
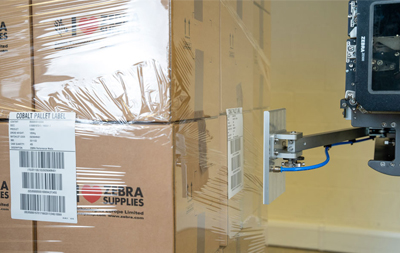
In this second part of our guide to print and apply barcode labelling automation, we’ll look at the specifics of which machine type and tools are suitable for your production line.
If you want to refer back, part one of this guide introduced the concept of print and apply and whether it’s the right approach for your business.
Part two is intended to get you thinking about the specifics of your environment and how automating the print and application of labels will fit into your business and production line.
The guide covers the following:
- Labelling requirements (label position & quantity)
- Type of product and packaging material
- Variety of packaging/outer cases
- Speed of production line throughput (and impact of downtime)
Labelling requirements (label position & quantity)
Different industries have different barcode labelling requirements. Whether adhering to GS1 for retail or ensuring your pallets are SSCC (Serial Shipping Container Codes) compliant, it’s usually business-critical to get it right.
Added to that mix are the individual requirements of specific customers who might require a particular configuration of labels. So, the first thing to establish is where you need to apply labels on your outer packaging and how many you need to apply.
Our range of print and apply machines can print on one, two or even three faces of outer packaging in a single step.
Our standard configuration machines can print and apply barcode labels as follows:
-
- Top only
-
- Front only
-
- Side only
-
- Bottom only
-
- Top & side
-
- Two adjacent sides (a superior solution than a wraparound label)
-
- Front & side
-
- Three sides (of a pallet)
Type of product and packaging material
Once you know how many labels need to be printed and where they will be applied to your packaging, the next step is to determine how the label will actually be stuck on.
There are various methods which can be used to apply an adhesive label. These include:
-
- Tamped: Physical pressure is applied – either by the machine mechanism or the movement of the outer packaging against the machine as it moves down a production line.
-
- Wipe on: Labels are dispensed off a beak directly onto the product and pressure is applied (often by a roller) to ensure adhesion.
-
- Air blown: The label is held in place on the non-adhesive side using a vacuum of air which is then reversed to blow the label onto the packaging surface.
-
- Air blown & tamped: Combination of the two methods described above.
The correct method is often dictated by the surface texture and material of your outer packaging. For example, rougher surfaces typically need to use a tamp application method to ensure appropriate adhesion, as might a non-flat surface or ‘lumpy’ products (imagine a plastic bag of loose components).
Air-blown applications tend to work well where the arm of a machine is required to move to meet the face of the outer packaging, as the air vacuum holds the label securely in situ under movement. Tamping can be added when the packaging material is not smooth enough to ensure adequate adhesion by air blowing alone.
For irregular or rough surfaces, a foam pad keeps the label’s face wrinkle-free but absorbs irregularities in the packaging surface.
Machines dedicated to specific materials and surfaces also exist. For example, our Drum Printer Applicator is designed specifically for printing and applying large synthetic labels that meet Global Harmonisation Standards for chemical-based products (GHS).
One important consideration is whether or not you use compressed air in your production facility. If not, then we have a range of all-electric print and apply machines that be configured for your production line.
Variety of packaging/outer cases
The variations of outer packaging types you use can have a significant bearing on the best type of print and apply machine for your business.
In a simple environment with a small number of outer pack sizes that only change infrequently (e.g. 12 unit packs manufactured Mon-Wed and 6 unit packs Thu-Fri), it’s simple enough to stop the machine and switch the configuration to cope with the change in outer size.
But if you have a range of different sizes, then more advanced options can work in your favour to increase automation and remove the need for human resources.
A straightforward configuration might be a mechanical switch that allows an operator to choose between single-sided or two-sided labelling without stopping the machine and the line. This is an ideal set-up where the same product is shipped to different customers with different labelling requirements.
An advanced approach is when our machines use a ‘recipe-driven database’. This is achieved by pulling live information from ERP software to automatically identify a product type on the line and then printing and applying the correct number of labels in the right location, all in real-time.
Speed of production line throughput (and impact of downtime)
One of the most essential factors in determining the correct machine or solution for your business is the speed of your production line and the impact of unplanned downtime.
There are various methods available to accommodate higher speed lines, which can either be specified from our standard range of machines or be built as a bespoke solution.
With high-speed packaging lines, there tends to be greater uniformity of product size, particularly in an FMCG environment, so it’s possible to deal with high volumes on a fast line by using an applicator in a fixed location. In addition, removing the need for the applicator to carry out a movement to apply a label removes time to apply and therefore means you can print more and apply more.
However, the system will need media replenishment, preventative maintenance such as cleaning and corrective action in such a case where a barcode label is detected as substandard.
In some production environments, the time it takes to overcome such issues won’t be a problem. Product can be allowed to back up and get back up to speed over time. But for many organisations that’s not the case.
When specifying any part of your line, it’s prudent to ask yourself some difficult questions…
-
- How much would it cost if the line went down for 5 minutes, an hour, half a day or 2 days?
-
- What would the knock-on effect be on deliveries and customer relationships?
-
- How quickly can I get my line back up and running?
-
- Can my own team fix the issue or do I need a service technician?
On a 24/7, high-speed production line, any period of downtime can have a significant impact on output and a machine that is supposed to deliver savings, rapidly starts to become a cost. To counter this, we offer a continuous operation system that provides many benefits.
Rather than rely on a single print head on a machine, our Continuous Operation Machines usually feature two or three print and apply heads but can be more. This feature allows a production facility to counter all the potential causes of downtime and increase production output speed safe in the knowledge that the line will be able to cope. It works by allowing the additional print and apply heads to automatically activate when required.
Optional in all Cobalt’s systems is onboard barcode verification for barcode quality control. This is usually specified into continuous operation systems. When a fail code is detected it is never applied to the product. Instead, it is held on the pad and the secondary head automatically takes over.
It is also equipped with machine vision and industrial scanning technology, to check that the already verified label has been successfully applied to the product and still reads correctly, if not the secondary units take over and reapply a new label.
Equally, if the primary print head runs out of labels, the secondary machines take over while the primary machine automatically withdraws itself from the line so new media can be added.
While a continuous operation machine is more involved than a single unit, it provides absolute peace of mind against increased line speed, unplanned downtime and automatic self-correction of incorrect labels. These machines are the platinum standard for environments where downtime is simply not an option.
Whatever your production requirements, our range of print and apply labelling solutions are able to meet your needs.
Part three of this guide breaks down everything you need to consider in shaping your own Print and Apply solution, including:
-
- People: operators and engineers
-
- Anticipated throughput
-
- Integration with other parts of the production line
-
- The flexibility of the production line environment
-
- Installation and commissioning
-
- Operating Environment
-
- Quality Control
-
- Software and security
-
- Usability
-
- Futureproofing
For more information on Choosing the Right Machine and Tools for your Production Line talk to Cobalt Systems Limited