
Sign In
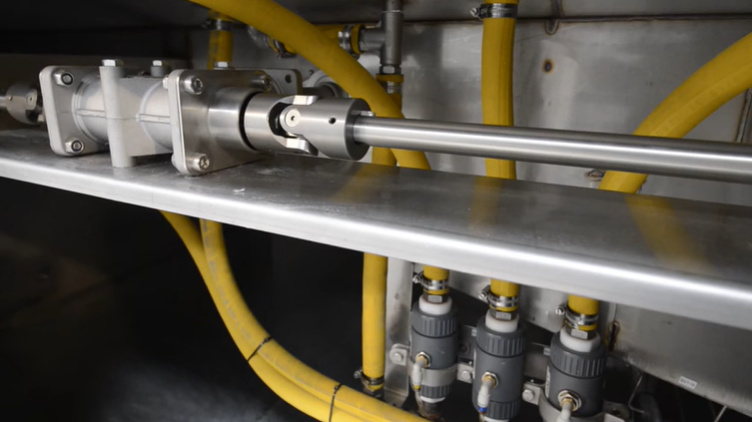
A company manufacturing a wet blasting and rinsing system that uses leading-edge technology is using Pinch Valves from AKO on this extremely well designed machine.
Wet Blasting With Ease
Constructed from high-grade stainless steel, continuously welded to form a water and dust-tight robust structure, work pieces are loaded directly on to a 900mm x 920mm processing trolley by overhead hoist or via roller conveyor system. As components are driven into the main wet blasting enclosure, users can have up to 12 blast nozzles operating concurrently: eight nozzles above the work piece and four below. Oscillating across the work piece, the trolley traverses through the enclosure at a pre-set speed allowing complete customisation in line with production needs.
The applications that this system is involved with are component cleaning, die cleaning, edge preparation, surface activation for PVD/CVD coatings, and post treatment polishing & peening in the Extrusion Die Cleaning and Round Shank Tools industries.
Pinch Valves used within this application – VM015.03X.70.80
VM model, air operated, PVC body, white POM plastic BSP threaded ends, natural rubber sleeve.
Change of Valves for Wet Blasting Model for Quality Efficiency
The company were originally using AKO’s VMP type Pinch Valve for wet blasting (pictured below), which have ‘squared’ bodies and unfortunately did not fit into their standard pipe-clamps so neatly.
The VM type Pinch Valve (pictured above) has cylindrical bodies, which the company found were more suited to their standard pipe-clamps.
These Pinch Valves for wet blasting are subjected to a line pressure of 3 Bar, and a closing air pressure of 5 Bar, both of which are well within the specified operating perameters for the valve.
The valves are fitted onto a rigid pipe as shown. In three of five other locations on the machine, the Pinch Valves for wet blasting are supported at the bottom by the manifold, but only connected to flexible hoses at the top, which provide minimal support. A fourth is cantilevered of the back of the manifold.
The company have been successfully using AKO Pinch Valves from the VM range on this wet blasting system for 9 years to date.
VM/VMP Pinch Valve Differences
Aside from the difference in body shape as mentioned above, the VMP Pinch Valve is a much shorter, compact Pinch Valve. It is also slightly lighter in weight. For most valve users, the VMP model is the prefered choice because it is also more cost effective, being cheaper in price.
Because of the shorter face to face length, the rubber sleeve inside the VMP body is shorter than the sleeve used in the VM Pinch Valve. The shorter sleeves are characterised with a ‘K’ at the end of the sleeve part number. For example:
M015.03X – 15mm Natural Rubber Sleeve for VM type Pinch Valve
M015.03XK – 15mm Natural Rubber Sleeve for VMP type Pinch Valve
Read more Case StudiesExperts in Valves for Wet BlastingNeed a Reliable Valve Solution? We can help! Talk to our sales team today:Contact Us
For more information on Valves for Wet Blasting & Rinsing System talk to AKO UK Ltd
For more information on Valves for Wet Blasting & Rinsing System talk to AKO UK Ltd
Enquire Now
More related to Valves for Wet Blasting & Rinsing System
List your company on FindTheNeedle.