
Sign In
COMAT Filtration Systems
15-10-2020
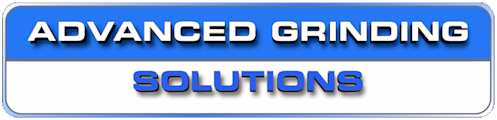
Advanced Grinding Solutions (AGS) of Coventry has announced a large number of recent sales for the premier Italian manufacturer of Filtration systems Comat for grinding applications.
Comat manufactures super-filtration systems that deliver ≤ 2-3μm filtration quality (making oil cleaner than unused oil as supplied new) and importantly do so throughout the entire working cycle whilst minimizing lifetime running costs and maintaining maximum coolant consistency. Importantly for end users, the Comat filter systems use their Intelligent Performance Technology that allows them to be remotely monitored in real-time during the manufacturing processes with customers filter systems fine-tuned by Comat to ensure that the optimum filtration quality is obtained at all times. Furthermore, depending upon the model, the Comat filter units can be monitored, controlled, and optimized by integrated controls or externally by PCs, tablets or smart phones.
AGS has sold an additional 5 Comat filtration systems to the tool grinding and medical engineering sectors in August and September; mainly for connection to the Rollomatic multi-axis grinding machines also represented in the UK and in Eire by AGS with existing UK Comat end-users already including Samwell Tools of Poole and AW Precision of Rugby amongst others.
Today, more than 20,000 machine-tools use Comat Filtration Systems, with more than 120,000,000 litres of metal working oil being super-filtered every single day. Comat operate globally and have a 30-year history in developing the most advanced filtration systems that are available. Comat's Superfiltration Technology uses continuously regenerating filtering media (diatomaceous earth, cellulose or other vegetable media), to ensure that particles larger than ≤ 2-3μm are removed from cutting fluids and the fluid is maintained at a stable desired fixed temperature of +/- 0.2 degrees. Oil cleanliness is measured according to internationally set and agreed standards such as the National Aerospace Standard 1638. Brand new, neat cutting oil is typically classified in category 9. However, with Comat Superfiltration systems brand new clean oil is brought down, and then held, to a finer filtration category of just 7 or 8.
Oil that is filtered by Comat systems does not need to be replaced and many clients report that they have never changed the oil for up to 20 years (save top-ups due to oil loss). Main applications for these filter systems include tool grinding on Rollomatic and similar grinding machines and also on turning machines and automatic lathes. Comat systems can operate with any oil having a viscosity ranging between 5 and 30 Cst at 40° C (104° F).
The filters media needs to be re-generated once per day for full production/heavy stock removal applications and this takes just 15 minutes or so and machines do not need to be stopped whilst this is carried out. If the system is fitted to a grinding machine used for regrinding cuttings tools then re-generation of the media would only be required every 1-2 weeks.
In terms of running costs then the Comat systems are usually only around 25% of the cost of running competitor filter systems who often rely upon expensive candles or filters that need replacing at a very high cost. Most of the end users supported by AGS are only spending around £250 a year on the Comat filter media as compared with the users of other systems facing huge bills when sets of filter candles or discs, that are aware item, need replacing.
Remarkably so the filtration levels from the Comat systems are so high that new virgin oil has to be go through several regeneration cycles in order for it to meet the finer filtered quality of older/used oil that is filtered within Comat filter systems. The low-cost media used in Comat systems is very cheap and as there are no cartridges, paper rolls or expensive candles to replace; Comat filters offer the lowest running costs of filter units.
Today 80% of sales are for Comat EVO systems that offer 24/7 monitoring and are equipped with a facility whereby the system when registering any issue will send an email/alarm warning to both the end user and to the Comat HQ to inform them of a problem. This said Comat units are extremely reliable and a check-up maintenance visit is only recommended every 2 years. During such a visit the history of all parameters since installation or the last service check can be recalled, and the system optimised when necessary to suit grinding or turning processes that may have changed slightly over that time.
Comat ECO systems are the basic version of Comat filter units and are offered to cost conscious customers that want highly economic solutions and do not want Comat's automatic remote diagnostics support. However, these systems of course still offer the same very high level of filtration and ongoing reliability.
Comat filtration systems ensure a higher and more consistent quality of machined components, increased lifetime of cutting fluids, reduced machine wear and importantly bring about an increased lifetime of grinding wheels and cutting tools. From small stand-alone systems to support a single grinding machine or lathe with a capacity of 60l/min up to centralized units that can cater for up to 12 grinding machines or 25 lathes with a capacity of over 1,000 l/min; Comat have solutions. Furthermore, these universal filtration systems can handle any type of contaminant including brass, carbide, ceramics, glass, HSS, special aerospace and medical alloys and PCD etc. The advantages of the Comat systems are clear; they offer large reductions in running costs, they filter oil to the very highest levels, they offer a constant quality of filtration, and thanks to their ability to be remotely checked and monitored offer hassle free ownership.
Comat continues to expand and today has a production facility of approx. 4,000 m² with a further office area of 1,000 m² at their base near Milan and their filtration systems will be shown in hall 7, stand 7091 at the forthcoming Grindtec exhibition near Munich where AGS personnel will be available to meet interested engineers looking for the finest filtration available.
For more information on COMAT Filtration Systems talk to Advanced Grinding Solutions Ltd
Enquire Now
List your company on FindTheNeedle.