
Sign In
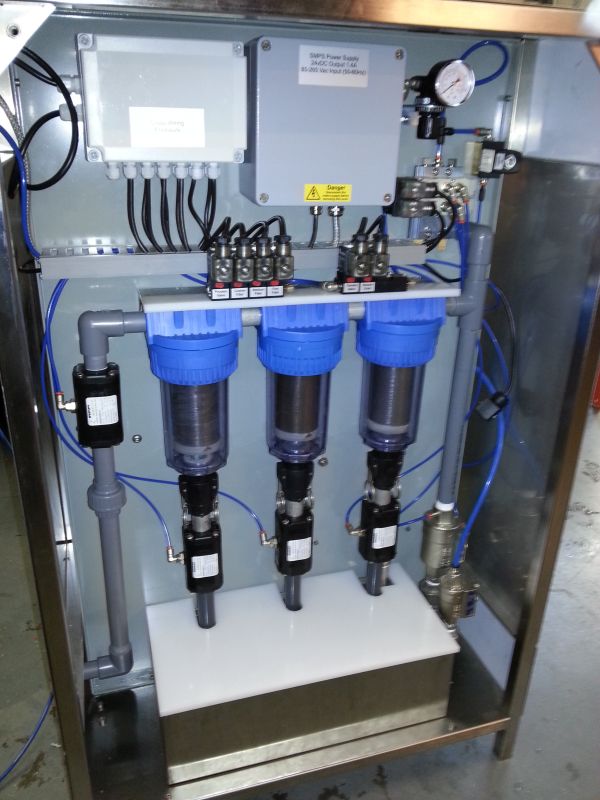
A specialist measurement supplier to the paper Industry are using valves within their bespoke systems.
The implementation of process consistency control together with wet-end control schemes around retention and charge applications can provide a fast payback on investment.
Improved process stability helps to reduce the production environmental impact. Savings on water usage, effluent load and energy can be realised.
Paper Manufacture with Pinch Valves
The media passing through the pinch valves within this system is process water with a trace of cellulose fibre, which travels through the valves at 2 Bar. The temperature of the process water media is 35-55°C.
The pinch valves for process water are installed in the vertical position for drainage, and are normally open. Performing 200-250 cycles per day, the VMP compact Pinch Valves are the ideal solution for this application. 4.5 Bar is used to fully shut off the valves, assisting in the filtration flushing cycle for a batch measurement.
For the paper process, this company’s sensors are used from; stock preparation, PM wet-end, excess water systems, broke recycling and in the influent. They are able to deliver custom sensor solutions for unique or difficult applications.
Pinch Valve used within this application: VMP020.03XK.72
VMP model, air operated, black POM plastic body & BSP threaded ends, natural rubber sleeve.
Abrasion Resistant Valves for Process Water Experience
The paper manufacturing company have been using AKO Pinch Valves for 8 years. The high cost and wear of the rotary actuator were what made the company decide to use pinch valves within this application. The application causes high wear rates, so they knew they needed a product that could handle abrasion.
The AKO Pinch Valve for process water has a durable and abrasion resistant rubber sleeve inside it’s casing, and is also high in elasticity. These benefits allow the valve to perform at it’s best for a reliable and effective process within any application.
This company told us at AKO UK that they are very satisfied with the Pinch Valves for process water they install on their systems. The rubber sleeves, being the only wearable part of the valve, are replaced every 2-3 years. With the rubber sleeves being extremely low cost, it gives a very attractive total cost of ownership for the user.
3/2-way solenoid valves are also used within this application. There is a potential for more pinch valves in the future here, depending on skill locally. The company will also be continuing to keep spare sleeves in stock on the shelf, and replace them when needed.
Read more Case StudiesExperts in Valves for Process WaterNeed a Reliable Valve Solution? We can help! Talk to our sales team today:Contact Us
For more information on Valves for Process Water in Filtration Flushing Cycle talk to AKO UK Ltd
For more information on Valves for Process Water in Filtration Flushing Cycle talk to AKO UK Ltd
Enquire Now
More related to Valves for Process Water in Filtration Flushing Cycle
List your company on FindTheNeedle.