
The Cost of Downtime in Production Lines
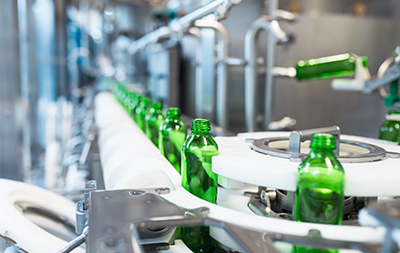
In any modern production or manufacturing environment, continually moving finished products down the line is vital. Therefore, avoiding downtime becomes crucial to ensuring that the process of manufacturing goods is as smooth as possible, cutting down on both the tangible and intangible costs associated with downtime.
According to a Forbes report, manufacturers face an average of 15 hours downtime per week, and a 2017 report by Deloitte found that downtime costs industrial manufacturers over £40 billion annually.
Skip to a section:
Why does downtime occur in production lines?
As any manufacturer knows, there are different types of downtime, each associated with differing costs and downsides. Planned downtime, wherein machines are scheduled to reduce capacity or stop production to carry out planned maintenance, is a core part of the production line’s function; unplanned downtime occurs when machine parts fail, machines jam, or when the entire machine shuts down unexpectedly.
Unplanned downtime can occur when machines aren’t properly maintained at regular intervals or when one part of the production process is overlooked for an ongoing period. Machine part failure is one of the biggest causes of unplanned maintenance.
Inadequate staff training and unclear standard operating procedures can also lead to downtime for your production lines, either through a lack of ongoing maintenance or having your staff not know what to do when the production line isn’t running.
Unplanned downtime can also occur due to circumstances outside your control, such as during power outages or IT issues. For larger companies, backup generators can help to attenuate the effects of power outages, but with the increased connectivity of IT systems crucial to Industry 4.0 thought, downtime due to issues here can be hard to plan for.
While planned downtime can be accounted for, unplanned downtime can result in both direct and indirect costs for businesses. Ensuring that all sections of the production line are maintained and that any downtime is planned and mitigated is the best way to cut unnecessary costs and ensure that products continue to roll off the production line.
The direct costs of downtime
The direct or tangible costs of downtime are the immediate results of having to lower capacity or shut down production for a period. These are the most visible downtime costs, including the loss of capacity, loss of production, direct labour costs, and the impact on inventory.
Loss of production
Downtime can result in delays during production, meaning that orders have an increased lead time. These delays can indirectly impact your business’ reputation, but the most immediate effect of a machine part breaking down can be the whole production line having to shut down.
Not only will this mean that new products aren’t produced, but also you will have idle employees unable to complete their jobs while still costing the business wages and losing potential income through sales. Alleviating downtime by building redundancies into your system can help to lessen these downtime costs.
Loss of capacity
Even when all machines are working correctly on a production line, often companies leave excess capacity: unused machines ready to deal with any sudden increase in demand. For example, suppose a machine breaks or has to be shut down unexpectedly. In that case, the effective capacity of the production line is immediately diminished – potentially below acceptable levels where a company might not be able to deal with an increase in demand.
This could further increase lead times and increase the possibility that customers receive goods late. While not downtime per se, this loss of productive capacity can impact a production line and wider business.
Repair costs
If downtime occurs due to machine part failure, alongside the costs associated with loss of capacity and production, companies must consider the costs of repairing or replacing the broken parts. Whether this includes hiring specialised technicians or engineers to diagnose and solve the problem, or testing that the equipment works appropriately once installed and repaired, the costs associated with a broken machine part can increase quickly.
Direct labour costs
Any machine shut down in the production line means that employees cannot complete their work. Therefore, as well as losing potential income through not producing new parts, downtime continues to cost the business through the salary costs of the employees who are unable to complete their tasks.
Inventory costs
If your production process has shut down at an inopportune time, you may have to scrap any partially incomplete products and begin the process afresh. Smaller production lines might only experience a minor impact, but a temporary shutdown can mean huge scrap and rework costs for larger companies. Furthermore, if this failure occurs at the end of the production line, such as during package or pallet labelling, the entire inventory on the production line at that time might have to be scrapped – especially for time-critical products such as food.
The indirect costs of downtime
The intangible costs of downtime can be far-reaching, with a small production line shutdown leading to far more significant impacts throughout the business beyond the factory floor.
Responsiveness
When downtime occurs, not only are the production line employees affected, but also those who work on processes indirectly impacted by the broken part. As a result, fixing the issue becomes of utmost importance, meaning that other less critical – but still crucial – tasks aren’t dealt with as quickly as they might be. The knock-on effects of downtime can result in a loss of time elsewhere in the business beyond the production line, and compound lost potential income.
Loss of reputation
One of the most critical indirect consequences of downtime can be gaining a reputation as unreliable. Frequent downtime can lead to your business gaining an unwanted reputation in your industry, making it harder for you to attract new customers and employees.
Loss of customer goodwill
If any downtime associated with production shutting down affects your ability to deliver goods to customers on time, you risk losing customer or client goodwill. Compounding the loss of reputation that downtime might have on your company, a loss of customer goodwill could result in your core customers exploring other, more reliable options and ultimately taking their business elsewhere.
How to solve the problem
Predictive maintenance
Although planned maintenance has long been the industry standard for ensuring against downtime, an increase in data production and the use of analytics now allows production managers to anticipate when equipment is likely to fail or require maintenance. Predictive maintenance principles can be applied to production lines of all sizes, such as continuous monitoring to detect problems early and to keep a strict equipment history to see patterns in failures.
Effective training and standard operating procedures
Ensuring that your staff are well-trained and knows the equipment you use inside out can help reduce the impact of downtime on your production lines. When your maintenance staff are equipped with the knowledge to deal with issues quickly, and your production staff have good recovery plans to know what to do when a problem occurs, you can mitigate direct labour costs during downtime.
Built-in redundancies
The best way to deal with machine failures is to ensure that your production line has built-in redundancies that can handle partial failures. For example, having a second or even third piece of equipment or system that can take over if the primary piece fails can minimise the impact of machine failures on the production process and give you time to repair the faulty equipment without having to shut down the production process.
Good service contracts
Another way to mitigate downtime is to work with equipment providers who have an excellent customer service team, effectively building a redundancy into your product from the outset. If the machine does fail or go down unexpectedly, being able to rely on a team that can solve the problem quickly can help you reduce any unnecessary downtime.
Reputable suppliers and build quality
Working with reputable suppliers and ensuring that the parts that you use are reliable can help keep your machines running for longer, without the need for constant repairs. Unplanned maintenance is one of the biggest causes of downtime, so making sure that your equipment is as robust as possible can help to mitigate the effects of machine breakage.
The importance of a robust end-of-line labelling process
As the final stage of the process for many production lines, package labelling and end-of-line labelling machines can be overlooked. However, the end of the production line is one of the most crucial parts, where any downtime necessarily means downtime for the entire production process. Some of the costs associated with downtime can be mitigated by ensuring a robust contingency process exists with your production line.
We offer continuous operation labelling solutions to alleviate downtime at the end of the production line, mitigating any issues from having a single machine fail or jam up. All of our Zebra print engines are also hot-swappable to ensure if there is an issue, a replacement can be fitted in a matter of minutes. This allows any maintenance or repair to occur offline, whilst your line keeps running.
For more information on The Cost of Downtime in Production Lines talk to Cobalt Systems Limited