
Sign In
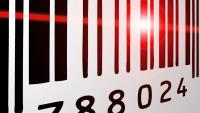
Our guide to packaging line automation offers a visual overview of what a manual, semi-automated and fully automated packaging line could look like. What emerges is a direct correlation between the level of automation and the number of workers required along the line; a manual line requires a larger workforce to carry out tasks and quality assurance processes in comparison to semi or fully automated lines.
In a manual packaging environment, you would typically have a minimum of 3 people completing the process of box erecting, packing, sealing, labelling and palletising. Operating in a confined space has been a problem during the pandemic and social distancing guidelines have forced manufacturers to rethink processes and automate where possible or they drastically reduce the speed of throughput and slow down production.
Book your free consultation today
Social distancing may have been a strong catalyst for packaging automation however there is a constellation of benefits way beyond spacing out your workforce, including increased productivity, efficiency and accuracy. When automating, even in a partial way, you are redeploying workers away from the packaging line and it is important to consider that there are a reduced number of eyes on the line. We want to explain how barcode verification and validation can be utilised as you move towards your automation goals to safeguard your business from errors causing downtime and ultimately your reputation.
First, let us look at the distinction between verification and validation in the world of barcodes. Barcodes are used in almost every manufacturing environment and are pretty much integral to any type of automatic data capture operations. The packaging line is no exception. Without barcodes, manufacturers would find their whole operations slow right down and level of accuracy within operations deteriorate dramatically.
Barcode verification and validation are terms that are often confused, so let us clear that up first. Barcode verification is the process of confirming the print quality of a barcode and ensuring it meets ISO/ANSI standards. Barcode validation ensures that the correct barcode information is being placed on the correct product. It is important that verification and validation work together, otherwise you may end up with the situation where a label passes a validation test but is not up to scratch on print quality, compromising your business. Preventing incorrect or poor-quality bar codes from entering the supply chain eliminates fines, rejects and rework for suppliers.
Image of barcode verification taken from one of our packaging lines
For more information on Barcode Verification and Validation: A crucial component in packaging automation talk to Cobalt Systems Limited
Enquire Now
List your company on FindTheNeedle.