
Sign In
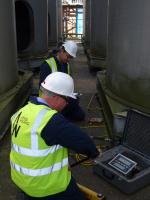
The ability to maintain consistently high product quality and optimise operating capacity are just some of the reasons why ensuring the accuracy of measuring instrumentation is afforded so much importance within the manufacturing industry. Indeed, calibration can provide a number of benefits for manufacturers, as well as ensure the safety of both employees and consumers alike.
However, traditional calibration methods are typically associated with production downtime and high costs. This can lead to instances of manufacturers prioritising calibration for some measuring instrumentation at the expense of those which are considered to be less essential. But the risk of neglecting calibration can lead to even greater costs being incurred.
Applied Weighing’s HydraCal direct force calibration system allows for a weighing vessel or silo to be fully calibrated in the fraction of the time taken using traditional flowmeter or weighbridge calibration methods, thereby minimising production downtime and generating significant cost savings.
Their revolutionary, proven technique can be carried out easily on any weigh vessel with suitable jacking points fitted at each load cell location. There are two methods that can be used depending on the suitability and type of the vessel; reverse calibration and force calibration.
The reverse calibration method involves the HydraCal system being used to push a known amount of weight off a full or partially full system. Applied Weighing’s engineers jack the system in multiple, measured intervals back to zero, enabling them to check the overall system accuracy, the system linearity and repeatability. This method can often be carried out without the need to modify an existing system as most systems already have a suitable jacking point at each load cell. Reverse calibration is particularly good on bulk storage silos which are rarely emptied, because the calibration method can be carried out with product in the vessel.
Alternatively, with the correct brackets in place, the force calibration method requires the HydraCal system to apply a measured force down onto a weighing vessel, thereby allowing Applied Weighing’s engineers to calibrate the system in multiple intervals, often up to the full scale of the weighing system.
Both techniques are quick and simple once the calibration system is positioned, consequently limiting the downtime of the vessel and ensuring less production schedule problems. Calibration accuracy is to within 0.1%, signalling the technical superiority that Applied Weighing’s HydraCal system has over alternative calibration methods. The system is also fully traceable, with certification issued as standard, and ATEX approved for use in hazardous areas.
First established in 1990, Applied Weighing provides a complete range of weighing solutions and systems. These are custom built to meet individual customer requirements. Their range includes platform scales, silo and vessel weighing systems, drum filling systems, high speed weighing systems, telemetry systems and load cells. Applied Weighing products are used in a diverse variety of industry areas including pharmaceutical, food processing, milling and bakeries, aggregates and cement, fuel oils, chemicals and plastics. Their aim is to provide quality products on short delivery times, backed up with comprehensive technical support. Applied Weighing is an ISO 9001:2008 registered company and is certified for the manufacture of ATEX compliant products.
For more information on Applied Weighing’s HydraCal System Revolutionises Calibration talk to Applied Weighing International Ltd
Enquire Now
List your company on FindTheNeedle.