
Sign In
Paul Swann from Chick Workholding
23-08-2011
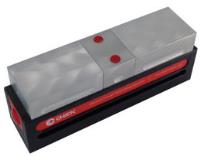
PAUL SWANN, owner and managing director of Chick Workholding Solutions, explains how an innovative approach to clamping can raise productivity and accuracy, sometimes dramatically. Sole UK agent for the US-made products is 1st Machine Tool Accessories, Salisbury.
Machinists tend to be highly talented people, but rather conservative when it comes to exploiting workholding technology to the full. Yet beyond the comfort zone of traditional clamping practices lies the difference between advanced manufacturing and world class manufacturing, says Mr Swann.
Operator safety is paramount and next most important is the quality of the components being machined, both priorities requiring rigid, consistent workholding. Most staff in a factory, from the production director to the machine setter/operator, are content if those conditions are met.
However, this should be just the starting point, Mr Swann suggests. He outlines below various clamping techniques that maximise metal removal rate, increase accuracy and minimise idle times, leading to extra efficiency and profit.
Two core considerations are these. First, if clamping is firmer and more secure, larger cutters can be used, leading to heavier cuts and higher productivity. Second, rapid operation of workholding systems like the Chick One-Lok, with its fast ratcheting of the moveable jaw to within millimetres of the point of closure before a handle completes the clamping action, increases output further by minimising idle time.
The experience of Chick’s applications engineers in the US is that the output of a vertical machining centre can be increased by typically 30 per cent, and exceptionally by up to three times, with judicious production planning and use of modern workholding technology.
1st Machine Tool Accessories, the UK agent for Chick, can identify numerous instances where its principal’s products have increased productivity in British factories. Specialist engineers are available to carry out site visits, advise on the most appropriate clamping methods and demonstrate their performance in actual applications.
Pads increase clamping consistency
The forces pressing on either side of a clamped component are not uniform across the surfaces in contact with the jaws, but are concentrated at one high spot on the fixed side and two similar points on the floating, moveable jaw. The positions of these points are unknown.
Therefore the localised clamping forces on the workpiece may be anywhere over the faces of the ‘smooth’ jaws and are unlikely to be equal and opposite, which is the ideal. So it is recommended that rubber or plastic pads are fixed to both jaws at either side of the component to restrict the contact points to known areas.
The precise locations of the contact points will still be uncertain, but it does not matter, as they must fall within the areas of the pads and so the fundamental geometry of the clamping action is optimised for maximum stability. One alternative is to employ jaws with a roughened surface, which increases the number of points in contact with the workpiece, but there is a risk of causing unwanted marking.
It is a good idea to use similar pads on the working surface of a vice to act as rests. Provided that they are swarf-free, the precise vertical position of a part sitting on them is known, even though swarf may have collected below the level of their top surface. As batch size rises, speed of load and unload become more important, so swarf that prevents quick and accurate location of a part prior to clamping is unhelpful. It is also possible to use lateral rest pads for added stability, but on one side only to prevent over-constraining the workpiece.
Pads have the additional effects of protecting the workpiece surface and of dampening vibrations during machining, enhancing accuracy and prolonging tool life.
A burr along the edges of a premachined component is another factor that may prevent it from sitting down squarely on the working surface, resulting in misalignment. To prevent such uncertainly, a relief can be machined at the bottom of a jaw to accommodate the burrs.
Multiple workpiece clamping
Significant improvements in productivity can result from clamping more than one part in a vice. For example, machining a single component might require a 6-minute cycle but due to human factors it slips to 7 minutes. If two parts are fixtured the waste is halved, as the one-minute loss is spread over twice the number of components. It is halved again if four parts are fixtured and the benefit increases logarithmically.
So also does operator walk-away time, allowing extra tasks to be performed during the machining cycle, such as tending other machine tools or carrying out second operations. Unattended operation on a vertical machining centre suitably equipped with modern clamps can last for up to 90 minutes. It allows production to continue over operator breaks or well into the evening after the factory has closed for the day. Research has shown that faster set-ups, multiple component loading and unattended running can double an operator’s productivity.
The shorter the cycle time per part, the more important multiple fixturing becomes. It is not recommended that more than two components are clamped in a single jaw set, however, as if three are held, one invariably slips. Dedicated twin-station clamping systems like Chick Qwik-Loks are the best solution for machining pairs of parts and up to five can be fixed to a standard machine table.
If a twin pallet machining centre is being used and the APC time is slow, it may be expedient to fixture several dozens of components, if batch and component sizes allow, to minimise the effect of the long pallet change on production cost per part. The only downside of multiple part fixturing is that if a tool breaks and it is not detected during unattended operation, there is scope for generating a lot of scrap, although tool monitoring systems avoid the problem.
High density, dedicated fixturing is available using Chick’s versatile, quick-change faceplates, which can be machined to suit specific applications. Essentially a fast and highly repeatable mini pallet changer, the system reduces set-up time considerably when machining multiple small or awkwardly shaped workpieces that are difficult to clamp.
Chick also manufactures bespoke, precision ground, cast iron foundation plates, each of which bolts to a specific machine table, covering the T slots.
The plate has a grid of holes spaced 50 mm apart, each hole having an M12 thread at the bottom for bolt down and a 12 mm diameter bush at the top for accurate location. The system allows fixtures to be mounted quickly and consistently in the same location, reducing set up time. All foundation plates incorporate an alpha-numeric labelling system to simplify production and cataloguing.
Two-hit machining strategies
In the past, machining six sides of a cuboid part required six separate clampings. However, using modern workholding methods and with the ready availability of 4th and 5th CNC axes on machining centres for indexing more complex components, just two hits are normally needed. The part can be machined from above and two sides in the first clamping, then inverted and rotated through 90 degrees for completion.
Such a strategy is widely used, but care needs to be taken when multiple parts are clamped. Should Op 10 and Op 20 be performed at each pair of stations so that a finished part comes out every time the machine doors are opened? Or is it best to perform the same operations on both components at the same time?
Mr Swann’s opinion is that it comes down to how many tool changes are required. If there are many and the two operations require a significant number of different cutters, it makes sense to set up for two Op 10s then two Op 20s, as otherwise excessive idle time is generated during ATC and the associated rapid traverses.
On machines employing indexing units, an important consideration is whether to change tool or index first. If tool change time is shorter than indexing time, the machine should cycle through all of the cutters on one side of a component before indexing.
If indexing time is less than tool change time, a cutter should be retained in the spindle and the components repositioning. Under such conditions, all parts are cut prior to changing the tool. Using multiple indexing units, one or more can be programmed to index while another is in cut, saving further time.
Another consideration in determining the most effective workholding solution, particularly for small components, is the desirability of nesting components as closely together as possible to minimise the amount of rapid tool travel time between each part.
All of the above analyses are employed at Chick’s own factory in Pennsylvania, allowing the company to compete effectively with vice manufacturers in low-wage countries.
Clamping force
A component must be held securely, but the clamping system should not be over tightened and never with a cheater pipe. If a part does not stay fixed during machining, something is wrong with the setup. A workholding solution should have a pull-down effect as it is closed and almost no jaw deflection, which are a consequence of the manufacturer’s designs. Moments of force need to be considered and the component mounted as low as possible in the jaws, consistent with providing access for the tools.
Soft jaws can be machined to hold a part more securely if it is awkwardly shaped. Attention to providing adequate space for chips to collect pays dividends, as does machining of suitable pockets for coolant to enter and blast chips away from the machining area. If a hard serrated jaw is used, it should be placed on the fixed side only, as a serrated moveable jaw can cause the part to be clamped incorrectly. A quick-change jaw system is essential to minimise set-up times as well as to utilise other jaw sets that may exist in a factory.
Drawing tolerances are decreasing all the time, with 12.5 microns frequently encountered in a general machine shop, whereas a few years ago it would have been 25 microns. It is another reason to avoid excessive tightening, as part deformation can easily result, especially when machining softer materials, using up a lot of the allowed tolerance, or even exceeding it.
Tooling considerations
It is universally recognised that sharp tools promote high productivity and component accuracy. They also assist the stability of clamping by minimising cutting forces, which is especially important when machining from the side. However, in general, insufficient attention is paid to drilling operations, according to Mr Swann.
He points out that a drill has zero cutting effect at the centre, so getting a large diameter bit to penetrate a workpiece, especially when machining harder materials, requires a lot of pressure that can cause movement in a vice. He therefore recommends machining a pilot hole before coming in with the full diameter drill. A small amount of time is lost due to the extra operation and tool change, but it is often outweighed by the advantage of more secure clamping and more accurate drilling.
A further advantage of precise, repeatable clamping is that for all but the most exacting applications, it can eliminate the need for probing to verify part position before machining commences. Not only is the cost of the probing system saved, but also the time that otherwise has to be added to the start of the cycle.
A piece of history
The foundation of Chick Workholding Solutions had unlikely beginnings. Paul Swann’s English parents, Barbara and Rex, followed the hippie trail to the States in the early 1960s. Rex used his background as a machinist and designer to set up a job shop in 1965, buying a manual milling machine to make a very high precision part for his first customer.
As the business grew, he could see that set-up times were holding the company back and reducing profitability. He took the unusual step of investing on spec in a Matsuura horizontal machining centre with 11-pallet pool, an expensive purchase, to take advantage of off-line fixturing.
This threw the spotlight on the efficiency, or lack of it, with which parts could be clamped using rudimentary vices taken from an old Bridgeport turret mill. The Matsuura was highly productive once parts were fixtured, but it used to take a long time using conventional vices and the operator was chained to the machine.
Having researched the workholding market and found no product that fitted his needs well enough, Rex decided to develop his own quick-change clamping systems to speed set-up and free the operator to do other tasks. It was the start of Chick Workholding Solutions, which now specialises in the manufacture of generic clamping systems and machine tool-specific OEM workholding products. Both Rex and Barbara are still involved in the business today.
The full range of Chick Workholding products are available from 1st MTA.
For more information on Paul Swann from Chick Workholding talk to 1st Machine Tool Accessories
Enquire Now
List your company on FindTheNeedle.