
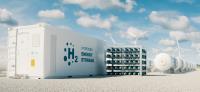
In renewable energy storage and carrier technologies the function of the battery is to store electricity in the form of chemical energy and to convert to electrical energy when required. Vented lead-acid batteries or flooded batteries as they are also commonly known, consist of plates that are flooded with an acid electrolyte. When charging, the electrolyte emits hydrogen through the vents in the battery. Under normal operations, the release of hydrogen is relatively small, but this is elevated during heavy recharge periods. Hydrogen is a key factor in ensuring a reliable, safe, and stable energy source in the post fossil fuel period. Therefore, the safety of hydrogen ventilation and a correct hazardous area classification should always be undertaken when handling applications that have this explosive group IIC gas. Hazardous area classifications (HAC’s) are used to identify places where, because of the potential for explosive atmospheres, special precautions over sources of ignition are needed to prevent explosions. Hazardous area classifications should only be done by responsible and certified personal; equipment manufacturers should not decide the classification and the onus should be on the end user to determine the correct zone and class of the area to determine where an explosive atmosphere is present, if it may occasionally occur or if it will only exist in abnormal conditions. Hydrogen is a group IIC gas and belongs to the T1 temperature class making it one of the hottest, most dangerous gases. When mixed with oxygen, Hydrogen is a highly explosive substance that is odourless, colourless and lighter than air. The lightweight element accumulates above the oxygen, and where effective ventilation is not in place, a build-up can occur. In extreme circumstances there have been cases of battery room explosions as a result of ineffective battery room ventilation. A small smoulder can create a huge explosion when hydrogen is in the presence of oxygen, and besides this, hydrogen is hazardous to health, causing skin burns and eye issues. Dismissing a critical safety issue is clearly not responsible, system integrators in commercial, industrial, renewable energy and dockyard applications need to identify the risks and design a system to protect in a fail-safe way. This also includes protecting personnel with protective workwear. Any structure containing hydrogen components should be adequately ventilated. Suspended ceilings, inverted pockets, confining cowlings or covers that might accumulate hydrogen should be avoided if possible. The release of hydrogen in laboratory settings should be controlled by enclosures, fume hoods or vented outside to prevent it from reaching an ignition source. The likelihood of an explosion occurring in the case of a battery room depends on the number of batteries, the charge rate, the size of the room and the ventilation available. Legislation advises the number of air changes per hour, for example IS:1332 Battery Rooms advises 12 air changes per hour or suggest that hydrogen concentration levels are kept below 1% to avoid the risk of explosion. The National Fire Protection Association lists the explosive concentration level, or Lower Explosive Level (LEL) of hydrogen as 4%, so the legislation stipulating a maximum level below 1% encourages the safe implementation of ventilation systems to avoid explosions far below the stipulated 4% explosive level. Air changes per hour tables can be used to determine the changeover rate depending on how the room is used. If the level of hydrogen in a battery room exceeds 1% after one hour of charging, mechanical ventilation using ATEX explosion proof exhaust fans is required. This should be a compulsory requirement even if the concentration is not expected to reach 1%, due to uncertainties in building geographies, high points, or inadequate and blocked openings for natural ventilation. Ventilation should ideally be placed at both high points (for the exhaust of hydrogen that accumulates above the oxygen), and low points within the room to encourage forced ventilation out of the room. There should be no air recirculation under any circumstances as this encourages the mix of the two gases, and where possible, on a separate ventilation system than the rest of the building. Corrosion resistant fans with ATEX non sparking components, ideally roof mounted to exhaust upward and out are the ideal solution, but if not possible, ATEX wall mounted axial fans with back draught dampers, to avoid the return of hazardous substances, can be used. All Axair ATEX explosion proof fans are suitable for IIC gas groups to ensure adequate and safe removal of Hydrogen gas. Both temperature class and gas group are important pieces of information that are required for the correct selection of ATEX industrial fans for Hydrogen exhaust. There’s a difference between IIB + Hydrogen and IIC markings. Our Casals ATEX fans are all IIC gas group certified. Our Rosenberg product series EHND, DKNM and DKNB are available with material combinations suitable for hydrogen (H2). According to ATEX and EN 60079-0 the fans are marked with II 2G Ex h IIB+H2 T3 Gb X (with Ex eb motor) or II 2G Ex h IIB+H2 T4 Gb X (with Ex db, Ex eb motor). Rosenberg fans for potentially explosive atmospheres are manufactured and tested according to legal regulations in the EU, Internationally and in the UK. The possible contact surfaces between rotating and stationary components with regard to operating faults, which are usually to be expected, are manufactured from materials where the danger of ignition is limited by friction, grinding or impact sparks. Those quoted Rosenberg ATEX Fans will have conformance documents and supporting certification supplied along with the order and can review all documentation at quote stage to confirm it is compliant. Rosenberg Ex fans are suitable for conveying explosive atmospheres of zones 1 and 2 and for installation in zones 1 and 2 for combustible gases.
For more information on IIC Hydrogen Exhaust & Effective Battery Room Ventilation talk to Axair Fans UK Ltd