
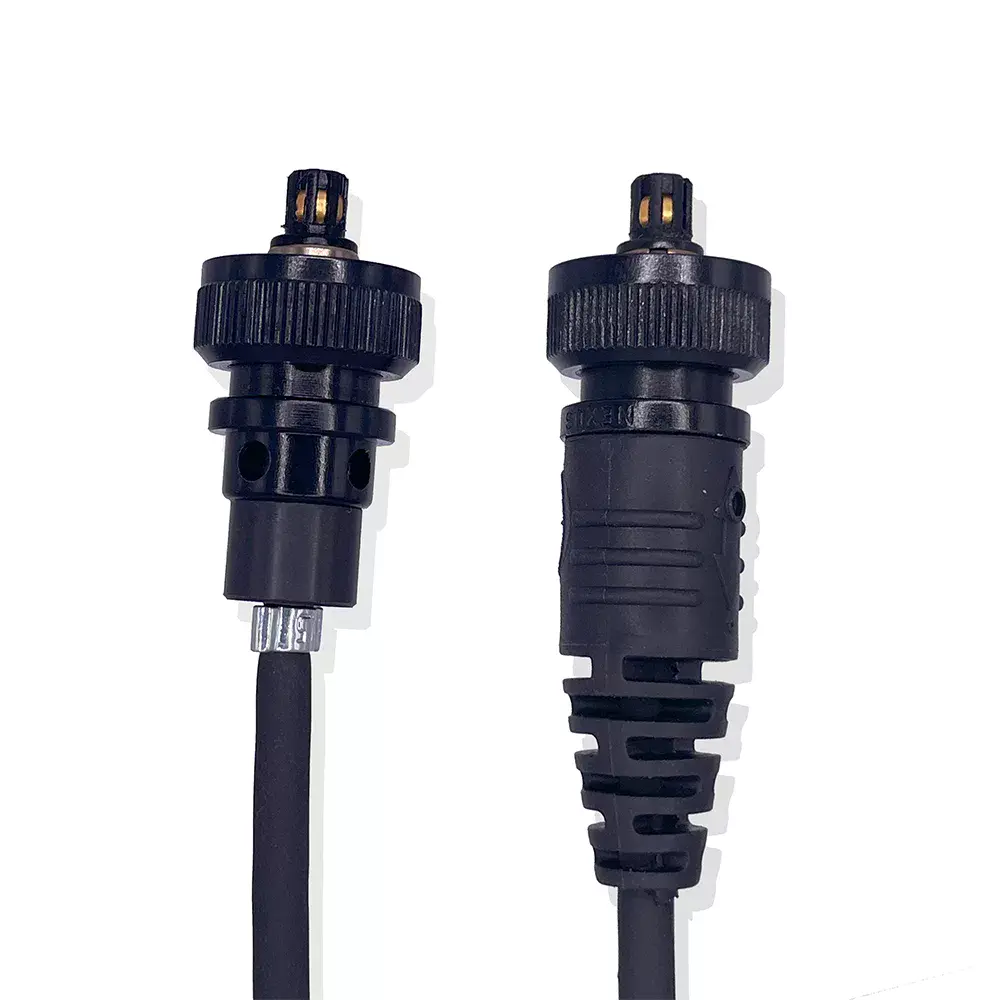
Overmoulding is a plastic injection moulding technique that moulds two components together to make a single part. Overmoulding electronics involves moulding plastic over an electronic substrate, creating a part which is often more durable, flexible, and protected from outside elements.
Lots of the electronics used in everyday life are overmoulded, including cables and wires, sensors, and printed circuit boards.
Why overmould electronics?
There are a few reasons why electronics are overmoulded:
-Waterproofing: Many electronics will be completely ruined if exposed to water, particularly salt water. Overmoulding prevents water from getting inside the part.
-Durability: Electronic parts may be overmoulded to help them withstand harsh environments, giving them greater resistance to impact, dust, chemicals, and heat.
-Appearance: Overmoulding can improve the aesthetics of an electronic part. Bespoke elements such as logos and writing can be added to provide branding or decoration during the moulding process.
-Reduces secondary operations: Overmoulding can negate the need for costly and time-consuming secondary assembly operations.
-Increased product lifespan: Improved durability of the part will increase its lifespan and return on investment.
Limitations of overmoulding electronics
There are some points to consider when weighing up overmoulding for your project:
-The process is more complex and time consuming than traditional injection moulding. This also increases the costs associated with it. It can still be more cost-effective than other methods however.
-Not all elastomers and plastics adhere to one another- your moulder will need to take this into account when designing your part and its materials.
-The electronic substrate will need to be held in position while the plastic flows around it in the mould tool, this can be tricky to achieve.
How do we overmould electronics?
Prototyping: In some cases, 3D printing can be used to quickly produce a prototype overmould as a means of checking if the design fits application requirements before commencing hard tooling.
Design: The mould tool is designed to securely hold the substrate in place whilst molten plastic is injected around it. The toolmaker will also need to consider more typical mould tool issues such as gates, runners and wall thickness when designing the tool.
Material selection: The ideal materials will be selected for both the electronic component (substrate) and the overmould. Often the substrate is made from a metal, and the overmould is made from TPEs or TPUs (more on that later).
Moulding: Once the mould tool has been set up the molten plastic is injected into the cavity under pressure, it fills the mould around the substrate and cools. Once cooled and solidified the mould tool opens and the part is ejected.
What materials are used in electronics overmoulding?
Material selection for electronics overmoulding is dependent upon a number of factors. This includes application, environment, cost and part specifics (such as wall thickness).
Commonly used materials for overmoulding include:
- TPEs – they provide protection from heat, water and UV and are relatively soft and slow flowing- reducing the amount of stress put on the electronics during moulding.
- TPUs – Improve flexibility, chemical and impact resistance.
- Silicone – Provides flexibility, temperature resistance and is biocompatible.
If you’d like to know more about overmoulding electronics, or would like to get in touch regarding an overmoulding project, then email hello@becgroup.com or call us on 01425 613 131.
For more information on Overmoulding Electronics talk to BEC Group