
Sign In
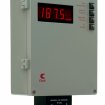
Steam Condenser Air In-leakage Monitoring
John Addy & Jamie Shanahan,
Applications Engineers
Chell Instruments Ltd
You have to measure it to control it:
Condenser performance is one of the largest factors affecting thermal power generation efficiency, profitability and emission levels. Air ingress causing a 10 mmHg increase above condenser design pressure and therefore turbine exhaust pressure, will typically reduce generator output by 1%, or increase fuel consumption correspondingly. Without a real time monitoring system these leaks can, and often do, exist for weeks before they are detected, costing hundreds of thousands of pounds worth of additional fuel use and associated emissions. Larger leaks can cause a build up of air that blankets the condenser cooling surfaces, preventing steam from reaching them and causing a rise in condenser temperature. This in turn causes a further rise in condenser pressure, and turbine inefficiency. Similar effects are caused by poor condenser cooling water/air flow, as well as inadequate suction from the pumps used to remove non-condensable gases. Therefore the ideal monitor should provide continuous readings of temperature, absolute pressure and air ingress, to allow condenser problems to be fully diagnosed.
Historical methods:
Past methods of air ingress measurement have tended to use variable area meters, or orifice plates and differential pressure transducers to measure flow rate on the exhaust of the vacuum pumps, both of which create a flow restriction making them unsuitable for permanent use. Other devices have been tried but suffer from sticking, clogging and corrosion due to the wet media and also measure any air leak that the pump itself has. Switching off the air extraction pumps and measuring the rate of pressure rise in the condenser may be suitable where air ingress rates are low but does not provide a continuous reading.
Optimal solution:
Chell Instruments have developed an instrument that uses a rugged probe installed at a common point in the air extraction line to not only continuously monitor air ingress to the condenser but also temperature and absolute pressure. The probe has no moving parts and has all 316 stainless steel wetted surfaces to overcome the problems experienced with previous techniques. It is not affected by hostile operating conditions and is installed between the condenser and vacuum pumps to avoid measuring leaks in pump seals. The AIM100 control unit provides a local display and continuous analogue and digital outputs that can be viewed and logged remotely.
Optimal solution: cont'd.....
Validation of the original design was carried out in conjunction with a UK power producer, where it was initially exposed to controlled dry air leak rates into a test pipeline, then transferred to a condenser air extraction line and tested under actual operating conditions. The instrument responded quickly to changes in flow rate, its readings corresponded closely to the input flows and there were no problems with reliability. Since then instruments have been continuously operated reliably in a number of power plants for more than 20 years.
Benefits:
Real time indication of air ingress is an invaluable tool for efficiency engineers:
Showing trends – Allows faults to be detected at an early stage.
Instantly confirming results when a repair or maintenance cycle has been carried out – Confirms whether actions have been successful.
Improving reliability – Early detection avoids unplanned shutdowns.
Reducing running costs and plant corrosion – Reduced fuel consumption, fewer vacuum pumps to purchase, maintain and run, lower dissolved oxygen levels in boiler water.
Lowering pollution and CO2 emissions – A direct benefit of greater efficiency.
Regaining lost output – Due to improved turbine efficiency.
Condenser temperature:
As previously stated other conditions can cause elevated condenser pressures, such as poor condenser cooling water flow, elevated coolant inlet temperature, fouled cooling tubes, poor cooling tower performance, or low tide or river conditions. By continuously monitoring the Air Ingress Monitor’s temperature, pressure and air ingress measurements, a condenser pressure change due to temperature change is immediately visible.
Vacuum pump condition:
Poor vacuum pump performance is another common cause of elevated condenser pressures, with operators often switching in additional pumps during peak load operation. Again, by monitoring the AIM-100’s temperature, pressure and air ingress measurements, it can be seen when a vacuum pump’s performance has degraded. This can be confirmed by switching between different pumps and comparing the pressure.
Vacuum pump condition: cont'd....
Failing or cavitating pumps also often cause rapidly fluctuating pressure spikes which again will be monitored by the AIM.
The cost of purchasing, powering and maintaining additional vacuum pumps to cope with increasing air ingress, though less than running with increased turbine back pressure, can be substantial but is often overlooked.
Indication of air ingress source:
The AIM100 cannot pinpoint the source of air ingress but the data provided is a great help in narrowing the search area. During light load operating conditions the condenser pressure is usually lower and more of the turbine and its associated components are exposed to vacuum. By monitoring the air ingress measurement under different load conditions, it is often possible to determine the approximate area of the leak source and therefore reduce the time taken to locate it. This can often be confirmed by sticking a patch over the suspected leak and checking for an immediate change in air ingress reading.
Conclusions:
Fuel costs and plant emissions are under constant scrutiny, whilst maintenance budgets are being squeezed. Chell's AIM100 Air Ingress Monitor provides the real-time information required to reduce or minimise both fuel costs and plant emissions without the need for additional staff. The potential cost savings are enormous, often hundreds of thousands of Pounds per year, giving a payback on investment of just a few weeks.
For more information on Steam Condenser Air In-leakage Monitoring, an application note talk to Chell Instruments Ltd
Enquire Now
List your company on FindTheNeedle.