
Sign In
COLD WEATHER WELDING
19-01-2022
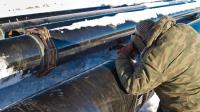
COLD WEATHER WELDING
A good weld takes skill, patience, access to quality equipment and ideally, good weather. There’s some flexibility for hobby welders, such as when and where you weld, but for professionals, you often get little choice. Your customers are relying on you to produce high-quality work even in winter. Professional welding projects are rarely halted by cold weather, and this is achieved by welders who know how to protect themselves, their equipment and their materials from the elements. Today, we will discuss the issues and solutions associated with welding in cold weather.
Keeping Yourself Warm & Comfortable
The first thing to consider when welding in cold weather is your clothing. You must maintain feeling in your fingers to weld safely, and you can’t afford to let the cold distract you. If you’re uncomfortable, the quality of your weld will suffer, so wrap up warm and ensure you’re wearing sensible clothing that doesn’t restrict your movement. Welding is a manual, physical process that requires concentration, which can diminish if you’re uncomfortably cold.
Of course, it’s not just about maintaining quality welds; you also need to consider your own safety. If you’re welding in an elevated position, you’ll need to ensure you’re using fall protection equipment and quality work boots with good grip to reduce the risks of slipping on icy scaffolding platforms. Whatever you wear to protect yourself from the cold, ensure your outer layer is flame retardant, you’re wearing quality, heavy leather gloves with a spare pair on hand in case yours get wet, and you’re not wearing any polyester. As welding gas suppliers, we also stock a range of welding safety equipment suitable for cold-weather welding.
Keeping Your Equipment Safe
In winter, consideration also needs to be given to your welding equipment, particularly when it is being stored. If you’re following the gas cylinder storage rules, ensuring your gas is stored in a well-ventilated area, away from heat sources and combustible materials, cold weather should not affect your MIG welding gas or TIG welding gas.
Your welding machine and rods should be treated with caution in cold weather. Ideally, welding machines should be kept in a dry, tepid environment. However, manufacturers understand that isn’t always feasible, and most good welding machines are built to be heavy-duty and withstand fluctuations in temperature. It’s actually the dust and moisture that come with cold weather that you should be wary of. Excess moisture that finds its way into your welding equipment can damage the machine and cause corrosion. Therefore, it’s advisable to keep your welder covered in winter when not in use to protect it from dust and moisture.
Industrial welding supplies like welding rods should be kept warm, dry and treated with care. If a welding rod becomes wet when in use, the heat from the arc can cause the shielding layer of the rod to crack and crumble from the rod during a weld. Water vapour created by a wet rod can contaminate the weld and offer little shielding of the weld puddle.
How Are Welding Materials Affected by Cold Weather?
Most metals will become brittle at low temperatures, in fact, they will have a narrow but tangible temperature range at which they transition from ductile to brittle. For many types of steel, this will occur at 0oC, making it difficult to weld in cold weather. However, stainless steel’s ductile-to-brittle transition temperature is much lower (around -200 oC), allowing for safe welding in winter without the risk of shattering. Before welding at low temperatures, you should check the ductile-to-brittle transition temperature specific to your chosen welding material.
Weld Strength in Cold Temperatures
The strength of a weld can be affected by cold temperatures through cracking and poor penetration, which occur when the weld cools too rapidly. Since the rate of heat lost is directly proportional to the temperature, we know that cold-condition welds will cool faster. There are other factors that are at play here, including the chemistry of the steel, and the hydrogen levels in the weld and the humidity levels of the work environment, but cold weather can heavily impact weld strength and quality.
Preheating Metal Workpieces
A weld will fail if the base metals are not penetrated correctly due to cold weather, which can be incredibly dangerous, particularly for large, heavy-duty projects. When cold, base metals can immediately suck the heat from a fresh weld. This is what leads to cracking and poor penetration. Preheating the workpieces is the advisable solution. It is typical to use an acetylene gas torch, and although it can take some time to get the metal up to temperature, it is well worth it to ensure a high-quality weld, even in winter.
Cold weather impacting your welds is only logical since welding is a thermal process. As long as you stay aware of all the issues we’ve discussed today, use high-quality workpieces and get your welding gas from reputable bottled gas suppliers, you should be able to weld successfully in cold temperatures. Here at Adams Gas, we supply a wide range of gases suitable for different types of welding. Please contact us if you would like more information about our products.
For more information on COLD WEATHER WELDING talk to Adams Gas
Enquire Now
List your company on FindTheNeedle.