
Sign In
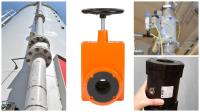
Hose valves with a rubber pinching tube inside the housing to stop or control the flow of media is often used in a vast range of industries and applications all over the world. This page will discuss some examples of hose valve applications, their benefits, and how they perform.
Hose Valves Testimonial:
Bill Kingfisher – Quality Manager
“9 out of 10 of the engineers that I work with on our food site said that they prefer using hose valves on our system rather than ball valves. We were fed up of ball valves clogging up and causing us problems. Finding out about hose valves was like a God send to our company! We now have so many less failures and our system runs more smoothly.”
Hose Valves Processing Raw Materials
One example of an application where a hose valve will be most suited to the job is a cement plant. Hose valves have been used successfully in the manufacture of cement for over 15 years. The standard natural rubber sleeves inside the hose valves have proven to be the best solution for controlling the movement and flow of concrete and cement media.
Also, hose valves are part of an ever-growing industry manufacturing lime mortar products. Companies are using dry mortar batching plants in the UK to manufacture lime building products using hose valves. The batching plant is fully automatic and the hose valves keep a continuous supply of raw materials to various parts of the plant. So far, a DN80 flanged hose valve with internally threaded flanges and a DN15 plastic hose valve, both with standard natural rubber tubes, are installed and have not needed to be maintained for over 2 years.
Hose Valves with Flour
Hose valves have been proven, after tests, that they are the successful solution to the flow of flour and other baking products in the many Warburtons bread manufacturing factories around the UK.
Hose valves with 100mm and also 125mm diameter flanges with white food quality sleeves have been the successful working solution for maintaining the movement of the flour. The FDA approved rubber sleeves are lasting longer in rubber hose valves than when the same company were using ball valves because the ball valve would become continuously plugged, blocking the flour flow.
Over the years, this company have found that the soft seated rubber sleeves inside the numerous hose valves across their different plants are lasting approx 15 months. This is an exceptional lifetime of a rubber membrane of a hose shut off valve, especially with the coarse media passing through it such as salt.
Hose Valves and Water Flow
Hose valve types with a smaller bore size such as 25mm have been victoriously used in a water pumping system. The hose valves are used on a landfill site using air pumps operating at about 4.5 bar where it is required to pump to another area when the tank fills up and the valve closes.
One hose valve is often tested on a trial basis and when it is proven to be working satisfactory, more hose valves are installed on various other plants.
Hose shut off valves are also used in other applications where water is used on road sweeping machinery. After recently developing a recycled water system where contaminated water is coarsely filtered and directed down to a suction pick-up system, the hose valve has worked wonders for the job.
Furthermore, hose valves with a true bore and low maintenance are proving to be the ideal solution for handling and controlling the flow of media in the following areas of industry:
The manufacture of gelatin for soft gel capsules
Sand foundries & sand blasting machinery
Mineral powder
Crop spraying
Aqueous solution of Aluminium Chlorohydrate
Wet shot blasting cabinets for water
Water based china clay slurry for Filtration System
Iron oxide powder
Environmentally friendly biochemicals that can replace oil-based products.
Powder coating plants
Sludge/sewage
Animal remians
Plastic pellets
Powdered Sulphuric Acid & Ethyl Acetate
Sodium Carbonate powder
Concrete on-off dispensing
A Hose Valve for Pharmaceutical Uses
Tri-Clamp connection for hose valve
Aside from large industrial applications such as those mentioned above, hose valves are also being used by pharmaceutical companies manufacturing small medical tablets. One particular company is using the hose valve with stainless steel tri-clamp end connections. For this application, the valve will be kept normally closed and will then open for a number of seconds to pass tablets through by gravity falling pressure.
How much Control Pressure should be used?
Hose valves can sometimes have too much control pressure applied to close them by an engineer on site, which can shorten the life of the hose valve rubber membrane. For example if 6 BAR of pressure is used to close this tube/hose valve on a gravity fed pharmaceutical application, this is too much because only 2-2.5 BAR above the line pressure is needed to fully close the hose valve. Therefore, only 2 BAR is required to close, as there is no line pressure present in the flow of tablets.
Repairing a Hose Valve
fitting tool for hose valves
Fitting / repair kit for hose valves
Hose valve repair takes place by replacing the rubber hose inside the housing. The process of replacing the rubber hose inside a hose valve is quick and simple using a fitting kit, which consists of mounting wood, mounting pipe, lubricant paste, and assembling screws, nuts & bolts.
Replacing the rubber sleeve inside a hose valve is a procedure which should not need taking place very often, and it is the only wearable part inside the valve. Hose valve parts are very low cost and easy to replace.
Hose valves sometimes operate with high temperatures being exposed to the rubber sleeves, so the rubber hoses are routinely replaced at intervals by an engineer. It is important that the correct sleeve material is used for any application with pneumatic hose valves, taking into account the temperature range for each material. For example, natural rubber is rated to 80 degrees C, whereas EPDM is rated higher to 120 degrees C.
Hose Valves for Confectionery Production
Hose valves are now installed on a UK plant producing sweets after a successful trial period. The particular application is used with a vacuum, which pumps at 280/260 millibar. The hose valve (with an aluminium body and stainless steel G3″ end connections), is normally closed, and has approx 220 cycles per hour. The plant runs about 14 hours a day, 5 days a week.
Another hose valve on the same plant has special stainless steel weld-on connections which means the user can weld on any specific fittings required.
For more information on Case Studies about Hose Valves – Performance & Advantages talk to AKO UK Ltd
Enquire Now
List your company on FindTheNeedle.