
Sign In
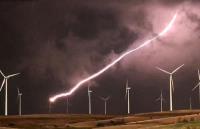
Our recent blog revealed that, as more wind farms move offshore, manufacturers are having to innovate to ensure that expensive and dangerous maintenance work is kept to a minimum.
With the average lightning strike containing 55 kWh of energy, and a powerful strike capable of 20 times this value, major storms pose a significant risk to consistent energy production, not to mention the cost of repairs. In order to optimise the ROI of a wind farm, turbines must operate effectively as a unit, so if one part of the system is running at reduced capacity or facing downtime for repairs, the whole production is at risk.
As a result of their remote location, often in areas of high elevation, as well as their height, turbines are at a significant risk of direct lightning strikes. Fortunately, there are a number of methods wind farm owners can adopt to minimise the risk of damage.
Most turbines are now manufactured with in-built protection that uses grounding systems in the blades, as well as the turbine itself. Products such as BGB’s 120 amp lightning brush holders are robust units designed to dissipate lightning energy to defend critical components such as the main shaft and yaw bearings.
The completion of our new state of the art testing facility enables BGB to complete the full manufacturing and testing process on-site, ensuring that all products meet the required industry gold standard for operation. With the ability to recreate a range of environmental conditions, including high temperatures and humidity controls, all components can be examined rigorously before being transported off-site.
Another method is the use of weather systems to analyse metrological data to predict the probability of a strike in a given area. Lightning sensors can also be installed at a wind farm to predict upcoming strikes using local measurements. Although these systems provide some support, they are unable to tell if a turbine has been hit directly and often leave damage from a near strike unnoticed.
This means that a strong O&M plan, including the implementation of regular, high-quality inspections, is also crucial to a profitable wind farm. With a broad range of damage as a result of lightning strikes, a detailed inspection is often the only way to fully understand the impact and ensure the safety of continued operations.
With more than 1,700 electrical storms across the world at any time and more than seven million strikes per day, lightning will continue to pose a constant threat to wind farms. The key for operators will be to decrease downtime and extend the reliability of turbines by preventing damage from direct or nearby strikes.
Although monitoring weather conditions and performing highly detailed inspections will help O&M teams to keep turbines in action, using high quality and thoroughly tested components during the manufacturing process is vital to minimising the risk from a strike.
For more information about BGB’s lightning brush holders, visit our online store.
For more information on Blog: Taking Action To Brush Off Lightning Strikes talk to BGB
Enquire Now
List your company on FindTheNeedle.