
Sign In
Coatings for Neodymium Magnets
11-10-2022
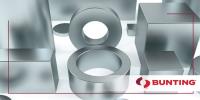
Coatings for Neodymium Magnets
Nearly every neodymium magnet will be plated or coated and, as the most powerful permanent magnet available, they are used in many different applications. However, they possess physical characteristics that require them to be plated or coated in order to protect them from damage. In their raw form, neodymium magnets are quite brittle, and as a result are prone to chipping, breakage, and other types of physical damage. Another concern is that neodymium magnets (which are 65% iron by weight content) are highly vulnerable to corrosion and prone to experiencing erosion and decay if not properly coated. Fortunately, there are many coating options available for neodymium magnets that protect damage and corrosion from occurring.
Types of Coatings
The type of plating or coating used on a neodymium magnet is determined based on the application and environment in which the magnet will be used. One of the most common options is nickel plating, a three-layer plating that combines a nickel layer, a copper layer, and a nickel coating. Nickel options are typically best suited for indoor use, offer excellent abrasion resistance, and are a highly cost-efficient choice. Other nickel-plating options incorporate layers of copper, nickel, gold, and chrome. For those who desire non-nickel metal plating, zinc is also available.
There are various types of non-metal coatings available for neodymium magnets, including Teflon/PTFE coatings, plastic coatings, rubber coatings, and epoxy resin coatings. These coatings are often designed for use in specific applications, and some require speciality manufacturing.
For more information on Coatings for Neodymium Magnets talk to Bunting - Berkhamsted
Enquire Now
List your company on FindTheNeedle.