
Sign In
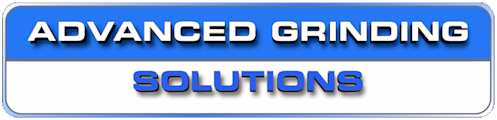
As a complete system provider for complex surface finishing, FLP Microfinishing is the only company in Germany to offer the entire range of industrial fine grinding, lapping and polishing machines for flat surface finishing from a single source. The four FLP product lines are new single and double sided machines (both standard and full CNC), fully rebuilt and refurbished machines, the supply of lapping consumables and tooling, and finally a large sub-contract lapping facility. FLP is a relatively young and fast growing company being started in 1996 by Thomas Rehfeldt. FLP started off manufacturing machines for others in Germany and then progressed into designing and manufacturing their own. They employ over 60 people at their main HQ in Zorbig, near Berlin, and have a world-wide distribution network of dealers including Advanced Grinding Solutions here in the UK.
The broad range of FLP fine grinding and lapping machines includes for both twin wheel – double sided CNC Lapping Machines as well as single wheel – single sided, Lapping machines. The size of machines ranges from the most basic of 400mm in diameter having three working stations up to the world’s largest 100 ton 5 meter diameter monsters constructed from multiple 26-ton solid granite blocks. These huge machines are 16 meters long, 8 meters wide and 4 meters high; in terms of capacity they will hold parts having a combined weight of 10 tons across all 3 working stations.
Around 25% of FLPs sales are for so called Fine Grinding machines that offer 2-3 times the stock removal of more traditional lapping machines with 75% of sales being for Lapping or Polishing machines that are used where there is a low stock removal requirement with a mirror finish and perfect flatness being the main targets. The fine grinding process, that uses Diamond or CBN wheels, is much cleaner than lapping and virtually eliminates work piece cleanliness issues. Furthermore, this process is typically many times faster than lapping and bridges the gap between traditional lapping and standard grinding technologies. Fine grinding will create a micro cross-hatched finish on parts that is akin to one after a Superfinishing operation that has advantages in terms of surface retention of lubricant whilst still offering very high degrees of flatness and a mirror like visual surface.
The FLP single wheel series of Lapping Machines comprises of very small and cost effective machines of 400mm in diameter having three dressing/control rings each of 145mm diameter up to 3.5 meter versions with dressing/control rings of 1.3 meters in diameter
The FLP Double Disc or twin wheel machines have 7 machines in the range offering a working disc diameter of between 540 and 1300mm. These are fitted with Siemens PLC controls, can all be offered with optional full automation via linear or robotic solutions, and weigh between 7 and 16 tons. These advanced machines are offered as high-precision versions with granite machine beds and the latest machine controls, drives and measurement technology.
In the FLP machine rebuild division, and regardless of the type and size of a customer’s old fine grinding, flat honing, lapping or polishing machine, FLP will carry out process and technology orientated improvements and general overhauls. The replacement of sub-assemblies for which spare parts can no longer be supplied, retrofitting of automation such as programmable logic controllers or replacement of materials with more wear resistant types, for example rustproof steel, in addition to the utilisation of frequency inverters with electrical drives to increase efficiency are all catered for. The many advantages of such a general machine overhaul are a large cost saving of up to 40% as compared with the cost of a new machine, shorter delivery times and of course an increase in machine uptime as compared with older worn machinery. Overhauled machines are fitted with PLC controls with integrated measurement controls with detailed graphic illustrations on new touchscreens and come with simple operator guidance. FLP also offers rebuilt used machines, often from stock, that have already been re-manufactured to an as-new standard as well as supplying replacement spare and wear parts for all market established machines.
FLP holds over £2.5million worth of lapping consumables in stock and offers end users of all types of lapping machine the largest range of wear parts and consumables. The range is vast and includes for over 4,500 different items such as lapping and polishing oils, fine classified silicon carbide, boron carbide, and special fused aluminium lapping powders, lapping and polishing fluids in water derived concentrates with integrated rust protection, honing oils for machining steel, non-ferrous metals, hard metals and ceramic, and diamond sprays, suspensions, powders and pastes with micro-grains of various specifications and grades from 0.25um up to 45um.
FLPs final product line is the sub-contract facility it offers its world-wide customers using their fully equipped factory work-shop that has a large variety of single and double sided lapping machines and all associated equipment that’s needed to produce fine ground and lapped components for its customers. FLP manufactures in excess of 20 million lapped parts a year for customers needing a sub-contract facility with some customers needing very small batches produced for them and others needing 250,000 parts a week every week. The sub-contract facility comprises of the flat honing, fine grinding, lapping, polishing and deburring of all components including full process documentation, measurements and statistics.
In terms of industries served, FLPs machines are in use across many branches of engineering including automotive, aerospace, bearings, optics and technical ceramics etc. Applications include the production of pumps, bearings, ceramic seals, fuel injection and transmission components. FLP machines ensure that all components are produced to the closest possible tolerances and at the highest production rates. Operator friendly simple machine operation is ensured as is the lowest cost per machined component.
Chris Boraston of Advanced Grinding Solution concludes; "FLP really does offer the one stop global solution for anyone with a lapping or fine grinding requirement including new machines, used machines, refurbishment of the customer’s own machines, tooling, consumables, spares, and a very large sub-contract facility".
More information on FLP including videos and brochures is available for download on the AGS website www.advancedgrindingsolutions.co.ukor contact AGS on +44 (0) 2476 22 66 11.
For more information on FLP Fine Grinding Machines, Lapping Machines & Consumables talk to Advanced Grinding Solutions Ltd
Enquire Now
List your company on FindTheNeedle.