
Sign In
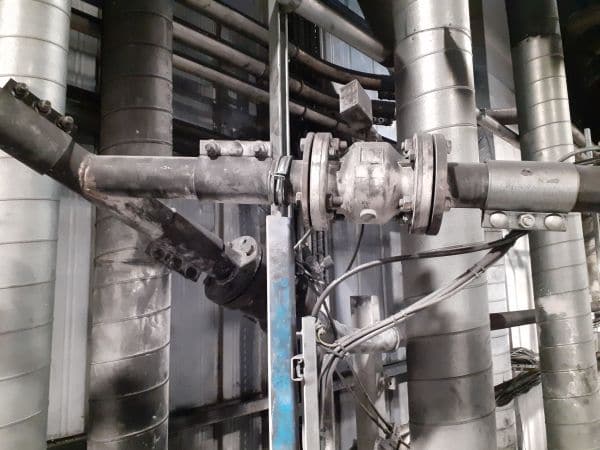
An international manufacturing company producing black plastic masterbatch and conductive compounds have been using AKO Pinch Valves within their applications. They are the leading global specialist in what they do, and AKO UK are pleased to be supplying the company with their Pinch Valves to successfully assist with the manufacturing processes.
The company works closely with major carbon black, carbon nano, graphite and graphene producers in developing new and improved Black Masterbatches and conductive compounds. Therefore, the site is fairly dirty due to the process and materials used, but this doesn’t affect the performance of the Pinch Valve.
The black masterbach that the company manufacturers is sold onto the end user, and is used in the form of electrical components, personal electronics, personal care products, toys and much more. The automotive industry is also a user of the black masterbach, within various areas inside and outside of vehicles.
Valves for Chalk Application Details
The DN80 aluminium AKO Pinch Valves of the VF Series installed within this site are positioned horizontally. The position of the Pinch Valve makes no difference to it’s performance, it all depends on existing pipework and what space there is on site.
The material flowing through the full and true bore of the AKO Pinch Valve is chalk at ambient temperature. The chalk is blowing through the lines at a pressure of 0.5 BAR. The chalk has it’s own conveying line, leading straight to the production line.
The Valve for chalk is held in the normally closed position with 4 BAR (60 psi), and a solenoid valve is charged to release the air of the Pinch Valve, meaning that the natural rubber tube or sleeve inside the body of the pinch valve is pushed open to allow the chalk to be conveyed through the line.
AKO Recommendation
4 BAR holding back 0.5 BAR of media is too high and would be putting more ‘stress’ on the valve for chalk rubber sleeve than necessary. We would recommend reducing the closing pressure to 2.5-3 BAR to allow a longer lifetime for the rubber sleeve. Over-pressurising the sleeve is a typical Pinch Valve failure, therefore using the correct advised pressures will help it to last longer.
Pinch Valve used within this application – VF080.03X.31.30LA
VF model, air operated, aluminium body, aluminium PN10/16 flanges with mild steel bushings, natural rubber sleeve.
Valve for Chalk Performance
The black masterbatch manufacturers have been using Pinch Valves for chalk conveying for 20 years. The AKO Pinch Valve was already fitted on an installation supplied to them by another company, but they have expressed that their overall satisfaction is good, with one of the site engineers quoting:
“The opening and closing times of the pinch valve are instant which is really useful for our processes. We had tried ball valves in the past, but the reaction times were just not quick enough, and we found that they would rust fairly quickly, leaving less of an opening for the chalk to pass through. What we love about the pinch valve is that they are self cleaning, and the chalk does not become stuck around the rubber sleeve.”
Valve for Chalk Excellent Total Cost of Ownership
The pinch valve for chalk users of this particular application only have to replace the rubber sleeve once it has fully worn or come to the end of it’s life. No other parts are needed to be replaced, only cleaned. This gives a fantastic total cost of ownership (TCO) in general, as with many other conventional type valves you will find that lots of little separate parts will continue to need replacing.
Read more Case StudiesExperts in Valves for ChalkNeed a Reliable Valve Solution? We can help! Talk to our sales team today:Contact Us
For more information on Valves for Chalk in Black Plastic Masterbatch Production talk to AKO UK Ltd
For more information on Valves for Chalk in Black Plastic Masterbatch Production talk to AKO UK Ltd
Enquire Now
More related to Valves for Chalk in Black Plastic Masterbatch Production
List your company on FindTheNeedle.