
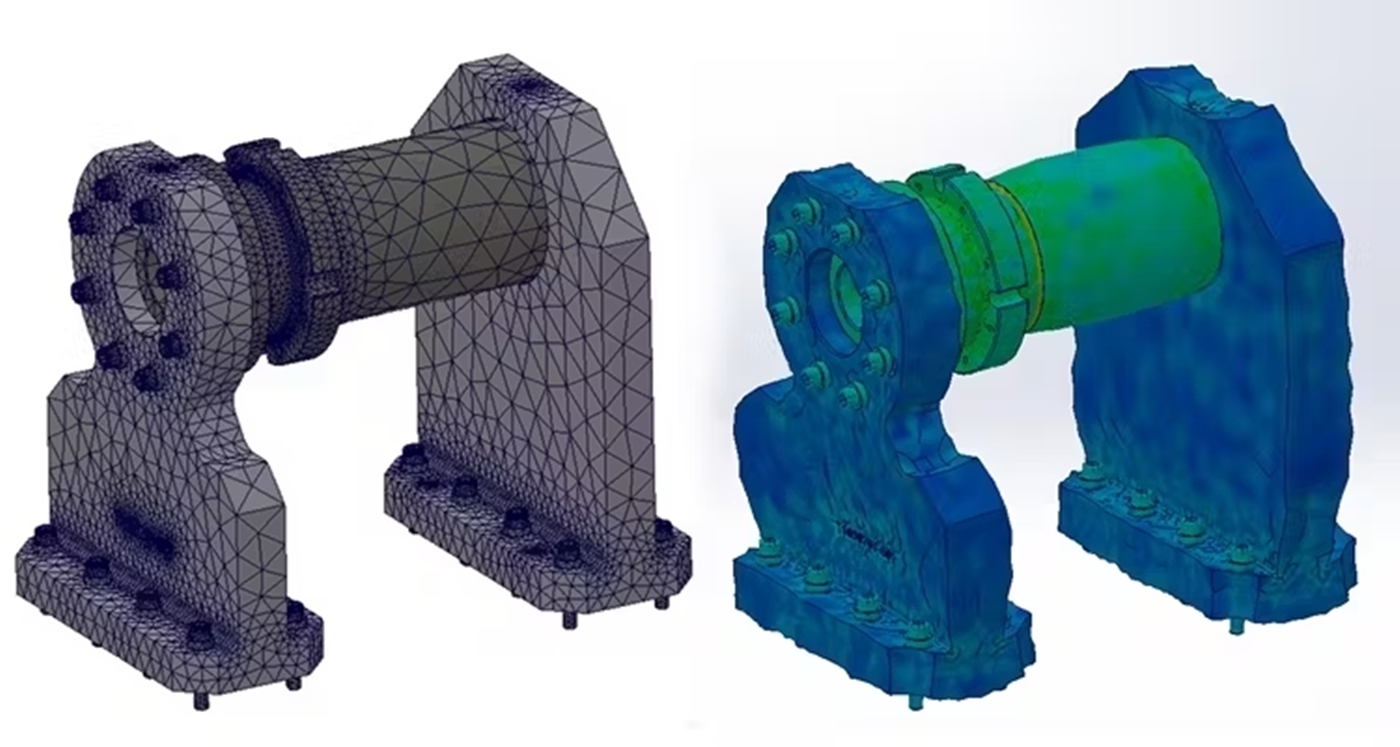
Protean Electric is a world leader of in-wheel motor (IWM) technology for passenger cars, light commercial vehicles, future transport solutions and more. Their IWMs are designed to deliver high levels of performance, efficiency, and sustainability for myriad solutions. Protean’s motors deliver a host of benefits including creative freedom for original equipment manufacturers (OEMs) and driving benefits for the consumer allowing increased interior space as well as more packaging for battery, increasing range.
Facing Challenges, Seeking Solutions
Yet, pioneering such revolutionary technology comes with challenges. In-wheel motors, positioned inside the wheel, must endure harsher operational conditions and external forces. These motors face higher shock and vibration levels due to road conditions, making stringent durability testing crucial.
Protean Electric encountered testing challenges that required innovative solutions. To tackle these issues and enhance their product development cycle, they partnered with CentraTEQ, an expert in custom-designed fixtures and vibration testing solutions.
The Collaborative Approach
Protean Electric’s goal was clear: develop a custom fixture capable of supporting the test item during vibration testing within specific parameters. The fixture needed stability in multiple axes, a wide frequency bandwidth, and the ability to withstand intense acceleration and temperature variations.
Through close collaboration with Protean Electric’s engineers, CentraTEQ designed a specialised “H” fixture. This fixture’s symmetrical support structure minimised unwanted vibrations, and thoughtful design elements allowed for seamless rotation of the payload without disassembly.
Success Through Partnership
Protean Electric successfully conducted vibration tests using the custom fixture. Mark McDonnell, Protean’s Product Validation Manager, praised the partnership, highlighting the professionalism and technical prowess of CentraTEQ’s team.
This successful partnership underscores the significance of tailored fixture design in vibration testing. It emphasises the importance of working with experienced experts who have a comprehensive understanding of vibration test fixture design, including the properties of the fixture materials used, their resonant frequencies, and how they may impact the testing.
To learn more about this collaboration, read the full article published in Engineering magazine here.
For more information on Overcoming Vibration Testing Challenges: A Success Story of Collaboration talk to CentraTEQ Ltd