
Sign In
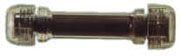
Service Repair of Viscous dampers.
The METALDYNE viscous damper has a design / operating principle of using a high viscosity silicone fluid to generate damping torque by shearing the thin film of fluid surrounding the inertia ring mass (flywheel).
As the engine speed changes to a point where torsional vibration is present, the crankshaft (and hence the damper casing because of its attachment to the crankshaft) are subject to torsional oscillation superimposed on the mean rotation. Because of its inertia, the flywheel (within the casing) will continue to rotate at a more uniform velocity so that there is an oscillating relative movement between the flywheel and casing.
Therefore, when torsional vibration is present, the fluid undergoes a shearing action absorbing vibration energy which is dissipated as heat.
The high viscosity silicone fluid within the damper casing will, after constant heat absorption during its service life, reduce in viscosity value and because of this, sampling plugs are fitted into the cover plate and / or back face of the casing so that samples of fluid can be extracted for analysis to determine the condition of the damper.
From this fluid analysis, the internal mechanical condition and operating efficiency of the damper can be established, and METALDYNE will recommend the service period the damper can be used before a further sample of fluid must be taken. If the reduction in fluid viscosity is excessive, or the condition of the fluid indicates internal mechanical damage, the remaining safe service period before overhaul of the damper becomes absolutely necessary will be advised.
New silicone fluid is a clear / colourless fluid and as a general guide, the following observations when sampling may be of assistance.
1) Fluid colourless to light shades of yellow / brown, and free from particles. Usually indicates no internal damage. Fluid viscosity will determine suitability of damper for further service periods.
2) Fluid dark brown or black in colour, usually with particles in the fluid. As a general rule, dampers with fluid in this condition have suffered internal mechanical damage and have restricted remaining service life.
3) Dampers with gelled / solidified fluid are unsuitable for service and they should be removed from service at the first convenient opportunity.
The service life of the damper can only be accurately established by fluid analysis, and torsional testing of the engine will only indicate the condition of the damper at the actual time of testing.
Provided no internal damage has occurred, overhaul is recommended when the fluid has reduced 50% in viscosity value. At this stage, the damping efficiency will be 80%.
The average operating time to reach this condition is 25,000 / 30,000 hours, but it can be influenced by engine application and loading as well as non-torsional factors associated with then engine?s environment such as vibrations induced from adjacent machinery, engine mountings, shafting systems and hull vibrations.
It is therefore recommended that the first fluid sample is extracted not later than 15,000 service hours.
Examination of the first sample will enable METALDYNE to advise the subsequent sampling intervals, and by following this procedure and our recommendations, the necessity for overhauling or replacing the damper can be anticipated.
For more information on Crankshaft Damper Repair talk to AAM Driveline Halifax
Enquire Now
List your company on FindTheNeedle.