
Sign In
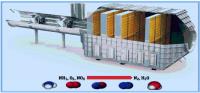
WIP.OCT.13. SCR. AGRIEMACH.p26:RHP.WIP.p27.qxd 08/10/2013 15:23 Page 1
S
26
elective Catalytic Reduction (SCR) is
a means of converting Nitrogen
Oxides (NOx) into Nitrogen (N2) and
Water (H2O), using an injection of urea
(AdBlue) with the aid of a catalyst.
A specialist company in the UK which
offers SCR technology is Agriemach Ltd.
Its systems are used on lean burn
applications and offer a very high
efficiency for the reduction of nitrogen
oxides.
Agriemach Ltd has experience with many
different fuel types and the issues
associated with them. The company offers
systems suitable for diesel and biodiesel
engines, natural gas and biogas, and
renewable fuels, and offer designs for a
multitude of engine power outputs.
David Kallmann of Agriemach tells WIP:
“Italy is famous for its premium quality
Parma ham. One of our customers is
currently using waste material from the
meat process to generate electrical
energy and heat.”
He continues: “This needs to be done in
a clean way, and so the customer selected
us to be the emission reduction system
partner on the project. Our experience
and know-how convinced them. A ‘perfect
SELECTIVE CATALYTIC REDUCTION
Systems for lean-burn
applications & NOx reduction
Agriemach Ltd offers a bespoke service for the design, manufacture and project management of
Selective Catalytic Reduction technology. WIP looks at two examples from London and Italy
handled by the company where system designs, dosing system upgrades, catalyst replacement and
everything from bulk urea tanks to heat & sound insulation materials have been supplied.
commissioning’ in 2012 proved our skills in
not only designing SCR systems but also
supporting the installation.
The client company in Italy ordered a
compact Urea/AdBlue control and dosing
system, with NOx sensing sensors allowing
feed forward and feedback control of the
Urea/AdBlue flow.
The factory features a 400kW engine,
and NOx reduction is >80% over 6,000 8,000
running hours every year.
There
are
even
plans to build a sister plant in Italy
soon.
David
Kallman adds: “Agriemach was
behind
a 2013 London-based bio-diesel
project
which required both soot and NOx
reduction.
We
met with the client to go
through
the engine details, fuel
specification
and space restrictions. With
our
combined years of experience and
global
knowledge, we were able to offer
the
complete solution from design,
delivery
to commissioning.”
The
London site features a fuel called
FAME
- Fatty Acid
Methyl Ester.
This
is
traditional
biodiesel, produced by
processing
raw vegetable oil and/or
animal
fats.
The
resulting product is chemically
different from petroleum diesel, has
different properties, and meets a
different quality standard. The most
common feedstock for FAME biodiesel in
the US is soyabean oil, but in Europe
rapeseed or canola oil is typically used.
The engine size at the London site was
derated to 130kW, and NOx reduction has
been estimated at 90%.
Says David: “We work with many
different fuel types from natural gas to a
whole host of bio-fuels. Agriemach is a
one-stop solution for meeting stationary
engine emissions targets as we offer
solutions for the reduction of NOx, Carbon
Monoxide (CO), Hydrocarbons (HC),
Particulates (PM), as well as supplying the
Bulk Urea Tanks and Delivery, Compressor
Units, Heat and Sound Insulation
Materials, Exhaust Gas Heat Exchangers
(EGHE) and Silencers.”
He concludes: “We offer a complete
solution. We design bespoke systems using
CAD offering a seamless integration to our
customers drawings. For certain
challenges, we also offer Computational
Fluid Dynamics (CFD) to ensure our design
is going to work before releasing it to
production. “
Internet link
Internet link
www.agriemach.com
O CTOBER 2013 • WORLDWIDE I NDEPENDENT P OWER
WIP
For more information on Systems for lean-burn applications & NOx reduction talk to Agriemach Ltd
Enquire Now
List your company on FindTheNeedle.