
Sign In
Advanced Grinding Solutions at MACH
25-03-2022
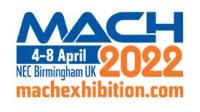
Advanced Grinding Solutions (AGS) has booked one of its biggest ever stands of 100 sqm at the forthcoming Mach show with all of the machines receiving UK debuts on their stand 320 in hall 17. None of these machines have been exhibited here before and therefore many UK engineers will be getting their first opportunity to see this range of advanced grinding and finishing machinery; the widest range on display at Mach.
AGS is showing the new Rollomatic 660XW GrindSmart multi-axis tool grinding machine with this being the first machine of several sold into the UK having been purchased by a leading UK cutting tool manufacturer.
The unique hybrid design of this latest Rollomatic machine combines, for the first time, the power and performance of a blank prep cylindrical grinder with the flexibility of a multi axis tool grinder to allow for all machining operations to be carried in one single automatic operation on the same machine and in one clamping. Therefore, for the very first-time cutting tools may be machined complete in a highly efficient single grinding process. The use of this technology also brings dramatic gains in production efficiency for tool manufacturers and the savings made are enormous because lengthy set ups on multiple machines are avoided all together, and the handling and storage of partly finished tools between machines is also negated completely. Typical production efficiency from the traditional multi machine production method for standard end mills is in the region of 11% and this is increased to some 82% on the Rollomatic 660XW machine. There are also large savings in manpower as the number of different machine types needed is greatly reduced. This is a totally new design of grinding machine that despite combining all necessary grinding operations actually has a smaller footprint than standard tool grinding machines that do not have a true cylindrical grinding capability. Like all Rollomatics it is also an extremely accurate machine that is easily capable of holding tight tolerances of just 2um on tool runout across large batches of tools and as with all Rollomatic grinding machines comes with the industry leading 3 years unlimited hours parts and labour warranty.
Also on display for the first time in the UK is the latest Tschudin Cube centerless grinding machine. The Tschudin Cube machine benefits from a highly radical design that sets it apart from all other centerless grinding machines as was acknowledged by it winning the prestigious Red Dot Design Award.
The Tschudin Cube machine enables users to achieve significant productivity gains and the machines particularly quick and flexible changeover times help to minimise machine downtime. What sets the Cube machine apart in particular is its very small size and radical open design for easy access. Users only need access to the rear of the machine to perform maintenance and servicing tasks, which means that several machines can be positioned together without any gaps. The grinder can be manually loaded in a very safe and ergonomic way outside of the grinding zone. The Cube uses Tschudins patented W-axis which has the workrest blade mounted onto its own CNC axis that allows for parts to be loaded to it outside of the grinding area making loading efficient, fast, and very safe. Traditional centerless grinding machines require parts to be loaded to a fixed work-rest blade that sits inside of the machine between the grinding wheel and control wheel making loading difficult, more expensive, and sometimes unsafe. This also makes changeovers more complex and therefore lengthier. The Tschudin machine overcomes all of these issues and claims to be the world easiest and fastest centerless grinding machine to set-up as the grinding and control wheel can be changed in only around 6 minutes. AGS has sold this highly advanced Tschudin grinding machine to Hydraulic Projects Ltd of Dawlish; a specialist manufacturer of very high precision hydraulic control valves and pumps. This is part of a large investment in new machinery as Hy-Pro, that were founded in 1966, and is still a family-owned company, looks to expand further and to increase its manufacturing capabilities at its base in Devon.
Receiving its UK debut, and exhibiting here for the first time ever, is Comat with their C-120 filtration system. Comat Superfiltration systems are engineered to filter neat cutting oil to 2-3 microns (with a classification NAS 1638 – ISO 4406 better than new oil), whilst constantly maintaining a stable temperature (+/- 0.2 degrees), without compromising filtration or flow rates so to ensure maximum consistency over time. Comat Superfiltration systems minimize the running costs to obtain the lowest cost per liter of oil filtered. The C120 is the latest generation of compact Superfiltration systems designed to manage a single machine tool, and is able to filter any type of contaminant (hard metal, high speed steel, medical steel, ceramic, brass) and to guarantee intelligent performance including energy saving and process optimization by remote monitoring from Comat’s headquarters near Milan to ensure systems are always delivery peak performance.
FLP (Fine Grinding, Lapping and Polishing Machines) are showing their new FLP380 single sided lapping machine. The broad range of FLP machines also include twin wheel - double sided CNC Lapping / fine grinding Machines and visitors to the AGS stand are invited to attend to discuss their requirements for the face grinding of components.
FLP Double Disc or twin wheel machines have 7 machines in the range offering a working disc diameter of between 540 and 1,300mm. These can all be offered with full automation via linear or robotic solutions, and weigh between 7 and 16 tons. These advanced machines are offered as high-precision versions with granite machine beds and the latest machine controls, drives and measurement technology. FLPs machines are in use across many branches of engineering including automotive, aerospace, bearings, optics and ceramics. FLP machines ensure that components are produced to the closest possible tolerances and at the highest production rates. Operator friendly simple machine operation is ensured as is the lowest cost per machined component.
Specialists from Krebs & Riedel will be present on the AGS stand to discuss all grinding applications and best use of their range of internal and external grinding wheels. Krebs & Riedel manufacture high quality conventional, diamond and CBN abrasives and are constantly introducing new types of wheels with improved grain structures and novel bonding systems that enhance grinding wheel quality and optimise performance. Companies involved in grinding are invited to meet the Krebs & Riedel specialists and to discuss their grinding issues and aims to improve their grinding processes. Apart from offering high stock removal rates to improve cycle times, combined with more consistent part quality by avoiding micro-cracks in the surface of sensitive parts, another large benefit of using Krebs wheels lies in large cost savings made possible by reducing wheel dressing requirements. This has the three major advantages of lower wheel waste due to less dressing, faster cycle times as wheels can be kept grinding longer in between dressing them, and also a reduced spend on expensive diamond rollers. Krebs and Riedel are developing new wheels all the time and those are added to the existing collection of over 60,000 different wheel types that are available from them.
The range of grinding and finishing machinery receiving its UK debut can all be seen on the AGS stand 17-320 at Mach. For further information please see www.advancedgrindingsolutions.co.uk or contact AGS on+44 (0) 2476 22 66 11
For more information on Advanced Grinding Solutions at MACH talk to Advanced Grinding Solutions Ltd
Enquire Now
List your company on FindTheNeedle.