
Sign In
Mach 2012 Preview Information
14-03-2016
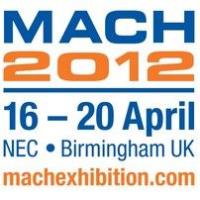
ST MTA TO HIGHLIGHT PRODUCTIVITY ENHANCEMENT OPPORTUNITIES
Workholding, drill sharpening and automation equipment specialist, 1st Machine Tool Accessories (1st MTA), will show its extensive range of products for raising production output and maximising return on investment from machine tools. As a special promotion at this year’s MACH exhibition, visitors to the stand will receive discount vouchers for purchases of US-manufactured Chick vices and Darex drill sharpeners.
Fast-acting workholding
Providing the speed, precision and flexibility demanded by modern CNC machining operations, Chick’s One-Lok clamping system eliminates the shortcomings of standard knee mill vices, as will be shown on the stand.
Unlike traditional machining vices, which require up to 70 complete revolutions of their operating handle to be fully opened or closed, One-Lok features a ‘QwikSlide’ mechanism that allows the moveable jaw to be easily unlocked and slid forwards or backwards to achieve rapid set-ups.
Its maximum grip capacity of 17 in (432 mm) is complemented by the manufacturer's ‘Boltfast’ jaw system, which enables jaws to be replaced quickly and efficiently with a repeatability of 0.0008 in (0.02 mm).
The system’s compact, modular design also features innovative ‘squeeze’ clamping, which imparts a pull down action and virtually deflection-free clamping with a maximum retaining force of 4.5 tonnes.
4-axis CNC sharpener restores drill bits inexpensively
The Darex 4-axis CNC drill sharpener, XPS-16, will be demonstrated restoring high-performance drills in a simple, one-touch operation. The bench top unit costs the equivalent of 100 radial split point carbide drills, yet even unskilled operators can sharpen more than 400 of them in a day. Return on investment is typically under eight months.
Conical, four facet, split point and radius split point twist drills with angles from 90 to 150 degrees can be processed, including high speed steel, cobalt, solid carbide and coated tools from 51 to 254 mm (2 to 10 inches) long and 3 to 16 mm (1/8 to 5/8 inch) diameter.
A blunt drill is inserted into the mains-powered sharpener’s chuck and the required standard or custom type of drill point is selected using a simple LCD touch screen panel. The unit then sharpens the drill and applies the required split point form in one seamless operation, without operator involvement.
The sharpener incorporates long-lasting superabrasive plated grinding wheels, 180 grit cubic boron nitride for HSS drills and 220 grit diamond for carbide tools.
New vices are ideal for 5-axis machining
The range of workholding products offered by 1st MTA has been significantly expanded since the last MACH exhibition, following a new agency agreement with BEST GmbH, Filderstadt, Germany. The company is a leading manufacturer of low-profile, centric (self-centring) vices that are particularly suited to clamping components undergoing multi-axis metalcutting applications on machining centres.
There are similar products on the market, but 1st MTA asserts that the BEST BSM range of manually operated, centric vices combines top quality and high clamping forces up to 100 kN with very competitive prices. Other notable qualities of the vices are an ability to clamp on only 3 mm of material; and ± 0.01 mm centring accuracy with five microns repeatability of centricity for manual and pneumatic vices, and one micron repeatability for hydraulic types.
Vices range in length from 115 mm to 500 mm and have up to 50 mm stroke. Face plates and adapters allow them to be fitted to any machine table, pallet or rotary table. Depending on requirements, they can be screwed conventionally to the table or used as a zero-point vice on the BEST Realpoint quick-change system (or other manufacturers' zero-point clamping systems after simple adaptation).
Jaw varieties including knife-edge options are manufactured from a range of materials from aluminium through machinable steel to hardened and ground steel to suit the application. Quick-change jaws are an option to the traditional tongue and groove for all vices with a suitable connection.
1st MTA’s comprehensive range of workholding solutions will be complemented by a display of Tecnomors self-centring automation grippers, indexing chucks and 5th axis manual vices. In addition, the company will demonstrate numerous examples from its established and proven machining and workholding products ranges, including Abbott and Leave fixturing and clamping products; OK-Vises; Brighetti reduction bushes; CoolJet high pressure coolant systems; Micromag filtration units; and Overbeck deburring twister lathes.
Wide range of Kitagawa chucks
High clamping torques, extreme rigidity and fast operation are key features of Kitagawa’s GT series of heavy duty rotary tables. Available in three models with tables from 200 to 320 mm diameter, the units incorporate a novel piston design that delivers component clamping torques of up to 2,800 Nm. Productivity is further enhanced by the tables’ rigid yet compact design, which allows maximum metal removal rates to be combined with high indexing accuracy and repeatability. The GT series also features a rapid clamping action for reduced cycle times and maximum production throughput.
The NV chuck range from Kitagawa has been developed to meet the demand for large power chucks in vertical lathes. Produced in eight models for components from 62 to 1,000 mm diameter, NV series units feature a protective jaw cover and scraper system that prevents the ingress of swarf or coolant into the chuck mechanism. They are rated for maximum speeds up to 2,900 rpm and are designed for use with standard range Kitagawa jaws and Y2035R type cylinders.
Kitagawa’s latest QJR08, QJR10 and QJR12 quick change chucks are interchangeable with the company’s popular large through-hole B208 / B210 / B212 and BB208 / BB210 / BB212 models. The new units’ base jaws, which are rapidly and simply changed using a manually operated wrench, feature metric serrations to accommodate a wide variety of popular jaw types.
DHP and DHF collet chucks from Kitagawa provide secure and accurate clamping of components up to 65 mm diameter. DHP variants generate a powerful pull back action for first operation work, while DHF models feature a removable bore stop, fixed collet position and high accuracy to ensure precise second operation machining. The compact chucks are offered with standard A5, A6 and A8 mounts to suit popular machine tool types and have been designed to be both compatible and quickly interchangeable with other popular quick change collet clamping heads, without the need for special purpose adaptors.
Bar feeding and billet loading
Representing the Italian-built Iemca range of shop floor automation equipment will be the KID 80 automatic bar magazine. Featuring outstanding versatility of application, the feeder is suitable for single-spindle lathes, either fixed- or sliding-headstock, CNC or cam-type. It can accommodate bar diameters from 5 to 80 mm and lengths up to 1,615 mm. The KID 80 can also handle bar pieces by inserting them into the spindle.
The ideal application for the compact feeder is in a production environment producing small to medium sized batch quantities with frequent work setups. Changeover from one bar diameter to another is performed rapidly and easily. The system is entirely mechanical, assuring reliable performance and efficiency. No compressed air connections are required.
New gantry handling systems for automated billet loading and workpiece handling have been introduced by Iemca since the last MACH show. An Automata Palletiser will not be on the stand, but will be actively promoted. It is a generic retrofit package that can automate machine tools already in use on a shop floor. Alternatively, it can be fitted to a new machine tool before delivery.
The overhead gantry is freestanding and not mechanically linked to the machine tool it services, so the unit is quick to install or transfer between machines, if desired. Transmission of unwanted vibrations that could compromise machining accuracy is avoided. An advantage of the loading arm travelling over the top of the machine tool is that the design allows full access through the machine's doors for tool change.
There is a 2-axis PLC stacker version of the Automata with a horizontal carousel for holding billets and machined components. Additionally, a 4-axis palletiser version incorporates a wheeled trolley, comprising up to nine trays, housed within the gantry’s superstructure. While the machine tool is being fed automatically from one trolley, an operator removes finished parts from and replenishes billets to another trolley outside the system, allowing almost continuous production.
For more information on Mach 2012 Preview Information talk to 1st Machine Tool Accessories
Enquire Now
List your company on FindTheNeedle.