
Sign In
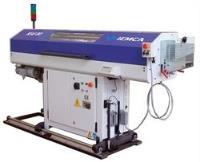
Turning productivity raised by 30% and labour costs cut
One of the top two hydraulic adaptor manufacturers in the UK, Gemac Hydraulics in Stanwell Moor, near London Heathrow Airport, has standardised on IEMCA short bar magazines for feeding hexagonal (hex) mild steel stock into its turning machines. The Italian-built, all-electric bar feeders, of which two have been delivered, were supplied by UK agent, 1st Machine Tool Accessories.
A major benefit of using IEMCA equipment, according to Gemac’s owner and managing director, Salvatore Costanza, is that alignment of hex bar with a lathe’s chuck jaws takes a shorter time than with alternative magazines, so bar change is faster and the lathe resumes production sooner.
He said that the magazines are quieter in operation, as there is less vibration compared with other bar feeders, leading to better machining accuracy and extended tool life. The short bar magazines are also very compact, which is important to Gemac as space is limited in the factory.
Manufacture of fundamentally rotational products that will subsequently be tightened with a spanner requires at least one hexagonal feature. In some cases, hex flats can be milled using driven tool stations in a lathe with live tooling, but this would be impractical when producing a hydraulic coupling, as almost the entire component is hexagonal in cross section.
Gemac’s second-generation machine shop manager, Giuseppe Costanza, commented, “We have no option but to use hex bar, but previously when we installed another make of feeder, we often found it difficult to line up the stock with the back of the spindle. This introduced excessive idle time and reduced productivity.
“The IEMCAs, on the other hand, have a servo-motor controlled pulse-push function that allows rapid alignment and feed-through.
“After setting the bar size on the bar size selector, the guide channel automatically aligns the centre of the stock with the centre of the spindle. During this time, the spindle is programmed to rotate at 40 to 50 rpm, which gives the bar a chance to line up properly.
“In this respect, the IEMCAs are easily the best bar magazines we have used. They reliably and consistently feed hex bar, as well as the small amount of round bar we use, so the lathe can be left to continue running unattended.
“With some other types of magazine, an operator has to be present at every bar change in case production stops due to a misfeed.”
One of the IEMCA magazines, a KID 80, was installed in 2011 as part of an Eagle 100 CNC turning cell supplied by Dugard, who had recommended this make of bar feed to Gemac. The other magazine, a VIP 70 CNC, was retrofitted in 2011 by 1st MTA to a Dugard Eagle 200 HT lathe that had been supplied the previous year without a bar feeder.
Salvatore Costanza advised that productivity from this lathe has been increased by 30 per cent compared with when they were previously using the machine as a chucker or feeding short lengths of bar through the spindle by hand. In addition, continuous operator attendance is no longer necessary, reducing labour costs.
The VIP 70 is extremely compact to suit the space constraints on the shop floor and handles a maximum bar length of 1.5 metres, although one-metre stock is used as standard, mainly 50 and 55 mm hex. Bar of 32, 38 and 41 mm is put mainly through the KID 80, which is capable of feeding 1.6-metre lengths. However, with spindle speeds of around 3,000 rpm, which is relatively high for hex bar, and with minimisation of vibration a priority, lengths are restricted to one metre in this magazine as well.
Depending on size, typically 10 to 14 bars can reside in each magazine, enough for six to eight hours’ production of hydraulic fittings, according to their length and complexity.
Operation of three Wickman multi-spindle cam auto’s and two Witzig & Frank rotary transfer machines help to boost overall production at Gemac to 10,000 components per day, half of which are exported. Some 1,500 product lines in a variety of sizes and materials are stocked. The Stanwell Moor factory also produces and stocks hoseassemblies for UK customers.
Salvatore Costanza, who has more than 44 years’ experience in the manufacture of hydraulic fittings, said, “A lot of this production went to Eastern Europe during the last decade, when sterling was high against the euro, but now the UK is more competitive and manufacture of this type of work is coming back.
“I was aware of IEMCA bar feeders from a previous company, where one was fitted to an Italian-built Gildemeister lathe. I was impressed with the robustness of the magazine as well as its reliability, ease of setting and the consistency with which it fed the bar.
“Since starting Gemac a few years ago, I have also been impressed with the service from 1st MTA. One of their engineers was on site a few weeks ago at 7am, when our factory opens, to correct a bar misalignment issue after a member of staff here had moved a machine instead of calling in the supplier to do it.
“All of the 1st MTA people seem very approachable and knowledgeable and their technical manager even took trouble to visit us after the first magazine was installed just to check that everything was OK.”
The full range of Iemca Bar Feeders are availalbe from 1st MTA.
For more information on Iemca Bar Feeders at Gemac Hydraulics Raise Productivity By 30% talk to 1st Machine Tool Accessories
Enquire Now
List your company on FindTheNeedle.