
Sign In
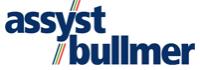
Composites UK
Official Trade Association for the Composites Industry
Lead partner: Cytec
Other partners: AEL, Assyst Bullmer and Gudel
The aim of this project is to develop and demonstrate a significant reduction in the cost of selected composite element(s) in a tidal turbine blade through (a) Optimised component design (probably a single-piece spar) (b) Evaluation of current manufacturing processes and (c) Development of bespoke ‘automated’ solutions for the manipulation of large, unwieldy prepreg plies. At the end of the project we expect to demonstrate and show advances on the state-of-art through the cutting, picking, placing and forming of prepreg materials.
As on date, we have achieved the following:
- Reduce waste and consequently the production costs by optimization of the nest.
- A comparison study of 600 vs 1200 mm wide UD that shows 1200 mm wide UD to be cost effective as compared to 600 mm.
- Optimum method of ply stacking/drawer optimisation for storing cut plies.
The next step to take this work further is to develop specifications of equipment needed to automate the process of cutting, picking and placing in storage and storage solution.
ATTOM
ATTOM will develop affordable tidal turbines via optimised manufacture. It is vital for all renewable energy projects that efforts are made to reduce costs, as renewable energy is still significantly more expensive than conventional non-green sources. In the area of composite blades for tidal turbines, many recent advances have been made in material formats, reducing cost by developing cheaper and better performing materials.
2014 will see the start of series-production of tidal turbine installations with rapid growth forecasted. In order to ensure that the supply chain is ready for this growth, the ATTOM project proposes investigate the potential for automation or improved materials handling methods as a further route to cost reduction, alongside factors that may affect production line layout and the possible solutions to specific quality control problems.
ATTOM will contribute to developing a UK-based supply chain that can produce tidal turbine blades at 20% reduction in cost through the use of automated/mechanised lamination techniques and improved design. It will demonstrate this by designing and manufacturing selected mouldings for automated/mechanised production methods, thus proving the potential for job creation by creating 70 jobs within the life of the project.
For more information on Affordable Tidal Turbines via Optimised Manufacture (ATTOM) talk to Assyst Bullmer Ltd
Enquire Now
More News
List your company on FindTheNeedle.