
Sign In
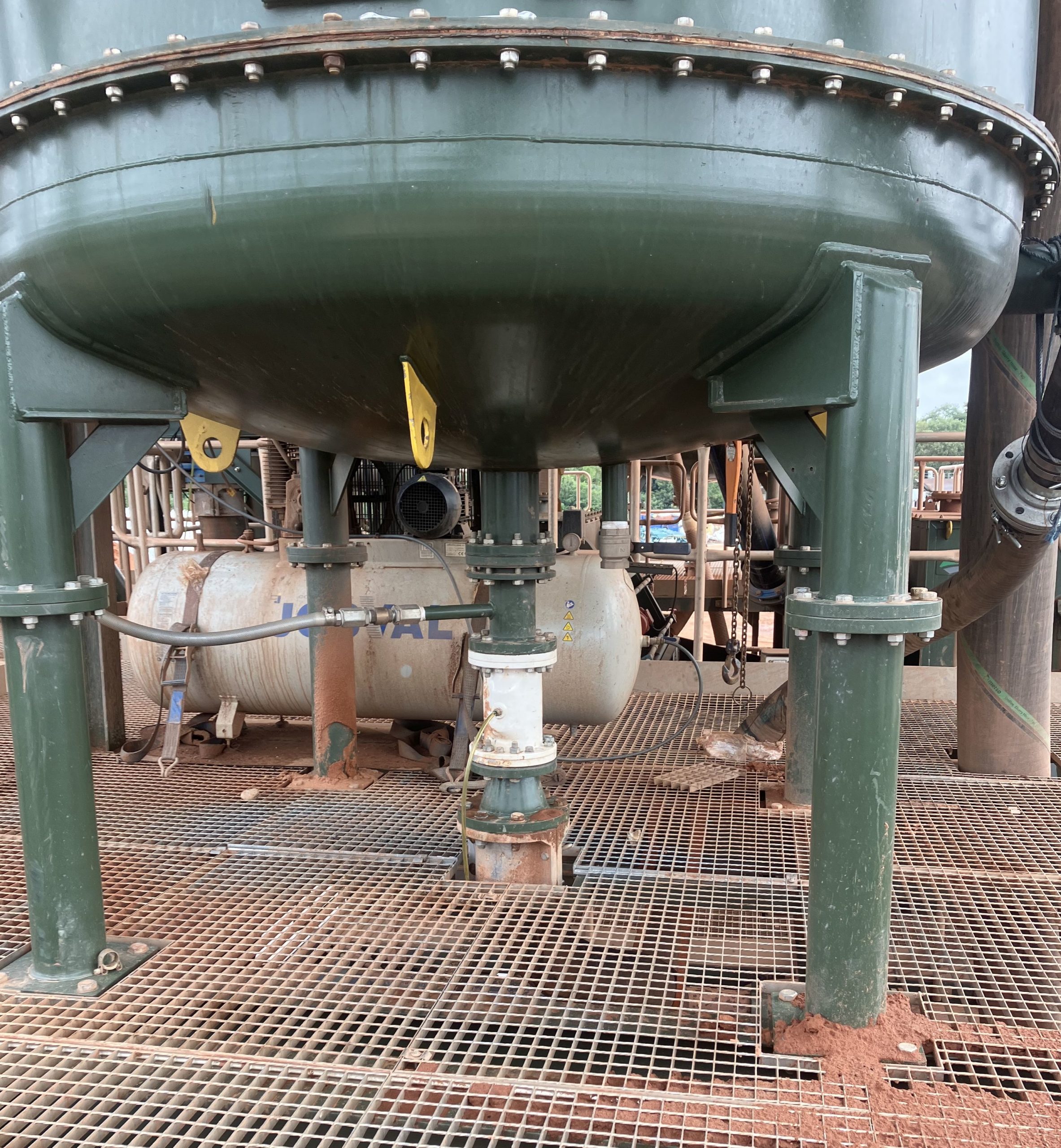
A sand processing company have been successfully using Pinch Valves for 28 years
The valves were originally chosen and installed onto the equipment by an Original Equipment Manufacturer, who produce a comprehensive range of static and mobile equipment. The OEM also supplies specialist processing equipment to create high grade silica sand from thin layers of soil and overburden.
Controlling the Flow of Sand with Valves
The fine sand passing through the full bore of the valve is 0-2mm in size, and ambient in temperature. The sand flows through with water under gravity, and moves through the valve from a circular tank above which has sand and water inside. The tank is approximately 2.0 metres diameter and 1700 tall.
Positioned underneath the sand classifier, the valve is normally open, installed in the vertical position, and runs all day with sand flowing through it for 10 hours per day on average.
2-3 Bar is used to fully shut off the valve, which is the optimum closing pressure for this scenario, since there is no pressure of the sand being blown through the valve with it being gravity fed. AKO Pinch Valves require 2 – 2.5 Bar above the line pressure to close.
The Performance of Pinch Valves with Sand
The purpose of the Pinch Valve is to control the flow of sand within this application. The Original Equipment Manufacturer originally decided to use a Pinch Valve for sand as a trial against their standard system. They told us that the valve works well but there is wear resistance, as expected with the abrasive nature of the sand. The rubber sleeve is replaced when it wears out approximately every 6 months.
Pinch Valve used within this application – VF100.03X.35.30LA
VF model, air operated, aluminium body, aluminium flanges PN10/16 with stainless steel bushing contact parts, natural rubber sleeve.
The company would like to use more Pinch Valves if they can reduce the wear rate. Mild steel bushings on the flanges/clamping plates were being used but AKO UK advised the company to use flanges with stainless steel bushings instead, which will last a lot longer for this particularly abrasive application.
To help to keep the plant up and running in the most efficient way, AKO UK also advised for the end user to keep spare valves, replacement flanges with stainless steel bushings, and replacement internal rubber sleeves on stand by, to replace any parts that fail immediately, ensuring there is as little down time as possible.
Read more Case StudiesExperts in Valves for SandNeed a Reliable Valve Solution? We can help! Talk to our sales team today:Contact Us
For more information on Sand Processing using Valves talk to AKO UK Ltd
For more information on Sand Processing using Valves talk to AKO UK Ltd
Enquire Now
More related to Sand Processing using Valves
List your company on FindTheNeedle.