
Sign In
UNDERWATER WELDING
04-03-2019
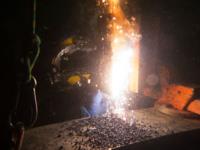
Also known as hyperbaric welding, underwater welding is an extreme form of welding that only the most talented, skilled and adventurous welders can begin to approach. In this article, we will look at the kinds of situations that might call for a spot of underwater welding, how one controls the electric arc below the surface, and what kinds of results you can expect to see compared to dry welding.
When to Weld Underwater
You might be thinking that any benefits of hyperbaric welding would be immediately outweighed by the difficulty and danger, but sometimes an emergency repair task will demand the presence of an underwater welder.
The quality of an underwater wet weld is never superior to a dry weld due to the number of interfering factors, but a wet weld can provide an adequate temporary solution where an emergency repair is needed. Once the temporary solution has been placed, the area in need of maintenance would be best served by being brought to the surface and corrected there. If this isn’t possible, a dry chamber system could be deployed to create a temporary atmosphere around the point of interest; this would allow welders to perform a stronger, dry weld below the waves.
How to Weld Underwater
Wet welding is performed through a stick weld, using an electric arc for the source of energy. The welding gas materialises as a thick layer of bubbles to shield the weld area from water and oxidisation.
This bubble is usually formed from a mixture of hydrogen, carbon dioxide and carbon monoxide. Once the welder moves the gun onto a new section of the structure, the bubbles leave with the gun which could cause problems for the newly unprotected welded surface. Without any protection from the surrounding water, the new weld could cool too quickly or even oxidise. This causes poor strength in the weld and results in cracking.
In order to combat this issue, wet welders leave behind a liquid metal called slag as they move along the seam. This metal sits on top of the new seam which gives the weld more time to cool properly but also reduces the opportunity for oxidisation to occur.
Another problem faced by underwater welders is bubbles. They might sound like a flimsy problem at first, but consider the damage they could cause to your weld when they are obstructing your vision. These bubbles come both from the diving suit and the welding gun, but the ones from the welding gun cause the most issues because these bubbles also have a habit of moving the weld puddle faster than anyone would like. The bubbles can also break the electric arc if the two cross paths.
Staying Safe during an Underwater Weld
Equipment is stricter for wet welds due to the dangers faced by the workers. To begin with, it is important for the diver to be completely sealed; their heat resistant gloves should connect with the rest of the suit without gaps. Without this precaution, there is a chance that some misplaced slag could float into the welder’s suit and burn them.
It is also important for the diver to be appropriately tethered to the surface in the event that they face a scary hazard known as a Delta P. This is caused when two different bodies of water meet and the differences in their pressures causes one body to rush in the direction of the other, creating a strong pull in the water. Without strong tethering, the diver could be pulled away without warning, and this could ultimately result in drowning, hypothermia or the bends. As part of the protection against Delta P’s, wet welders should also carry some ability to communicate their danger and location to workers above ground.
welding and cutting underwater
Salaries
Achieving the necessary qualifications to secure a position as an underwater welder can be fairly expensive, beginners can expect annual salaries of £23k, soaring up to £63k for the top ten per cent. While these wages might seem high, there is a lot to consider before you throw yourself into a diving-welding career. This is a career that is both mentally and physically demanding, as well as being one of the most dangerous jobs in the world.
The majority of us will likely continue to weld exclusively above the waves, with great respect for those skilled enough to venture into the cold and dark waters. Underwater welders carry out all of those necessary repairs on marine structures like oil rigs, offshore wind farms and even ships.
For more information on UNDERWATER WELDING talk to Adams Gas
Enquire Now
List your company on FindTheNeedle.