
Sign In
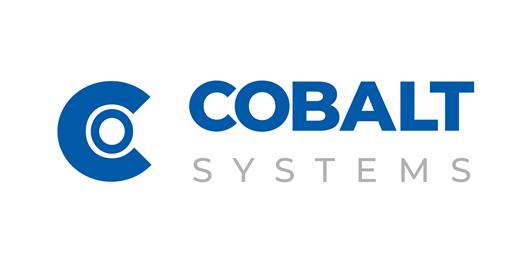
So……. is it worth doing? It’s a question often pondered in boardrooms whenever a change on a production line is being considered. But are the right questions being asked to conclude an answer?
There is no doubt that real time automated labelling has many advantages over a traditional hand labelling operation, but many companies have held back on investing, choosing to measure the value of the project solely against the savings it would make in eliminating labour costs. Of course, in some cases, this saving alone is enough to warrant investment, but in others, the cost benefits are not quite as obvious.
Is the change from hand labelling to automation really all about labour savings though?
Some SME manufacturers have realised that this is not always an accurate yardstick to base a decision on. Why? Well, because decisions based solely on labour savings don’t account for other factors like risk and future growth.
Labour cost savings are usually significant
If you currently run your operation with hand labelling have you ever really analysed the true cost of the operation? As real time labelling technology improves beyond recognition, it’s an exercise more manufacturers are now undertaking, because the ROI on the transition to automation in many cases is now around 12 months or less.
First of all, let’s look at the human labour cost saving. Many hand labelling operations have their own print room; this means labels are printed and then supplied to another person in the labelling area - this internally puts a double handling cost on to the manufacturer. If you also count the time to proof labels, the labour cost alone can be significant, and historically this has been one of the main drivers towards automation.
There are also other obvious advantages, particularly if space is a premium. By moving to automation, there is an opportunity to decrease operational footprint, removing the hand labelling and print room area and put that space to better use.
Then, of course, there is the cost of label waste. Hand labelling requires labels to be pre-printed and if you are involved with batch printing with product dating on the label, there could be label waste on a daily basis.
OK, granted these are all obvious points, but what about the hidden cost?
The cost of risk
The true cost of hand labelling is difficult to factor in because risk is difficult to quantify. Human error will always exist in hand labelling operations, and the consequences can be extremely costly.
Human error is a revenue risk, but it is often commercially overlooked when decisions are being made to invest in Print and Apply because risk doesn’t physically impact the balance sheet; until a problem arises and by then the damage is done.
For instance, let's take a look at manufacturers who supply food products to supermarkets, where the implications of a wrongly or poorly labelled product can be very expensive.
If a product is wrongly labelled, or the label is damaged or doesn’t scan correctly, a whole delivery of stock can be returned to the factory. The cost of taking back a full delivery, inspecting and re-working the barcodes is expensive, and for short shelf-life products like dairy goods, sometimes the products are simply scrapped.
Is it worth the risk?
Protecting customer revenue
More importantly, though, the biggest concern for manufacturers with hand labelling is the cost of losing a customer due to consistent errors.
For ambitious customer-focused companies, the question many are now asking themselves is “What value do I place on retaining custom?” now that is a question that can be answered by referring to the balance sheet.
Financially, it is significant…
Removing the risk of human error, with 100% label verification and validation is certainly attractive. In fact, by removing risk, real time labelling automation could be viewed as a protector of customer revenue as much as an investment.
From a commercial perspective, multiple potential points of failure in hand labelling equate to multiple points of potential revenue loss. Indeed, the questions manufacturers with hand labelling operations should be asking right now are…
Who is controlling the labels you are printing?
Where are the label templates controlled?
Who is issuing the labels to the lines?
How do you know labels are printed correctly?
How do you know you are issuing the right labels to the line?
If you are not 100 % comfortable with the answers to the above questions, automation must be a consideration.
Growth drives automation decisions
Companies with growth plans, benefit from automation as it allows an uplift in speed and efficiency which can translate into fulfilling larger orders faster, more effectively and without error.
Let’s take the example of Essential Cuisine. As a leading UK provider of stock pots, Essential Cuisine, transitioned from hand labelling to real-time Print and Apply, after Jamie McGregor, Production Director of Essential Cuisine, recognised that their hand labelling operation was unsustainable to keep up with the growth of the company.
Jamie commented on the impact of the project
“Previously, on each line, we had to employ one person, four days a week to apply labels by hand. Now that we have automated the labelling operation, we no longer have that overhead, and the process runs more efficiently.”
Other companies who have also moved to automated labelling have reported dramatic results. Cheese manufacturer David Williams Cheese swapped their hand labelling operation for automation to accommodate growth and achieved 25% more output on the line with an 18-month ROI. Meanwhile, Egg production company, Glenrath Foods transitioned from hand labelling to real time Print and Apply with incredible 30-week ROI achieved.
Chris Hunt, UK Sales Manager for Print and Apply specialists Cobalt systems commented
“The transition from hand-labelling to real-time labelling can be complex, but with the right partner and advice, it’s an enormous commercial opportunity. Integration need not be a headache anymore as many systems are modular, space saving and can adapt to existing lines. It’s about engineering a solution that delivers maximum value, at lowest capital cost and with the greatest ROI to future-proof production plans.”
Innovation not replacement
In a busy factory, it’s often tempting to just replace equipment in a “like for like” manner and maintain the status quo. However, in today’s increasingly competitive environment can you afford to ignore innovative technology that could make a real difference?
As Chris Hunt stated
“Many companies just don’t have the time or specialist knowledge to analyse what Print & Apply solutions can do for their lines. This makes it difficult for them to evaluate the value an automated labelling project can deliver. The starting point is to get some genuine advice from a reputable company who could scope out a best-fit solution. At that point, the manufacturer can make a real commercial decision on a project against the value it can deliver.”
As more manufacturers look to evaluate their labelling operation, the question today should not just be about what savings can be achieved, but what the consequences are for not investing.
Change, of course, is never easy, but change, innovation and improvement embody the soul of British manufacturing, and this is what is driving the real time labelling revolution.
For more information, give Cobalt a call on 01270 539 800 or email the team sales@cobaltis.co.uk
For more information on The Real-Time Labelling Revolution: Why Manufacturers are Analysing the Hidden Costs and Risks of Hand Labelling talk to Cobalt Systems Limited
Enquire Now
List your company on FindTheNeedle.