
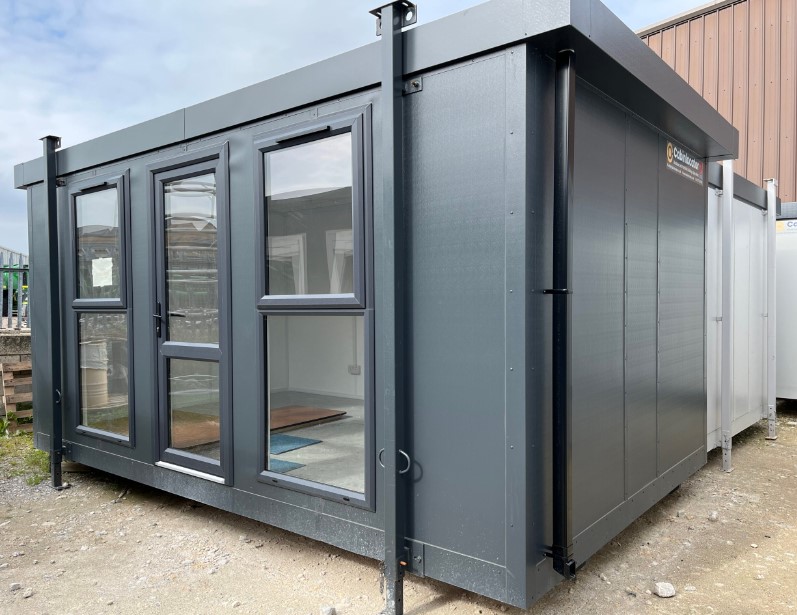
Modular and portable buildings are widely used throughout the healthcare industry, and they have been in especially high demand in recent years. In the latest development, the UK government has announced that £50m of funding will be released to create six new ambulance hubs plus an extra 42 discharge lounges at hospitals throughout England.
Some of these additional buildings will be temporary, such as the extra facilities recently created at the James Cook University Hospital in Teesside. The unit was built to reduce the waiting times for ambulance handovers and to enable the faster discharge of medically fit patients, in order to free up beds.
The Gazette Live reports that NHS England requested the hubs in response to patients facing lengthy waits to transfer from ambulances to A&E. Retrospective planning permission was applied after the modular buildings were installed on top of an existing car park.
The design and access statement submitted to the council reads: “The new modular building provides much needed clinical space incorporating a series of bed bays, WC facilities and clean and dirty utility rooms. The Temporary Emergency Ambulance hub increases capacity for discharge and the reduction in ambulance waiting time.”
This is just one example of how modular buildings can be used in the healthcare sector. Constructing a traditional bricks and mortar building would have taken months or even years, and caused significant disruption at the site. In the meantime, ambulance waiting times would have increased even more sharply.
In contrast, the temporary modular buildings were in place in a matter of weeks. Most of the manufacturing and assembly process takes place off-site, minimising traffic congestion and dust and noise pollution in the locality. This is a particular concern in a healthcare facility, where patient access, safety and comfort should be the main priority.
Cost effectiveness is also a strong consideration for such facilities. Modular or portable buildings can be installed for a fraction of the cost of a traditional building. The standardised construction process means that they are not subject to the same delays and disruptions that regularly occur in on-site construction.
For example, adverse weather conditions can mean that work is slowed or even completely paused, and it can also damage materials and equipment. After an episode of bad weather, the risk assessment process needs to be repeated, reviewed, and signed off all over again to ensure that safety standards are maintained on a traditional construction site.
On-site construction projects are also regularly held up by supply chain issues, particularly at the moment when certain materials are still in short supply and there’s a shortage of HGV drivers. Most of these issues are avoided with off-site construction.
The healthcare sector faces multiple time-critical challenges and remains under financial strain as it recovers from the huge impact of the Covid pandemic. Premium portable buildings are an ideal solution to create extra facilities that are cost efficient, minimally disruptive and quick and pain free to install.
For more information on Temporary Ambulance Hubs To Provide Extra Support for NHS talk to Cabinlocator Ltd