
Sign In
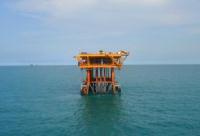
The recent level of increased optimism surrounding global economic growth has led to the International Energy Agency to improve its forecast for global oil demand for 2011. In order to satisfy this increase in demand, oil exploration and production companies are resorting to expanding their operations further out to sea in pursuit of the increasingly elusive supply of oil, despite the challenges associated with the process of offshore oil extraction compared to onshore alternatives.
When drilling in depths of more than around 120 metres, offshore drilling must be undertaken from a floating vessel, due to the fact that fixed structures are not practical for such operations. Therefore, depending on the depth of the water, the conditions on the seabed and other prevailing factors, offshore operations are performed using a range of mobile offshore drilling units such as jackups, semi-submersibles and drillships.
The process of drilling exploratory boreholes can be undertaken by these rigs, whereby drilling fluid is continuously circulated down a drilling pipe connected to the base of the rig and back to the surface in order to flush out rock cuttings. Invariably, cuttings are contaminated with oil from the drilling fluid and, given the importance that environmental protection has been afforded within the industry, the cuttings must be handled, processed and disposed of carefully.
A number of ships are dedicated to providing services for these mobile rigs and the responsibilities of such ships are varied, with some responsible for collecting cuttings and other by-products from exploration rigs. When an offshore services supplier recently required new weighing systems for eleven storage tanks onboard a service ship, they contacted Applied Weighing, the UK's leading manufacturer of weighing systems, for a solution.
The operating environment required for the system to be ATEX approved and robust enough to withstand transportation between the rigs and shore based processing plants. Consequently, Applied Weighing supplied their Safemount Loading Assemblies, with each module fitted with ATEX approved load cells. They also supplied ATEX approved weight indicators, which were mounted onto each module in order to allow visual weight monitoring. Critically, they also included outputs on each system which were used to signal the central control system and to stop the storage tanks from filling once the module had reached its target weight, thus preventing the risks that are associated with over-filling and the inefficiencies associated with under-filling such tanks.
Applied Weighing, which was first established in 1990, provides a complete range of weighing solutions and systems. These are custom built to meet individual customer requirements. Their range includes platform scales, silo and vessel weighing systems, drum filling systems, high speed weighing systems, telemetry systems and load cells. Applied Weighing products are used in a diverse variety of industry areas including pharmaceutical, food processing, milling and bakeries, aggregates and cement, fuel oils, chemicals and plastics. Their aim is to provide quality products on short delivery times, backed up with comprehensive technical support. Applied Weighing is an ISO 9001:2008 registered company and is certified for the manufacture of ATEX compliant products.
For more information on New weighing systems provide robust solution for harsh environment talk to Applied Weighing International Ltd
Enquire Now
List your company on FindTheNeedle.