
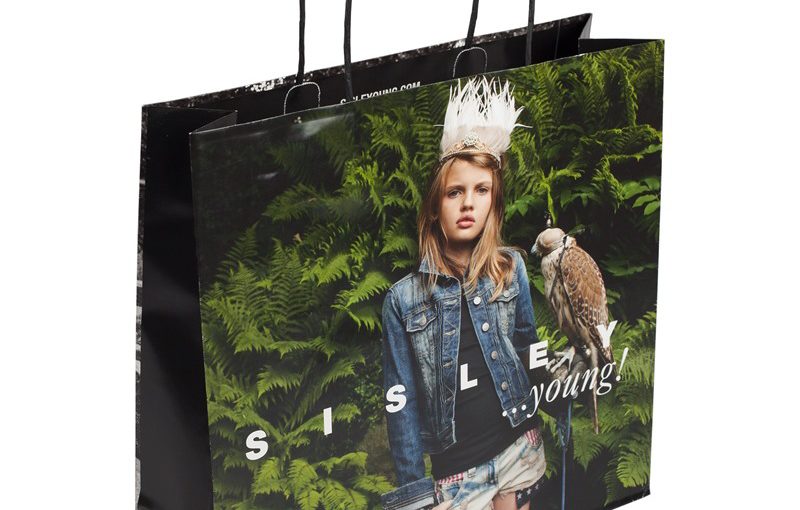
Printing Process Unravelled
On this week’s blog we talk about the printing service we offer to our customers and go into a little bit more advice on each of the steps that need to take place in order to get there!
Check out our 6 step process below:
What will you use the bag for?
The first question we would ask our customers is what will the bag be used for? If we know what you are using your bag for, we can determine the type of bag that would be best suitable for your needs based on size, strength and material.
Discuss What You Want
Tell our team what kind of print you have in mind, prompts to help you would include:
- What colours did you want printing? Single colour? Many colours? If your logo has a select number of block colours our printer will often use a Pantone which is a pre mixed colour swatch. This is the most common colour matching system we use to print with.
- Do you have a design/logo in mind?
- Do you have a sample of the artwork?
- What finishes do you require? e.g ribbon handles
Once we have talked through your requirements our team will advise you on the best printing solution for you.
We currently offer the following types of printing:
Flexo Printing
This method of printing uses a flexible (rubber-like) plate to transfer your desired artwork to the bag. Is works the same way as a stamp and is known as a modern version of letterpress. This type of printing is used on plastic, paper and metallic surfaces.
✓ 1-8 colours (depending on printing method)
✓ Print from 500 bags
✓ Pantone required upon delivery of artwork
✓ Paper
✓ Plastic
Lithographic
When printing Litho you are able to print a range of tones, shades, gradients and colours. The image is transferred onto paper or other material using an aluminium plate. The finished artwork is of a good quality and is often used for printing photography or publications.
✓ Pantone required upon delivery of artwork
✓ Paper
✓ Plastic
Screen Printing
This is a stencil method. In this technique the ink is squeezed through a mesh and onto a suitable substance. Often used in T-shirt printing and various other fabrics.
✓ Up to 4 colours
✓ Pantone(s) required upon delivery of artwork
✓ Jute
✓ Cotton
✓ Canvas
Send You A Visual Proof
Once your print requirements have been discussed and we have come to an agreement on the print method, quote and timescale, we will send you visual proof to check that you are happy with the printed packaging you will be receiving. In addition you are required to sign off your sales order at this stage.
Things to look out for are:
- Are all spellings correct
- Are the dimensions right
- Is the logo or design correct
- Are the colours correct
Each of our bags have a specific print area. It isn’t necessary for you to know the print areas as our artwork team will handle the technical specifications of applying your artwork to the bag but please bear in mind that we won’t be able to take your artwork all the way up to the edge of the bag due to the printing methods used.
Good To Go!
Only when you confirm that you are happy with everything, will we begin the process of having your goods printed for you.
Print Delivery
The timescale of your printing depends on a number of factors (such as the type of printing and quantity of your order). We promise to give you a good idea of how long it will take, and deliver your goods promptly.
Happy Customer
We hope you are happy with your packaging and should you need any more packaging in the future, we will be more than happy to help!
If you would like more information, a sample or a free quote, then give us a call on 0203 002 9960 and our specialist staff will give you honest and expert advice on exactly what we can do for you.
For more information on Our 6 Step Guide to Getting your Bags Printed talk to Carrier Bag Shop