
Sign In
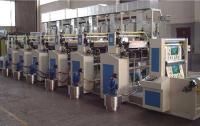
Flexographic printing is made by creating a positive mirrored master of the required image as a 3D relief in a rubber or polymer material. Flexographic plates can be created with analogue and digital plate making processes. The image areas are raised above the non image areas on the rubber or polymer plate. The ink is transferred from the ink roll which is partially immersed in the ink tank. Then it transfers to the anilox roller (or metering roller) whose texture holds a specific amount of ink because it is covered with thousands of small wells or cups that enable it to meter ink to the printing plate in a uniform thickness evenly and quickly (the number of cells per linear inch can vary according to the type of print job and the quality required). To avoid getting a final product with a blurred look, it must be ensured that the correct amount of ink is applied on the printing plate. This is achieved by using a metal scraper, called a doctor blade. The doctor blade removes excess ink from the anilox roller before inking the printing plate. The substrate is finally nipped between the plate and the impression cylinder to transfer the image. The substrate is then transported through the drying system usually hot air, which allows the inks to dry before moving on to the next application.
For more information on Flexographic Printing talk to Advanced Converting Equipment Ltd
Enquire Now
List your company on FindTheNeedle.