
Sign In
Ways to Improve Machine Safety in Factories
13-03-2023
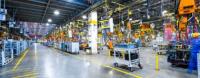
Machine safety is a critical aspect of running a successful factory. The safety of workers and equipment is vital for ensuring efficient and effective production, reducing accidents and injuries, and avoiding costly penalties and legal liabilities. In this blog post, we’ll discuss several ways to improve machine safety in factories and help create a safe and secure workplace environment.
Identifying Hazards
The first step in improving machine safety is to identify potential hazards in the workplace. Understanding machine hazards can help identify risks, allowing employers to establish appropriate safety measures to prevent accidents and injuries. Some of the key steps to identifying hazards include:
Understanding machine hazards: Machines pose various hazards to workers, such as electrical, mechanical, and thermal hazards. It’s crucial to identify potential dangers posed by machinery and create measures to address them.
Conducting risk assessments: A risk assessment evaluates the potential risks posed by the machine to the workers and helps identify appropriate safety measures to address them.
Identifying safety hazards through safety inspections: Regular safety inspections can help identify safety hazards before they lead to accidents or injuries. It can also help detect equipment wear and tear or potential hazards associated with malfunctioning machinery.
Implementing Safety Measures
Once you have identified potential hazards, the next step is to implement safety measures to address them. Safety measures can be divided into three categories: administrative controls, engineering controls, and personal protective equipment (PPE).
Administrative controls: Administrative controls include policies, procedures, and safety rules that help manage safety in the workplace. Some of the administrative controls that can be implemented include limiting access to dangerous machinery and installing warning signs.
Engineering controls: Engineering controls are physical controls that help manage safety in the workplace. For example, guards or barriers that prevent workers from coming into contact with dangerous machinery.
Personal protective equipment (PPE): PPE is equipment worn by workers to protect them from hazards in the workplace. Some examples of PPE include gloves, safety glasses, and hard hats.
Safety training: Training employees on the safe use of machinery is also an important aspect of improving machine safety. This includes teaching workers how to operate machinery safely, how to properly use PPE, and how to report any issues or concerns they have.
Maintaining Safe Machines
Regular maintenance of equipment is crucial in improving machine safety in factories. Proper maintenance helps ensure machinery is functioning correctly and reduces the likelihood of accidents or injuries. Here are some steps to consider when maintaining machinery:
Regular maintenance checks: Regular maintenance checks are necessary to ensure machinery is functioning correctly. This includes checking for wear and tear, inspecting machine parts, and ensuring proper lubrication.
Repairing damaged or broken machines: Damaged or broken machines should be promptly repaired to prevent potential accidents or injuries.
Replacing outdated or malfunctioning machines: Outdated or malfunctioning machines should be replaced with newer models. Newer machines come with enhanced safety features and better designs that reduce the likelihood of accidents and injuries.
Promoting Safety Culture
A culture of safety is vital in improving machine safety in factories. A culture of safety involves creating an environment where employees are encouraged to participate in safety efforts and feel empowered to report any safety concerns they have. Here are some steps to consider when promoting a safety culture in the workplace:
Encouraging employee participation in safety efforts: Encouraging employee participation in safety efforts can help create a safer work environment. This can involve regular safety meetings, safety committees, or employee-led safety programs.
Developing a safety management program: A safety management program is a proactive approach to improving machine safety in factories. This involves developing policies and procedures that help manage safety in the workplace.
Incentivizing safe behaviour: Incentivizing safe behaviour can help promote a culture of safety in the workplace. This can involve recognizing and rewarding employees who demonstrate safe behaviour or meet safety goals.
Staying Compliant with Regulations
It’s important to stay compliant with safety regulations to avoid costly penalties and legal liabilities. Some of the key steps to staying compliant with safety regulations include:
Understanding OSHA and other safety regulations: Understanding OSHA and other safety regulations can help ensure compliance with regulatory requirements.
Adhering to safety standards: Adhering to safety standards can help improve machine safety in factories. This involves following industry standards for safety, such as the National Fire Protection Association (NFPA) standards.
Conducting regular safety audits: Conducting regular safety audits can help ensure compliance with safety regulations and identify potential hazards.
Conclusion
In conclusion, improving machine safety in factories is crucial for creating a safe and secure workplace environment. By identifying potential hazards, implementing safety measures, maintaining safe machines, promoting a safety culture, and staying compliant with regulations, employers can improve machine safety and reduce the likelihood of accidents and injuries. Investing in machine safety measures not only benefits workers but also leads to more efficient and effective production, reducing costs, and improving the bottom line.
For more information on Ways to Improve Machine Safety in Factories talk to Billington Safety Systems Ltd
Enquire Now
More News
List your company on FindTheNeedle.