
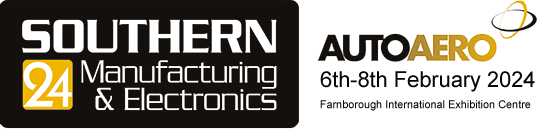
In the ever-evolving landscape of wire harnessing production, the quest for efficiency and precision stands at the forefront of industry priorities. A pivotal stride in this direction comes in the form of automatic crimp machines, which offer a multifaceted advantage, ranging from heightened productivity to elevated quality assurance. These machines have become an indispensable asset across various industries, transforming the way manufacturers approach wire harnessing.
Automatic crimp machines play a pivotal role in significantly boosting productivity levels, distinguishing them from their manual counterparts that rely on human effort. Operating seamlessly, these machines have the capability to process numerous connections in a fraction of the time it takes for manual hand crimp tools. This accelerated pace not only allows manufacturers to meet stringent deadlines but also elevates overall production output.
Precision is a cornerstone in any manufacturing process, and automatic crimp machines deliver it with unwavering accuracy. The automated nature of crimping eliminates the variability introduced by human factors, ensuring that each crimped connection adheres to exact specifications. This consistency not only minimizes the risk of defects but also enhances the overall quality of the end product.
Beyond precision, automatic crimp machines contribute significantly to improved safety standards. Manual crimping tools often demand substantial force, increasing the likelihood of repetitive strain injuries among workers. In stark contrast, automatic crimp machines operate with minimal human involvement, reducing the risk of workplace injuries and fostering a safer working environment. This not only safeguards the well-being of the workforce but also translates into lower healthcare costs and fewer disruptions in production.
Cost-effectiveness emerges as another compelling benefit of automatic crimp machines. Despite the initial investment appearing high, the long-term savings are substantial. These automated machines operate efficiently and reliably over extended periods, requiring minimal maintenance. This longevity, coupled with the reduction in labor costs and the avoidance of rework caused by human error, results in a significant return on investment over time.
Moreover, the adaptability of automatic crimping machines to various applications and connector types makes them a versatile choice for companies. These machines can be programmed to accommodate different crimping specifications, allowing for seamless integration into diverse production processes. This flexibility not only streamlines operations but also future-proofs manufacturing facilities against evolving industry standards and product requirements.
In conclusion, the advantages of automatic crimping machines are clear and compelling. From increased productivity and enhanced precision to improved safety standards and substantial cost savings, these machines are reshaping the wire harnessing production landscape. As manufacturers continue to seek innovative solutions to stay ahead in the competitive landscape, embracing automatic crimp machines is undoubtedly a step in the right direction. The future of wire harness production is here, driven by the relentless pursuit of efficiency and precision through automation.
For more information on The Revolution of Efficiency and Precision: Embracing Automatic Crimp Machines in Wire Harness Production talk to Automated Cable Solutions Ltd