
Sign In
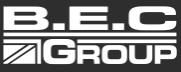
“The extent of BEC’s knowledge and expertise of plastic injection tooling and moulding was obvious from the outset. They restored my confidence in UK manufacturing, and I knew that if these guys couldn’t make the Hatpac then no-one could. Based in Hampshire it was so easy for me to visit the team and be onsite to sign off at each critical phase of the design, tooling and moulding process. As an inventor they helped me navigate the manufacturing process and the steps to making a plastic injection moulded product. They were always willing to answer any questions, talk through my concerns and any challenges were faced head on, with solutions always found.”
Jack Hamilton, CEO and founder of Pacfinity
Project: Hatpac by Pacfinity
Services: End to end design, product engineering, tooling and moulding. Injection mould tool design and manufacture, tooling modifications, plastic injection moulding, 2nd ops and product assembly.
Our Client: Pacfinity, based in the UK, is the creator of the PAC™ brand. Launched in 2019, with an innovative storage solution for baseball caps. The Hatpac was designed to accommodate three caps, made from environmentally friendly, recyclable materials, enabling consumers to both display and protect their baseball caps.
Our Mission: Pacfinity’s founder, Jack, identified and visited a number of plastic injection moulding companies but didn’t get the help and support he was looking for. Our mission was to reassure him that UK manufacturing with BEC was a viable option. With a sound concept our role was to review the design from a manufacturing perspective and recommend developments at every step of the manufacturing process to bring his concept to life, within timescale and on budget.
Our Solution: Full client involvement every step of the way. We worked closely with Jack throughout a complex product development and manufacturing process to keep him informed at every critical stage. Being an inventor and new to manufacturing, the BEC team were keen to translate technical manufacturing terms into plain English so he could make informed decisions.
With in-house design, tooling and moulding capabilities under one roof, it was easy for Jack to be involved from start to finish. Meeting those involved in the project, so he could tap into their technical expertise every step of the way, providing:
Mould tool design and manufacture
Product using recyclable materials
Single Hatpac deodorizer included with each case to keep caps fresh
Opportunity for customisation in the future, offering increased sales opportunities
Secondary operations (2nd Ops) and finished product assembly advice
We recommended the most cost effective and quality tool design to achieve his desired result within the allocated budget, referring to a thorough design for manufacture report which supported our recommendations for the best way forward.
Once we’d manufactured the mould tools, they were inserted in the moulding machines for rigorous product testing with tooling modifications mapped and documented.
Once the prototype was approved, the BEC on-site moulding team ran the tool and the first mouldings were produced, in addition assembling, boxing and packing the parts ready for shipment to his distributor – Amazon – to give Pacfinity time to find premises for storing the fully assembled Hatpac baseball cap units.
Result: Successful Hatpac product launch, making it available in time for Christmas 2019.
If you’re looking for the convenience of UK manufacturing design, plastic injection mould tooling, moulding and product assembly, all under one roof, please get in touch. Call us on 01425 613131 or email us, either way, we hope to hear from you.
For more information on Hatpac Baseball Cap Case talk to BEC Group
Enquire Now
More related to Hatpac Baseball Cap Case
List your company on FindTheNeedle.