bar magazine to its intended CNC lathe.
He commented, "You first need to decide in which lengths you want to buy your round and hexagonal bar, whether ferrous, non-ferrous or plastic, in order to maximise turned parts output and minimise bar wastage. "We choose bar length according to its diameter. For our purposes, all stock over 32 mm for use on fixed-head lathes is delivered in one-metre lengths and fed from Iemca KID 80 short bar loaders.
"This length of bar, which can be up to 51 mm in diameter for our largest Miyano turning centre, is housed almost entirely within the headstock, so any tendency for the bar to whip is eliminated. It follows that the speed potential and dynamics of the lathe can be fully realised.
"A short loader takes up only about half the area on the shop floor that a full length model occupies, so a lot of extra space is freed up, allowing us to fit in extra lathes.
"Another advantage of short bar feeders is that there is no gripper, so each remnant is very small. It is pushed easily out of the front and ejected, avoiding the delay of extracting the remnant from the back of a full length magazine and so maximising spindle up-time."
As regards sub-32 mm material fed into the sliding-head lathes, Mr Owen uses longer magazines. Between 20 and 32 mm, 3.7-metre bar in an Iemca Boss feeder is the system of choice, as it allows long periods of unattended running. At the same time, material loss is limited, as the average remnant as a percentage of bar length is lower than if 3-metre bar were to be used.
In Boss magazines, which Mr Owen said are robustly built, the clamps self-centre directly on the bar, so no adjustment by the operator is required when changing bar size. The latest, patented guide channel is fully closed during machining cycles, can be rapidly replaced and is interchangeable with previous guides.
Three-metre stock is reserved for diameters in the range 12 to 20 mm, fed from an Iemca Genius 118, for example. With this magazine, as with all Iemca models, a double bar pusher reduces overall length of the magazine, saving valuable factory space. Although average rest pieces are longer as a percentage of bar length with 3-metre stock than for 3.7-metre bar, smaller diameters mitigate the amount of material loss.
For feeding bar less than 12 mm in diameter, Mr Owen prefers a magazine like the Iemca Elite 220. This novel magazine for sliding-head mill-turning applications, which is fitted to a Citizen K16E at Precision Products, has the ability to be swapped quickly from gravity feed of larger bar to walking-beam advancement of small stock down to 2 mm diameter. Material at the lower end of this range is regularly turned.
The unit features a redesigned bar pusher with dual bearings to complement high performance Swiss-type machines with rapid accelerations and rotational speeds up to 20,000 rpm, more than sufficient for the Citizen K16E's 15,000 rpm spindle. Another advantage of the magazine is that job set-up values can be stored in a library in the control to be reused for quick changeover when running repeat jobs.
In general, Mr Owen thinks that handling large and small diameter bars is most difficult and requires investment in the best bar feeders. Stock of medium size is handled satisfactorily by budget magazines such as the Iemca Smart 320s feeding four of his Citizen A20s, two with a guide bush and two configured without it. The magazine features snap-in guide channels for rapid re-tooling and a self-centring bushing built into the front that guides the bar when it is turning.
The non-guide-bush sliders are ideal for machining shorter parts, generate less material wastage as a result of shorter remnants, and tolerate the use of less accurately produced bar. At Precision Products, the lathes are frequently employed for round-the-clock production of spacers to a high degree of flatness and parallelism for the aerospace industry.
The sector accounts for around 10 per cent of turnover currently, but following the subcontractor's success in gaining AS9100 quality management accreditation in September 2013, that proportion is likely to grow quickly. Other industries served include automotive, medical, brewing, white goods, fluid power, defence and telecoms.
Reshoring accelerates
Precision Products, which employs 40 people and operates two machine shops at its headquarters in Rustington, near Littlehampton and in Hollingbury, Brighton, has seen reshoring of work to the UK from Asia and Eastern Europe accelerate in recent years.
Mr Owen continued, "The overseas price advantage of around 80 per cent a decade ago was been whittled away to nearer 30 per cent today, which together with the benefits to customers of local sourcing gives us – and the whole of British manufacturing – a real opportunity to expand.
"However, we have to be highly responsive to what the customer wants. More and more we are being asked not just to machine components but also to produce sub-assemblies, often supplied in specialised packaging for kanban delivery.
"We also have to make sure we are highly productive and cost effective, which means buying only the best, automated CNC turning equipment. We believe this to be a combination of Citizen and Miyano lathes, both from Citizen Machinery UK, and Iemca bar feeders supplied through 1st MTA.
"Having single sources of supply and service helps us considerably. Our operators find it much easier to set up similar machines and bar feeds, appreciate the interchangeability of tooling and bar grippers, and like the commonality of programming. It means we can set up jobs quickly and swap them between machines as necessary."
Origins
An early member of the British Turned Parts Manufacturers Association, Precision Products was started in 1974 by both Brian Owen and his father, Bryn, with a selection of cam automatics. Today, the company still operates four Wickman multis and six Escomatics at its Hollingbury site and produces over one million parts weekly.
More than 80 per cent of plant is now CNC, however, producing batches of mill-turned parts down to 100-off at economical prices, due to the fast set-up of modern lathes and bar feeds and the high accelerations, speeds and feeds of which they are capable.
The subcontractor bought its first CNC lathe back in 1983 under the UK Government's SEFIS grant scheme. It was not until the late 80s that the first Citizen / Iemca CNC bar auto was installed, a second-hand B12 sliding-head lathe fitted with a CH112 bar feeder for turning parts in the diameter range 12 mm down to 1 mm.
Even though it was a used machine, Citizen Machinery UK agreed to install it as though it were a new purchase, complete with service back-up and training. This early relationship was instrumental in Precision Products staying with this supplier of automated CNC turning plant.
Conclusion
Commenting on the performance of the Iemca equipment in use at both of his sites, Mr Owen offered, "There is such a wide range of these Italian-built bar feeds available that we can always find one that exactly fits our needs. If we need help for any reason, a 1st MTA engineer is always on site quickly.
"The magazines are quick to set up and reliable in operation, with minimal noise and vibration, even when using hexagonal stock, which we do about 10 per cent of the time.
Geoff Bryant, managing director of Citizen Machinery UK added, "For our machines, we recommend Iemca as the bar feeders of choice due to their good price and performance, operator-friendliness and the high level of after-sales support from the manufacturer.
"They also keep up to date with the latest bar feeding technology. A case in point is the Iemca Elite, which is two magazines in one unit, interchangeable within seconds by the user to allow reliable feeding of bar from 20 mm right down to 1 mm diameter."
For more information on Iemca Bar Feeders talk to 1st Machine Tool Accessories
Enquire Now
List your company on FindTheNeedle.