
The importance of treating compressed air
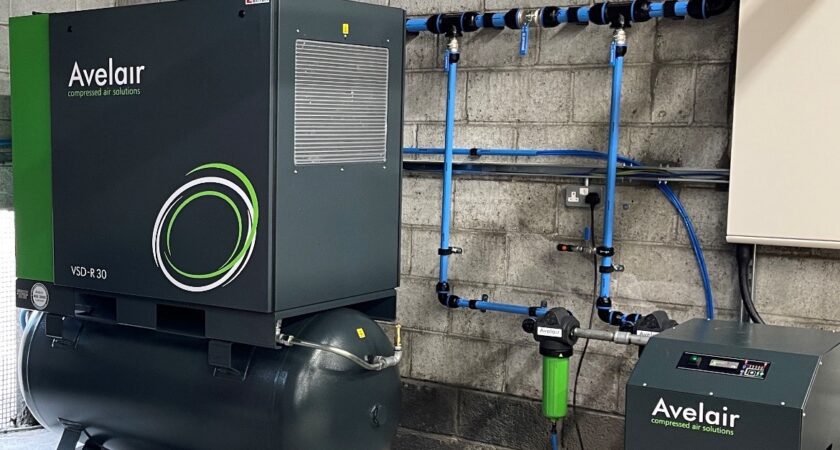
Compressed air, often referred to as the “fourth utility,” plays a vital role in various industries. However, it faces constant challenges from different contaminants which enter the compressed air from the ambient air, the compressor, the receiver and the pipework, The main types of contaminants in compressed air are as follows:
- Water Content in Compressed Air:
- Moisture enters the compressed air system through the intake as water vapor. It is the most prominent contaminant in terms of volume.
- The water content is measured by its dewpoint, which indicates the temperature at which the compressed air can still handle its water vapor before condensation occurs.
- If moisture is not removed, it can lead to corrosion, bacterial growth, and adverse effects on product quality and machinery.
- In applications like food and beverage or pharmaceuticals, air quality is critical to prevent bacterial contamination. The British Compressed Air Society has launched a number of best practice guidelines for vertain applications – contact our team to discuss this in more detail.
- Oil in Compressed Air:
- The quantity of oil in compressed air depends on factors such as the air compressor type, design, age, and condition.
- Oil can enter the system as vapor or liquid. It poses risks to downstream equipment or application such as breathing air which can then become a health and safety issue.
- Proper filtration and separation are essential to maintain oil-free air.
- Dust Particles in Compressed Air:
- Ambient air contains tiny particles that become visible under certain conditions (fog, smog, or smoke).
- These particles can damage pneumatic equipment, clog filters, and impact product quality.
- Effective filtration ensures clean air for reliable operations.
- Microorganisms in Compressed Air:
- Bacteria, fungi, and other microorganisms can thrive in moist environments.
- Contaminated air can compromise product safety, especially in sensitive industries like food and pharmaceuticals.
- Regular maintenance and proper treatment are essential to prevent microbial growth.
Treating the compressed air can be via air filtration and different types of dryer technology. Treating compressed air has many benefits as listed below:
- Equipment Longevity: Proper treatment ensures downstream equipment—such as pneumatic tools, valves, and actuators—lasts longer. Contaminant-free air prevents corrosion and wear.
- Product Quality: Clean air prevents contamination during manufacturing processes. Whether it’s food, pharmaceuticals, or electronics, product quality relies on pristine air.
- Energy Efficiency: Dry air reduces friction and energy losses in pneumatic systems, improving overall efficiency.
- Safety and Compliance: Treating air ensures safe working conditions and adherence to air quality standards. This could be where compressed air is used for breathing air, food and beverage direct or indirect contact requirements, or pharmaceutical requirements.
Remember, the quality of compressed air directly impacts your processes and products. Contact our team on 01359 272828 to see how we can help you ensure you have the correct air treatment equipment in place for your applications and processes.
For more information on The importance of treating compressed air talk to Avelair Compressed Air Solutions