
Sign In
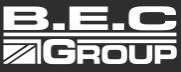
“I approached BEC Group after being warned off Chinese mould tool companies and was so glad I did. I initially dealt with Paul Holland who I met with on a number of occasions to discuss my component design and CAD drawings. The software Paul used to analyse the unusual shape of the initial component threw up a few problems due to its thickness, but he was able to make the changes to the CAD files that I needed and we were good to go. Paul suggested a 2 cavity mould tool that could make two components at a time which would drastically reduce cost. The mould tool got underway and with various adjustments following direct conversations with Mike Tharme, the tool maker, further cavities were squeezed into the tool to allow for a second bespoke component that could be branded, saving me having to source this separately and ‘make it fit’ my product. I was able to pop down when the tool was finished and be present for the first run-off of components to ensure they had the correct shot-blasted finish I had hoped for. The whole process was fantastic from start to finish and I can’t thank the BEC Team enough for allowing me to be so involved for the entire project. I have complete faith in their ability for future orders or mould tools.”
Client: Rob, Company Director
Project: Climbing Device Components
Services: Complete end-to-end manufacturing of component parts: Collaboration on design pros and cons for manufacture, mould tool design & manufacture, material selection, plastic injection moulding, insert moulding, laser engraving, overmoulding, critical material trials to verify materials and ensure fit for purpose.
Our Client: is a UK-based climbing brand, innovating and supplying unique products for climbers globally.
Our Mission: Company founder, Rob, came to us having developed the concept for an innovative climbing device. With the initial design and 3D CAD model for a specific component part already in hand, he asked BEC to help him make the product a reality. Various runs of 3D printed test pieces had already been put through their paces and the challenge was then to find the right plastic that could stand up to demand, and to digitally analyse the unusual shape of the component to ensure it could be successfully moulded.
BEC Solution:
As with every new product innovation, we carried out a thorough Design for Manufacture (DFM) review, so we could analyse and understand each component part. The team recommended a few design changes so we could manufacture economically, without compromising on optimum safety levels or the innovative nature of the product. Ultimately reducing the overall production cost.
Initially the enquiry was for a single component, but we opted for a 2 cavity tool as this was the most economic option. After discussion we were able to add additional cavities of another component to the tool. This removed the need to buy in from another source. As well as reducing the cost, the new component was designed to include the company branding.
Once signed off, we designed and made the mould tool, advising on the most appropriate moulding material, overmoulding the brass inserts and stainless-steel bolts, as well as laser engraving the logo, keen to ensure the end product could withstand the harsh conditions and physical stresses demanded of it.
The material selection process resulted in three options, so we produced prototype mouldings in each one, allowing for final product testing.
Result:
The world’s first multi-use climbing tool facilitating interchangeable applications, making this climbing device the go-to component for safer climbing adventures.
We love innovation, so this was a really exciting project! By involving us at an early stage, the client had a team who completely understood the vision and could work closely every step of the way.
The combination of Rob’s climbing knowledge and appreciation of the technical functionality required of the product, and BEC’s knowledge and expertise in tool design and moulding has meant this highly adaptable product is the best it can be. Because Rob was local, he was able to pop in at every key stage, even on site to approve the first injection moulded samples hot off the production line and make final tweaks for a perfect result.
Contact us to find out how we can help with the manufacture of your next device components.
For more information on Climbing Device Components talk to BEC Group
Enquire Now
More related to Climbing Device Components
List your company on FindTheNeedle.