
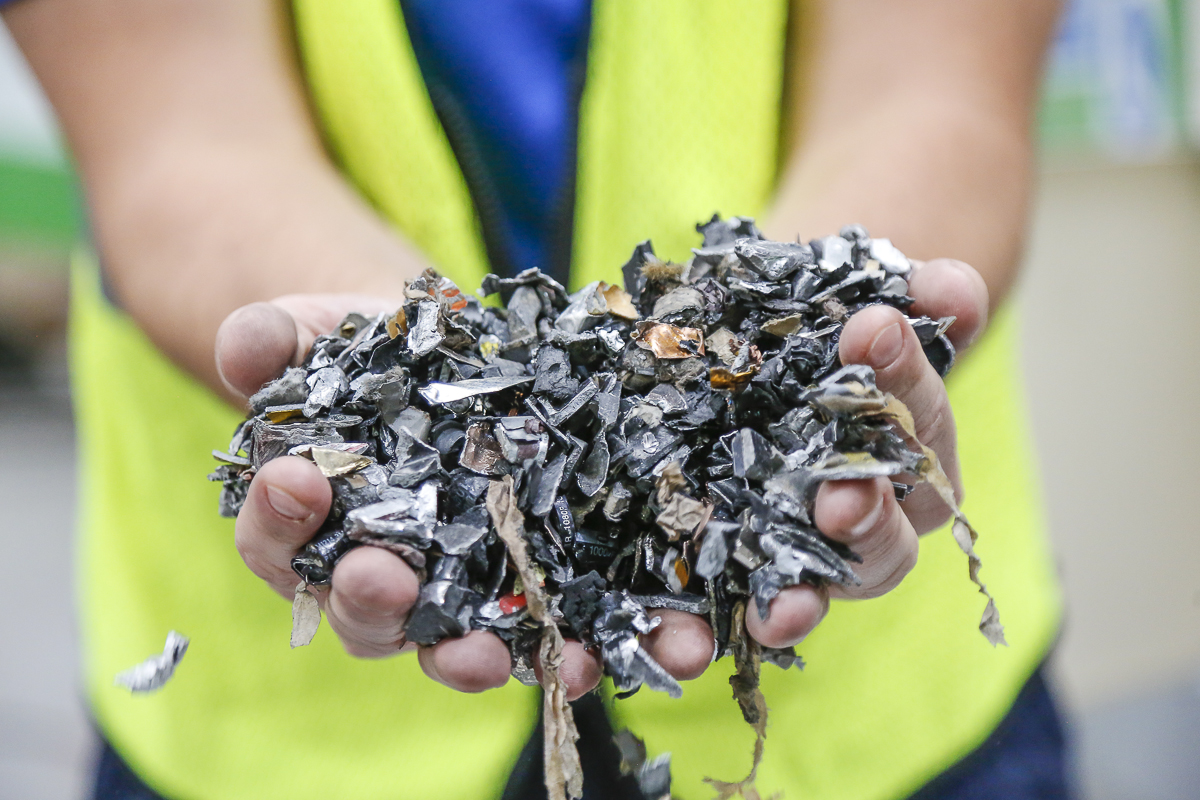
The effective recovery of valuable metals is an important step in the economic viability of recycling e-waste. Technology that maximises metal recovery and purity is the focus for Bunting on stand 110 at the E-Waste World Conference & Expo (28-29 June 2023, Frankfurt, Germany). The Bunting team is joined on the stand by local representative Marcel Graef from 3SMI.
Huge potential of e-waste
Global e-waste is estimated to hold approximately 56 billion Euros’ worth of raw materials such as gold, palladium, silver and copper. However, only 17% of global e-waste is reported as being collected and properly recycled each year. The depletion of mining reserves and the rising cost of mined ore highlight the necessity of ‘urban mining’, where valuable metals are recovered from secondary materials such as e-waste.
The nature of e-waste means that metal recovery often requires complex processing with specialist equipment and separation technology playing a key role in successful recycling.
Metal separation when processing e-waste
There are several stages of metal separation in a typical e-waste recycling plant, for which Bunting provides solutions. Ferrous metal recovery is commonly early in the process, with relatively straightforward recovery using Overband Magnets, Drum Magnets or Pulley Magnets. These are both in standard strength ceramic ferrite and high-intensity rare earth magnet designs.
The recovery of weakly magnetic materials, such as fragmented stainless steel and even printed circuit boards, has frequently proved problematic. The patented SSSC and HISC magnetic separators use exceptionally strong magnetic fields to preferentially separate the weakly magnetic fraction.
After the removal of the magnetic materials, the focus turns to non-ferrous metals, including aluminium and copper. Bunting developed the High-Intensity Eccentric (HIE) Eddy Current Separator to separate non-ferrous metals as small as 3mm and often smaller. The remaining fine fraction is passed through an ElectroStatic Separator, which enables the recovery of metals such as fine copper wire.
E-Waste Conference and Expo
At the E-Waste Conference and Expo, Bunting’s team will draw on the experience of installing metal separation equipment at e-waste recycling facilities such as Zixtel Ltd in the UK. Zixtel’s engineering team designed and built an e-waste recycling plant, which included a Metal Separation Module and Overband Magnet from Bunting. The Module included a high-intensity Drum Magnet for separating weakly magnetic materials and an Eddy Current Separator to recover non-ferrous metals.
With the existing process, Zixtel presently handles in excess of fifty different product streams. The material output of the plant is 70% metal, 25% printed circuit boards and plastics, 5% destined for an energy-to-waste plant, and 0% for landfill.
To support companies who are developing e-waste recycling operations or are seeking to improve metal recovery rates, Bunting has a material test facility to assess separation capabilities. The Customer Experience Centre at Bunting’s Redditch facility in the UK is home to a wide range of metal separation equipment, including the ElectroStatic Separator and Eddy Current Separator.
“E-Waste has never held a greater value,” explained Bradley Greenwood, Bunting’s European Sales Manager. “The successful recovery of metals involves many stages of size reduction, screening, and separation. Our metal separators play a key role in that process, maximising the recovery of metal prior to more complex processing. We look forward to speaking with e-waste recyclers at the conference.”
For more information on Metal Recovery Solutions at E-Waste World Conference 2023 talk to Bunting - Redditch