
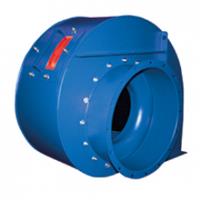
When selecting a fan for a corrosive environment it is important to have some knowledge of how corrosive atmospheres are categorised, this ensures that a selected fan is deemed suitable for use in harsh environments that are at risk of steelwork corrosion, coating failures, and a reduction in the life span of the components ability to perform to its required function.
ISO 12944 in particular part 5, known as ISO 12944-5:2018(En) Paints and varnishes — Corrosion protection of steel structures by protective paint systems — Part 5: Protective paint system, is a globally recognised standard for corrosive environments and details the categories, durability options and paint protection coating requirements for steel structures in atmospheric, immersed, and buried environments. ISO standard 12944-21 classifies corrosivity severity according to the mass loss of unpainted steel or zinc exposed one year on the site as seen below.
C1 - Very Low: Interior Applications - Heated buildings with a clean atmosphere such as offices, schools, hotels, shops
C2 – Low: Interior Applications – Areas with low levels of pollution, mainly rural Exterior Applications – Unheated buildings where condensation could occur such as sports halls, store houses, depots
C3 – Medium: Interior Applications: Areas with high humidity and some air pollution such as production rooms, food processing plants, dairies, breweries, or laundries Exterior Applications – Urban and industrial atmospheres, moderate sulfur dioxide pollution, or coastal areas with low salinity.
C4 – High Interior Applications – Swimming Pools, chemical plants, coastal ship and boat yards Exterior Applications – Industrial areas and coastal areas with moderate salinity.
C5 – Very High (Industrial) Interior Applications – Buildings/areas with high contamination and constant condensation Exterior Applications –Aggressive atmospheres with high humidity
CX – Extreme Interior Applications – Buildings/areas with constant high contamination and almost constant condensation Exterior Applications – Inshore and Offshore areas of high salinity In line with the demand for corrosive resistant fans in harsh environments, special requests are regularly made for enhanced paint protection on our range of industrial fans.
As standard Axair supply fans manufactured from rolled sheet steel or Fe360 steel finished in a RAL 5010, qualicoat polyester powder coating stoved at 200 degrees. Stainless steel or marine grade finishes C3, C4, C5 and CX increase the corrosion resistance of these fans making them suitable for use in harsh environments.
Some products, such as the Prextur, are C3 as standard given the nature of their regular application use. The Prextur medium pressure centrifugal fans with direct coupling and reinforced steel housing are ATEX certified and protected against corrosion with powder coating polyester resin and a C3 finish. They have a high efficiency rate up to 84% and are suitable for a wide range of applications including dusty environments. The Prextur has several beneficial features including a self-cleaning turbine and reinforced impeller with high performance backward blades made of carbon laminated steel dynamically balanced to minimise noise and vibrations. Typical applications include paint booths, dust collection, food industry dryers, food processing, pollution control and the manufacture and treatment of chemical products.
What Materials are 304 and 316? 316 grade steel is commonly known as marine grade stainless steel due to its ability to resist chloride corrosion. It contains 2-3% molybdenum, a hard metallic element which strengthens the steel and enhances its corrosion resistance. This makes it a suitable option for marine applications and provides an extended lifespan. 304 grade steel contains 18% chromium and 8% nickel, it is a cheaper alternative to 316 steel but is lacking molybdenum making it less suitable for highly corrosive environments. The lack of molybdenum would result in chloride corrosion in saline atmospheres making it a less viable option for the marine industry. Any form of corrosion will shorten the lifespan of a fan.
Axair's stainless-steel fans are available in both 304 and 316 as normal or electropolished versions. Special steel is also available on request including Cor-Ten A and Hardox for aggressive atmospheres with high humidity in addition to anticaloric paint coating. Cor-Ten steel is known as weathering steel meaning it can withstand all weathers or atmospheric corrosion due to its natural chemical composition of cor-ten alloys which protect the steel from corrosion by developing a protective top layer via surface oxidation. Hardox is a very hard wearing, abrasion-resistant steel with good bendability and weldability providing excellent structural properties. Anticaloric paint coating adds additional resistance to extremely high temperatures.
Most industrial fans in Axair's range can be manufactured from stainless steel. Some fans are available on request as hot dipped galvanised. In the process of galvanising, steel is dipped into molten zinc forming an alloy coating as the iron in the steel reacts with the zinc. This top coating acts as an extra layer of protection against corrosion and ensures a long-life span.
For more information on Understanding Corrosion Resistant C3, C4, C5 and CX Paint Grades talk to Axair Fans UK Ltd