
Sign In
What Is Functional Test?
29-04-2021
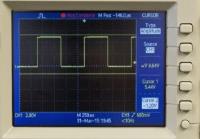
Deciding on a test strategy for your electronic product needs some careful thought. All testing comes at a cost, at very least in production time, so consideration has to be given to how error prone your manufacturing process might be and how much you need to ensure the finished product really works.
Amongst the test options is ‘functional test’, sometimes referred to as ‘FCT’. This is still perhaps the most common test method as it can be used on everything from relatively simple and inexpensive products through to valuable, high reliability assemblies where guaranteed performance is critical. Functional test is applied on both low and high production volume items where test access for say in-circuit test (ICT) isn’t possible. It can be used on its own, or often alongside other test and inspection methods such as automated optical inspection (AOI), ‘flying probe’ test, boundary scan or ICT. So, it’s versatile.
Functional Test
The idea of functional test is to make the unit under test (UUT) operate just as it would in real life. That means creating or simulating real power supply conditions and running the product at actual clock and communication interface speeds.
To assist with any fault finding, the test should break the functions down into separate blocks, for example power supplies, displays, inputs/outputs and communications, rather than testing the whole thing and reporting pass or fail at the end. Tests should only proceed to the next stage if it is safe to do so.
As with any manufacturing test, it should be looking for manufacturing defects, especially those that component level testing such as ICT or flying probe might not find, like the colour of LEDs.
A common mistake is to make the functional test try to verify the product design. Whilst the design of the functional test might well originate from the product developer’s design testing, there should be little or no value in repeatedly checking this on every production unit. An exception might be where ‘select on test’ is necessary, when a component may have to be adjusted, fitted or replaced depending on the test results of that individual assembly.
Test Coverage
What the functional test needs to test and what is left out depends on what other testing is performed and how much confidence is required in the performance of the product. If, for example, ICT is performed and it covers continuity (opens and shorts) between connectors, then it might not be necessary to repeat this within the functional test. However, if the requirement is to test continuity through the actual connectors, and not just the printed circuit board (PCB) connections, then the test would be better performed at functional test rather than ICT.
Test specifications
The secret behind generating a good functional test solution is the Test Specification. Ideally this should be generated by the product design engineer, as they will have the best knowledge of how the product has been designed to work. Additional input from a test equipment or production engineer helps identify the manufacturing defect risks to look out for. Note that if the product includes programmed devices then input from the design engineer is essential, as it won’t be possible for someone else to determine functionality from circuit diagrams alone.
A good test specification will cover all the following:
• An overview of the functionality of the product to be tested
• Definition of all inputs and outputs
• Specification of test inputs required
• Definition of the test outputs expected, including limits and tolerances
• A description of all tests required to meet the test coverage requirements
• An estimate of the test coverage to be achieved
• Any diagnostic messages to be included in the test sequence
• How the test is sequenced, and what to do if a test fails
• Safety considerations
Test Systems
A functional test system can either be a dedicated piece of hardware – and perhaps software – for a particular product, or a standardised hardware and software test platform that can be used for multiple products, such as ATE Solution’s FLEX systems. For the latter, an appropriate interchangeable interface is required for each UUT. This often takes the form of a fixture, with pins that probe onto the PCB or cables to the UUT connectors. The choice of approach depends on the complexity of the tests required, budget, and production volumes.
For more information on What Is Functional Test? talk to ATE Solutions
Enquire Now
List your company on FindTheNeedle.