
Sign In
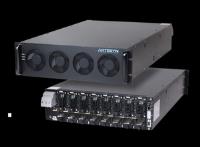
Adored for its intelligence and flexibility, the stunning Artesyn iHP series of power systems has, since its release in 2017, been well renowned for providing accuracy, resolution and stability as either a programmable voltage or current source in both medical and industrial settings.
Artesyn’s parent company Advanced Energy, in a recent study, certified these business gains by observing their product’s effects on operating expenses and capital expenditure in the horticultural sector and their findings are telling of how the iHP Series can improve the bottom line for your business.
The Study
The Artesyn line of products from Advanced Energy were designed specifically for driving high-power horticultural lighting fixtures and the name of the game here is minimising power consumption whilst maximising performance to keep systems powerful and efficient.
The difficulties for horticultural lighting stems from how crucial the control of light sources in ensuring high yields for farms. In the past, artificial lighting would require individual control systems for each luminaire as each power supply would need to precisely control the current to ensure the light is emitted at the correct wavelength to stimulate growth. The installation costs and cooling expenses would drive capital and operating expenditure through the roof!
In conventional power distributions, the heat generated by both the driver/power supply and the luminaire would need to be taken into account for cooling calculations, driving down that bottom line.
The iHP power supplies position themselves as a central current source to drive an array of LED luminaires. Using a large centralized current source outside growth areas and distributing power directly to all the luminaires leads to massive CAPEX savings as it eliminates the “doubling up” of power infrastructure. OPEX gains can also be had, as the current source can be placed outside of the environment-control area, allowing heat conversation to be controlled independently from the plants’ temperature control.
The ability of the iHP to supply higher voltages than individual control systems allows for reductions in installation costs with less insulation needed for wires, reducing wire size and cooling needs.
Artesyn observed the effects of their products in the US horticulture market, and the centralized power delivery model and found that using the iHP Series in LED grow light farms yielded a saving of $110k per year. This shows that the total CAPEX of these farms was recovered within three years of operation – this isn’t just the difference between the costs, but the entire power CAPEX for the whole system.
According to the manufacturer, utilising AE’s system allows end users to reduce their power conversion costs by as much as 50 percent, significantly lower installation and operating costs and increase the quality of crop yield.
In a statement released in December 2020, Joe Voyles, VP for Industrial Marketing at Advance Energy spoke of the iHP revolutionary gains for the horticulture industry[1]: “We are transforming our customers’ operations by both reducing the amount of needed equipment and improving the efficiency of the lighting systems, thereby reducing cost and energy spend. Not only do these innovative new products increase the efficiency and quality of fruit and vegetable production, but they also open the door to establishing indoor farming facilities in harsh environments anywhere in the world.”
The Product
The iHP is a highly configurable and intelligent high power system designed specifically for unrivalled control and accuracy in both medical and industrial applications.
Providing up to 24 kW in 3 kW increments, the iHP provides both the resolution and the high-power output needed for your critical application. With up to eight outputs, this power supply is perfect as a central node in any power delivery system and the ability to control the system both through analogue and digital methods affords engineers easy access for configuration.
Using Artesyn’s high level PowerPro configurable GUI, end users can seamlessly control and monitor all functions, including input and output variations, monitor system temperature and set time routines using a graphic script creation engine.
Digital control affords greater levels of scalability, as multiple iHP systems can be controlled simultaneously as routines and power variations can be synced or altered from one cloud-based access point.
Using an iHP system as a centralised power supply allows for simpler installation and makes servicing and repair much easier. The outputs can be configured as voltage or current sources and customised to the application’s requirements.
Outside of LED growth lighting, the iHP is perfect for medical settings, like pharmaceutical production where the programmable nature of the iHP allows for great precision to ensure safety and efficiency. Safety approvals secured by Advanced Energy eliminate the need for an isolation transformer in medical equipment.
The power rack house EMC filtering and digital front-end power factor correction circuits – allowing system designers to maintain the level of reactive power consumption and decrease the likelihood of power instability and equipment failure.
The modular design for output modules allows application specific modular development. Precision modules in development help provide low noise output for critical laboratory equipment.
For use with semiconductor processing equipment, AE have developed this product to meet the SEMI F47 standard, whereas the compact size and multi-rack paralleling capabilities makes the iHP perfect for large Megawatt installations for chemical processing or high-powered laser applications.
Billing itself as the heavyweight backbone to a highly configurable and efficient power delivery system, the iHP’s modular flexibility accelerates the speed of design cycles, shortens development time and allows for greater scalability, qualities that make it perfect for system designers as their next central PSU.
For more information on How this revolutionary power supply saves US farmers $110k a year and how it can cut costs for your business! talk to Components Bureau
Enquire Now
More News
List your company on FindTheNeedle.