
Sign In
Magic Carpet fix
03-03-2017
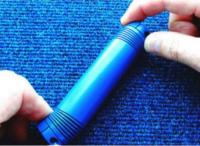
Another shaft coupling connection challenge was successfully solved by the Helical flexible beam product available through Abssac Limited. Abssac's customer had an application where a precision encoder was being connected to a carpet manufacturing machine output shaft. The machines are used to manufacture man-made fibre twisted loop pile carpets for domestic use. If the vibration and movement present at the output shaft was transmitted to the encoder, it would cause signal errors and ultimately prematurely destroy the encoder. Ultimately this would lead to below standard carpet being produced due to loom operational irregularities. Whilst very little torque was required in the application, torsional stiffness and zero backlash were important design parameters.
The customer also wanted a low maintenance solution. From a shaft coupling design aspect, the application required large axial motion and parallel misalignment because of the assembly tolerances. The customer was originally using a multi-part bellows shaft coupling, but the required angular and axial movements had lead to premature failure. Additionally, under certain operating conditions, the bellows coupling allowed too much vibration to reach the encoder.
When looking at Flexible Solutions - Flexible Couplings - Flexured U-Joints, one of the greatest advantages of the Helical Shaft coupling product is the ease in which it can be adapted from a standard and into a cost effective, multi-functional bespoke design. It is the perfect solution where flexibility is required for critical applications.
By altering the characteristics of coiled beam area, torque capacity, angular and parallel misalignment capabilities, (torsional and lateral bending rates of flexured u-joints) can be modified to suit specific specifications and or requirements.Once the performance dynamics of the coupling are decided, we then look at the way the shaft coupling attaches in the application or perhaps how we can add other parts of the total mechanism into the single piece shaft coupling. We like to refer to the adaptable flexible element in the product as the "FLEXURE".
The flexure is determined by six major characteristics:
1. Flexure outside diameter
2. Flexure inside diameter
3. Coil thickness
4. Material
5. Number of coils
6. Number of coil starts
Changing the beam characteristics offers huge advantages to a driven system
By varying the thickness of the coils a flexure can accommodate increasing amounts of torque and radial loads.
By varying the Number of Coils the torque capability remains unchanged but the angular, parallel and skewed offset capability increases.
By varying the Inside Diameter so does the torque capacity, torsional stiffness and axial spring rate
By varying the Number of Coil starts with One, two or three helical beams provide higher torsional stiffness.
In a rotating system, constant velocity refers to the relative rotational speed of the input and output shafts. In a constant velocity system the driven end of the coupling turns exactly the same rate as the driver end. When operating under a uniform load the helical flexure design provides constant velocity and can alleviate problems such as Backlash. The helical flexure has zero backlash. Angular misalignment can induce large fluctuations in rotational velocity in certain coupling designs.The Helical flexure has a constant spring rate at all points of rotation. Torsional variations can induce differences in hub to hub velocity when subjected to dynamic loading are minimal in steady state applications on the helical flexure. Concentricity can be an issue when there is a lack of it, particularly in the case of couplings with backlash or where production variation is difficult to prevent. The Helical flexure one piece integrity minimises sinusoidal variations and has zero backlash.
Misalignment Compensation
The flexing capacity of the flexure can compensate for a variety of misalignments including parallel, angular, axial and skewed shaft misalignment. Optimised Torque Capacity – The basic requirement of a flexible coupling is to transmit torque loads without permanent distortion or damage and without imposing undue bending or radial loads upon the driver or driven components. Once the working torque rating of the flexure coupling is established, based on design criteria, its operational life is virtually unlimited.
Configurable Torsional Stiffness
Every Flexible coupling has some torsional flexibility. Torsional flexibility reflects the amount of twist in a system; torsional stiffness the degree of resistance against twist. The flexure uniquely can be configured to provide the exact amount of torsional flexibility required in an application. The Helical flexure maintains a very constant radial and bending load at all points of rotation, providing exceptionally uniform and smooth bearing loads.
The Heli-Cal flexure product is available Aluminium, high strength alloys, Titanium, MP35N, Delrin to name a few and have been successfully used in medical, energy, military, aerospace and industrial automation.
By simply allowing the development of innovative connection solutions from the standard helical beam shaft coupling design, has opened up a plethora of opportunities to the design engineer. The hidden potential of expanding how a shaft coupling physically connects within an application, which is often left to standard grub screw or locking clamp, can enhance the overall efficiency of an application. With Abssac’s Heli-Cal beam coupling product, customers have been able to take their standard coupling designs to the next level, by incorporating features into the original shaft coupling design. In many cases, the final shaft coupling design is normally an amalgamation of separate parts that include such items as external gears, splines, threads and tangs. However, most importantly, it enables the design engineer to achieve far greater usage from one item in the total machine which inevitably leads to greater efficiency. How the standard shaft coupling connectability is enhanced, is really up to the designer. Abssac is so confident with the products success rate that in many cases it offers a free sample for the customer to test and evaluate. Stacey Taylor at Abssac says, “When you consider the Heli-Cal beam couplings capability as a shaft coupling and then add this ability to integrate the design engineers own end attachment ideas, you have a formidable product combination that other coupling manufacturers can not supply”.
Abssac recently enhanced the operation of a medical orthodontic machine by replacing a universal joint, plastic shaft coupling and a piece of shafting with just a one piece flexured drive shaft unit. Abssac's customer had initially been using a traditional universal joint to connect a hand control, via a piece of shaft and through another plastic flexible shaft coupling, to a small gear box. The universal joint was expensive and was being utilised at the limit of its angular capability, which was causing cyclic torque variants on operation. A separate piece of bar stock was then used to span the drive mechanism to the gear box, which again required 3 degree shaft misalignment, which was accommodated by a small plastic multipart shaft coupling. The old design was inefficient, time consuming to build and had suffered from reliability issues.Abssac's solution was to take 400mm of Aluminium bar stock, 15mm in diameter, which would provide the length requirement of the drive shaft. Then using the unique ability to adapt the "flexure" or beam part of the helical beam shaft coupling, they could provide the two angular misalignments required in the system, but all within the single part. Utilising a double start coil flexure at each end to give the superior torsional stiffness, the drive shaft could accept angular misalignment up to 30 degrees at one end, whilst the other end would accept up to 5 degrees. The final design incorporated a split clamp design to lock the drive shaft into position onto the driven and drive ends.The new design was then used in 4 other machines using different lengths as the single part provided a zeroblacklash drive solution, which did not require lubrication, maintenance or suffered from operational issues.
Abssac has recently supplied a classic example of the flexures unique capability being utilised as a heat sink. A pancake shaped compression flexure 50mm in diameter but only 5mm in height has been produced to hold an ultra thin reflective mirror on its top surface, in a high wattage industrial laser machining application. High strength aluminium material was used because of its heat transfer characteristics and low cost. By incorporating the unique flexible element into the one piece design allows the easy alteration of the mirrors angle of incidence, whilst maintaining the mirrors position, rigidity and focus.
Miniature designs are a growing part of our business as components become smaller and demand more function. A fully functional 3.1mm diameter shaft coupling was recently supplied for a medical application. Using a left and right handed thread shaft for attachment the coupling could accept up to 1mm of angular offset rotating up to 10,000 rpm. The same customer is now looking at a double start flexure with a 1.5mm outside diameter produced in titanium.
As the originators of the Helical beam style coupling we have a few decades of hard earnt knowledge on the competition. With any Helical beam flexible coupling design it is imperative that the start and finish of the coil slit is finished smoothly and without scarring or swarf residue, as this will shorten the working life of the shaft coupling dramatically. The way in which other similar designs are manufactured results in a relatively sharp edge that may act as a stress riser during operation. In certain cases this stress riser is where a crack will form and most likely lead to a complete failure of the part. Apart from superior manufacturing techniques , as standard, all Heli-Cal shaft couplings are shot peaned and hard anodised to further reduce the stress raisers within the coupling to make a more reliable part. For the more arduous of applications we have invested in the technology to incorporate a stress relief hole that reduces the stress concentration the coil finish to the solid hubs. Incorporating a stress relief hole reduces the stress concentration by taking the existing sharp edge and modifying it to be a smooth transition from the coil end to the solid hubs. A stress relief can drastically increase the life of the shaft coupling.
Utilising years of experience and flawless production techniques, the single piece construction totally eliminates any form of friction wear within its design, whilst also ensuring a zero-backlash and no torque loss operation. If you require further technical information on this product, please do not hesitate to contact our sales engineers who will be more than happy to help you.
For more information on Magic Carpet fix talk to Abssac Ltd
Enquire Now
List your company on FindTheNeedle.