
Sign In
Machinery Guard Regulations
13-03-2023
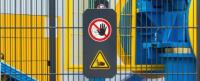
Machinery safety is a crucial aspect of any workplace, as it helps to protect employees from potential hazards and injuries while they operate or work near machinery. In order to ensure a safe work environment, there are regulations in place to govern the design and use of machinery, including those that pertain to guarding. This article will provide a comprehensive overview of machinery guard regulations, including the five types of machine safeguards, the three basic areas that require machine guarding, and the British standard for machine guarding BS EN ISO 12100:2010. With this information, employers can take
Importance of machinery safety in the workplace
Ensuring machinery safety in the workplace is crucial for preventing accidents, injuries, and fatalities. Proper maintenance and operation of machinery can reduce the risk of workplace accidents and injuries, which can lead to significant financial and legal liabilities for businesses. It is essential for employers to establish and implement comprehensive safety procedures and protocols, including regular inspections, training, and hazard assessments, to promote a safe work environment. By prioritizing machinery safety, employers can protect their employees and their business while maintaining compliance with regulatory standards.
Overview of machinery guard regulations
Machinery guard regulations require employers to provide safety guards on machinery to prevent employee access to hazardous areas during operation. Guarding machinery protects workers from potential injury, amputation, and death. These regulations aim to eliminate or reduce the risk of accidents resulting from exposure to moving parts, electrical hazards, or other machinery-related hazards. Employers must ensure that safety guards are correctly installed, functioning correctly, and providing adequate protection. Failure to comply with machinery guard regulations can result in significant fines, penalties, and legal liabilities. Overall, these regulations are crucial for promoting a safe and healthy work environment by reducing the risk of workplace accidents and injuries caused by machinery.
The 5 Types of Machine Safeguards
There are 5 main types of machinery guarding that are available to protect workers from hazardous machine areas: enclosures, interlocks, barrier guards, two-hand controls, and electrical controls. These safeguards are essential for ensuring worker safety and reducing the risk of workplace accidents and injuries caused by machinery. By implementing the appropriate machine guarding, employers can maintain compliance with regulatory standards, minimize legal liabilities, and create a safe and healthy work environment for their employees.
Enclosures
Enclosures are physical barriers that prevent access to hazardous machine areas. They can be either fixed or movable and are designed to protect workers from machine parts that may cause injury or harm. Enclosures are commonly used in conjunction with other safeguards and must be constructed from durable materials that are resistant to damage.
Interlocks
Interlocks are safety devices that prevent a machine from operating until all of its safety features are correctly engaged. They are used to ensure that workers are not exposed to hazards while operating or repairing machinery. Interlocks can also prevent workers from bypassing safety features, which can lead to accidents.
Barrier guards
Barrier guards are safety barriers that are placed between the worker and the machine. They can be either fixed or movable and are designed to prevent workers from accessing hazardous machine areas. Barrier guards must be sturdy and durable to withstand damage from external forces.
Two-hand controls
Two-hand controls require the operator to use both hands to start and continue operating the machine. They are designed to keep the operator’s hands away from hazardous machine areas, preventing injuries that could occur if an operator’s hand gets caught in the machinery.
Electrical controls
Electrical controls are safety devices that protect workers from electrical hazards associated with machinery. They are designed to detect electrical problems and shut down machinery when a problem is detected. Electrical controls also prevent electrical shocks that could occur if a worker comes into contact with live electrical components.
The 3 Basic Areas that Need Machine Guarding
There are 3 basic areas that need machine guarding: the moving parts of the machine, the points of operation as well as the power transmission apparatus. Failure to adequately guard these areas can result in severe workplace accidents, injuries, and fatalities. Properly installed machine guarding can significantly reduce the risk of accidents by restricting access to hazardous areas, preventing contact with moving parts, and ensuring that machines are not started accidentally. Employers must conduct regular hazard assessments to determine the appropriate type of safeguarding required for each machine, and they must also provide adequate training to their employees on the safe operation of machinery.
Moving Parts of the Machine
The moving parts of the machine that usually need guarding include any part of the machine that moves during operation, such as gears, belts, pulleys, rotating shafts, flywheels, and reciprocating parts. These moving parts can cause severe injuries or fatalities if workers come into contact with them, so they must be adequately guarded to prevent access. Guards for moving parts can be either fixed or movable, depending on the type of machine and its operation. Guards should be constructed of durable materials and designed to prevent workers from accidentally coming into contact with the moving parts. Additionally, guards must not create new hazards, such as sharp edges, pinch points, or protrusions that could cause injury.
Points of Operation
The term “points of operation” refers to the area on a machine where work is performed. It is the point where the machine’s tool contacts the material being worked on, such as the point where a saw blade cuts through wood or where a punch press stamps a piece of metal. The points of operation are typically the most hazardous areas on a machine, as they involve the interaction between the machine and the material being worked on. Hazards in these areas can include cutting, shearing, crushing, and puncturing.
Workers can be at risk of severe injuries or even amputations if their hands, fingers, or other body parts come into contact with these hazardous areas. It is, therefore, essential to provide adequate safeguarding, such as barriers, shields, or light curtains, to prevent access to the points of operation and protect workers from injury.
Power Transmission Apparatus
Power transmission apparatus refers to the mechanical components of a machine that transfer power from the source, such as an electric motor, to the machine’s moving parts. These components may include gears, pulleys, belts, chains, and couplings, among others. Power transmission apparatus can be a potential source of hazards, including entanglement, shearing, and crushing, if they are not adequately guarded. It is essential to ensure that workers cannot come into contact with power transmission apparatus during machine operation, maintenance, or repair, as such contact can lead to serious injuries or fatalities.
The British Standard for Machine Guarding
The British Standard for Machine Guarding is a set of guidelines established by the British Standards Institution to ensure the safety of workers who operate or maintain machinery. The standard provides guidance on the design, manufacture, installation, and use of machine guards, as well as information on the selection and use of other safety measures, such as safety distances, interlocks, and emergency stop controls.
BS EN ISO 12100:2010
BS EN ISO 12100:2010 is a specific standard that provides the general principles for designing safety-related parts of control systems.
Key provisions of the standard
The key provisions of the standard include identifying hazards associated with machinery, assessing the risk level of each hazard, selecting the appropriate safeguarding measures to eliminate or reduce the risk, and ensuring that the selected safeguards are properly installed, maintained, and tested.
Importance of adhering to the standard
Adhering to the standard is crucial for ensuring that machinery is adequately safeguarded and that workers are protected from hazards that can cause accidents, injuries, or fatalities. By complying with the standard, employers can ensure that they meet regulatory requirements, minimize legal liabilities, and create a safe and healthy work environment for their employees.
For more information on Machinery Guard Regulations talk to Billington Safety Systems Ltd
Enquire Now
More News
List your company on FindTheNeedle.