
Sign In
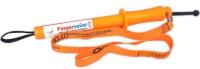
Testimonial: “BEC worked with us to resolve a number of issues and provided an exceptional end-to-end plastic injection moulding service, from under one roof. Being local meant we could visit them regularly, giving us visibility at every stage of the project, making problem-solving quick and easy.”
Martin Dennis, Specialised Engineering Products (SEP)
Project: The Fingersaver
A critical safety tool (preventing finger injury) used by a major global supplier in their refineries and oil rigs. Labelled 100% safe.
Industry:
Oil, Gas & Mining Industry
Services:
From concept to completion. End-to-end plastic injection tooling and moulding service. We designed and made the injection mould tool, and injection moulded the specialist Fingersaver handle and washer component.
Collaborating with 2 other manufacturers; one compression moulding company and one extrusion moulded, between us moulding different components, combining 3 moulding processes to produce one highly successful product.
Our Client:
Specialised Engineering Products – globally renowned and respected precision engineers. Supplying multiple industries; from Aerospace, Nuclear, Defence, Oil & Gas to Pharmaceutical, Marine & Petrochemical. This product is for the Oil & Gas Industry; a compulsory, critical piece of health and safety kit, preventing hand and finger injuries on offshore oil rigs.
Our Mission:
To take on the outsourcing and enable mass production of SEP’s Fingersaver – a product they’d originally developed and produced in-house.
To enable the client to keep up with a rapid escalation in product demand.
To be a collaborative supplier who could dig deep; test materials, analyse results and trial products in order to find the right solution.
Tenacious in spirit, the BEC team were up for the challenge!
BEC Solution
As is often the case with new product development we had to make a few adjustments to resolve issues during production.
SEP and BEC worked together to carry out capability studies, proving without doubt that a material change and some modifications to the tool would give a more consistent product within tighter tolerances.
Following a series of material trials after testing; Acetal gave the best results. Both moulding trials and the entire manufacturing process undergoing rigorous inspection every step of the way.
Collaborative Problem Solving
Thanks to both SEP and BEC teams working together so successfully, we were able to resolve a number of issues and share learning on both shopfloors during the project. Adjusting the tool, adapting the moulding, de-risking and speeding up the assembly process.
As a local manufacturer, offering an end-to-end plastic injection tooling and moulding service in-house, we were able to work as an extension of SEP’s own R&D team, so Martin could visit us at regular intervals to sign off each critical stage.
We also provided a spark eroding service – invaluable since they’re hard to find these days – especially one that’s integral to a fully functioning toolroom. Everything SEP needed in one place!
Result
By making the injection mould tooling; 2 x mould tools – 1 for the washer (4 cavities) and 1 for the handle (2 cavity tool) and plastic injection moulding the Fingersaver components, we were able to meet SEP’s requirements.
As for new product introduction? We helped SEP develop a brand-new, highly successful product, mass produced to meet increased demand.
Fingersaver: this innovative safety aid is now standard issue with major suppliers on their refineries & oil rig safety practice, worldwide. Protecting maintenance operatives from all-too-common injuries to fingers and hands.
A true example of #plasticsforgood
If you’re looking for an established UK manufacturer to help with you next specialist plastic injection moulding project please get in touch on 01425 613131 or email.
For more information on 100% SAFE CALLS FOR 100% COMMITMENT talk to BEC Group
Enquire Now
More related to 100% SAFE CALLS FOR 100% COMMITMENT
List your company on FindTheNeedle.