
Sign In
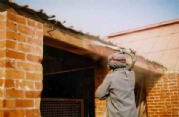
We specialise in using an adjustable pressure, low consumption sand jetting system that has been used nationwide for property restoration, including gaining approval for and subsequently working on many Listed Buildings.
The links on the left (and bottom of the page) should lead you to a page with further details. The Low Pressure Sand Jet system used by the Ashrose Group provides a number of advantages over rival sand, slurry, or water blasting systems. It also has advantages over acid cleaning ? the traditional technique for brick or stone cleaning.
Compared to traditional dry sand blasting machines consumption rates of sand are greatly reduced. Typical Dry Blast machines will use 250 kg of dry sand per hour. This quantity will generally last us the whole day ? with no drop in performance. Our machine was developed to allow the use of extremely expensive blast media (typically Garnet) for cleaning steelwork. Such are the quantities of sand use in dry systems that if it isnt recycled, sand would be a significant cost to the operator ? so dry systems tend to recycle the sand and can contaminate one site with the debris from the previous.
The large quantity of dry sand and pressures used in sand blasting mean that the operator has to be well protected, and dust is a widespread hazard. Operators tend to be further away from the workpiece, and with their protection requirements have less visibility of the work. We on the other hand can work close in and clearly see the area we are cleaning.
Traditional Slurry Blast systems wrap a dry blast in a water coating. This reduces the dust problem, but the blast system still uses the same quantity of sand. There being more sand also means that the slurry needs to be much wetter than in our system- leading to more water run-off. Slurry blasting also means that the sand cannot be recycled easily because dry blast pots rely on the flowing properties of dry sand.
High Pressure (200+ bar) will clean bricks ? but without extreme care will destroy the surface of the bricks? and Ultra-High Pressure (1500+ bar) water will eat through a wall very rapidly!
Chemical Cleaning is a traditional approach, typically using hydrofluoric acid. The acid, although weak is persistent, and causes operatives severe burns if not used carefully. It also needs careful application, dwell time of the acid being critical, and careful washing to ensure all is removed. The water run off from the cleaning operation obviously presents a hazard to the environment.
Our blast system mixes water and sand in the blast pot, and it is this slurry that is regulated and blasted. Any non-soluble blast media can be used, although it is possible to work with saturated solutions such as, for example, rock salt. Typically the abrasive we use for property tasks is crushed, recycled, glass bottles. This media is cost effective, and environmentally friendly. We also find that it has advantages in being sharper than other media, but rapidly looses its power ? allowing us to rapidly clean a surface with minimum risk to the surface itself.
The wetness appears at the nozzle as a damp mist type blast ? rather than streams of water. When blasting we rarely have enough run off of water to run down drains. Surface dirt and paint is captured by the damp sand against the wall and runs down the wall where it can be swept up and bagged ? effectively capturing hazardous paints such as lead based types. Once swept up the walls are then pressure washed to remove the final dirt/sand mix that adheres to the surface ? again these washings gather at the bottom of the wall where they are swept up and bagged.
The system, in our trained hands therefore causes minimal damage to an underlying surface and is flexible enough to tackle most property restoration cleaning tasks.
However, there are occasions where traditional dry sand blasting systems have their benefit
For more information on Sand Jetting System talk to Ashrose Group
Enquire Now
List your company on FindTheNeedle.