
Sign In
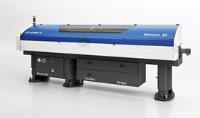
The world’s leading manufacturer of magazines for automatically feeding bar into CNC lathes, the Italian company Iemca, has introduced a new bar feeder designed to maximise productivity during unattended turning and mill-turning of larger diameter components in single-spindle, fixed-head lathes. Called Maestro 80, the long bar feeder is available in the UK and Ireland through sole agent 1st Machine Tool Accessories, Salisbury.
With over 100,000 bar magazine installations worldwide, a quarter of which are for material over 65 mm diameter, Iemca has over 45 years’ experience of feeding large diameter bar. Among the innovative design features incorporated into the new magazine, three have been granted patents.
One protects ABACOS (Adaptive BAr COntrol System), a self-adjusting bar clamping arrangement. It is designed to carry out different operations, namely guiding the material, damping vibrations and tightening on the pusher, all without changing the guide channel over a material range of 10 mm to 80 mm diameter.
The ABACOS system can also handle non-round material – 10 mm to 65 mm hexagonal or 10 mm to 50 mm square – with a quick change of the bushes. Material length options are from 1,000 mm up to 3,200 mm, 3,700 mm or 4,200 mm, subject to a maximum single bar weight of 180 kg.
The widest spread of bar diameters that could previously be guided in one channel was 20 mm to 80 mm, an attribute of the Iemca Master 80 HF magazine. A limitation of that model is that when feeding smaller diameter bar, especially when it is not straight or of poor quality, it is necessary to reduce the rotational speed. Otherwise vibration can occur, compromising surface finish and/or dimensional accuracy of the component being produced.
On the Maestro 80, this is avoided by another patented feature, the VIBRA-DAMP COLLET with interchangeable inserts. It damps bar vibration by reducing its oscillation amplitude and lowers bending and torsional stresses on the bar.
A third patient has been granted to Iemca for its HANDYLOQ quick change collet system, which allows manual exchange within three seconds without the need to use tools.
This, together with the ability to turn bar all the way from 80 mm down to 10 mm in diameter at the lathe’s maximum spindle speed, without having to stop the machine to adapt the guide channel by introducing inserts, results in bar changeover within 30 seconds and hence high spindle uptime. Return on investment is therefore fast, both in the bar feeder and the machine tool.
Another notable benefit is that due to ABACOS and a reduction in bar pusher length, it has been possible to remove the front bushing so that the magazine can be positioned closer to the lathe. It has the effect of limiting vibration further and also reducing spindle inertia, extending its life by lowering the load.
Additional advantages of the ergonomic Maestro 80 are Industry 4.0 data sharing as an option, built-in boxes at the front to facilitate access to the electrics, lubrication system and tools, a drawer for remnants, efficient cable management and a modern touch-screen control with 7 inch operator interface that includes the ability to adjust the magazine automatically for a new bar size. Additional bar loading systems to allow extended periods of unmanned running are expected during 2019.
For more information on New bar feeder for more efficient production of larger turned parts talk to 1st Machine Tool Accessories
Enquire Now
List your company on FindTheNeedle.