
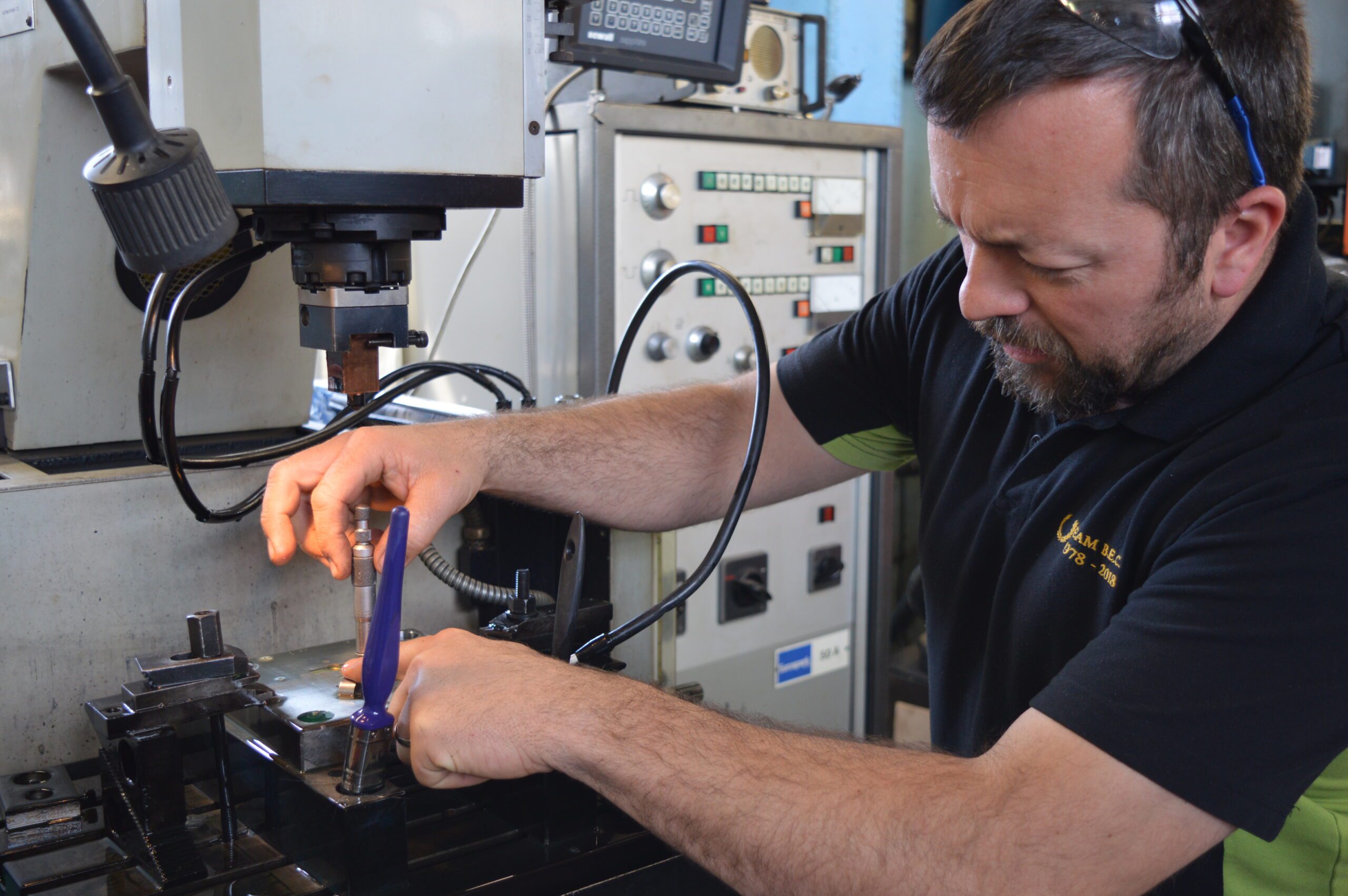
Taking a design into production is a risky business. Without proper testing, you won’t know if parts fit together as intended, if materials behave as expected, or if your design functions perfectly.
The fact is, late-stage surprises can easily escalate into costly delays and budget problems.
Luckily, rapid tooling – creating prototype tools and testing out designs iteratively – changes this dynamic. It allows you to test and refine designs early, using real materials in real manufacturing conditions.
Read on to discover how rapid tooling, done right, can support your next manufacturing project.
Framing the Problem
Full production tools represent a massive commitment. Each tool can cost up to tens of thousands of pounds and tie up months of development time.
Many manufacturers only discover design issues after this investment – when changes prove most expensive. A flaw in material flow or part fit can mean expensive modifications or redesigns.
Most companies can’t afford these setbacks. Modern manufacturing demands faster launches and tighter margins.
Through rapid tooling and prototyping, manufacturers can test designs thoroughly using production-grade materials and real manufacturing conditions. Early design validation catches issues when they’re still cheap to fix.
The Insights Gained From Real Results
Rapid tooling creates parts using your final choice of plastic under genuine manufacturing conditions, allowing manufacturers to validate designs thoroughly before committing to full production tooling.
By running the actual manufacturing process with your prototypes, you’ll identify issues that even the most detailed design reviews might miss.
In short, rapid prototyping puts you in a stronger position to:
Understand how materials flow through complex parts
Identify areas needing additional strength
Check how components fit and work together
Spot potential production issues before they become costly
Armed with such practical knowledge, manufacturers can refine designs before investing in final tooling, avoiding expensive modifications later.
The BEC Group Advantage
Quality rapid mould tooling demands both expertise and the right materials. At BEC Group, our experienced team handles every aspect of tooling in-house at our Hampshire workshop.
This means faster turnarounds, better quality control, and direct access to our toolmakers whenever you need them.
We never compromise on materials or methods. Using P20 steel for all our tools – including rapid tooling – means your test parts will match the final production quality perfectly.
By combining deep manufacturing knowledge with premium materials, we help you move from concept to production with greater confidence and fewer surprises.
Contact our friendly team to discuss your requirements.
For more information on Reducing Production Risks with Rapid Tooling in Early-Stage Manufacturing talk to BEC Group