
Sign In
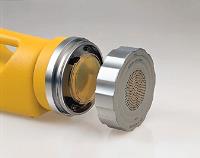
Delivering a professional service
Cherwell has always strived to offer a professional service, one that understands the needs of our customers. Easy to say, I hear you cry, but how do you actually demonstrate this. Whilst in conversation with our service engineers, a few points came to light that show this commitment.
Our engineers are in a unique position in that they can get into the very heart of our customers businesses when performing on-site calibrations for the SAS air samplers - a service that we have seen grow significantly over the last couple of years. In fact, our engineers now travel as far and wide as from the west coast of Ireland to mainland Europe and from the north to the south in the UK.
Following your procedures
At each site they see something different but there are common themes. Site induction and health and safety are important at most sites they visit. In fact induction procedures can take over an hour, therefore, it is important that we arrive on site in good time and of course listen and adhere to the site rules. After all a modern pharmaceutical manufacturing site is complex with many risks, we must act professionally whilst on site at all times.
I mentioned that our engineers can get to the very heart of the site, often we are asked to enter the manufacturing suite. Gowning is a key part and something that doesn’t faze our team. We run our own clean room facility and our engineers provide vital support to these facilities, so being familiar and competent in gowning procedures are a must for them.
Recognising the importance of flexibility
However, most of our clients will bring the equipment to a laboratory type area for service and calibration. This doesn’t always go smoothly as pressures at the clients site may mean the samplers aren’t ready to be released. We aim to arrive on site prepared and organised, however, being patient and flexible is also vitally important. Our engineers recognise all too well that even in shiny, large pharmaceutical plants things don’t always run exactly to plan. One can only imagine how challenging this may be when they have multiple service companies on site during a shutdown period!
Of course, whilst on site the engineers will undoubtedly face questions about what they are doing, is this result good, what’s the impact of that ‘as found’. The team are well experienced and knowledgeable in fielding these questions and explaining the equipment and calibration process. We recently improved our calibration process and equipment, for example a battery powered test meter provides greater flexibility and allows us to perform calibrations even within the clean room without needing to access power.
So, do I think we provide a professional service which understands the needs of our customers? Absolutely! If you want to put us to the test, please contact our Service team.
For more information on SAS Air Sampler On-site Calibration at Customer Facilities talk to Cherwell Laboratories Ltd
Enquire Now
More News/Blogs
List your company on FindTheNeedle.